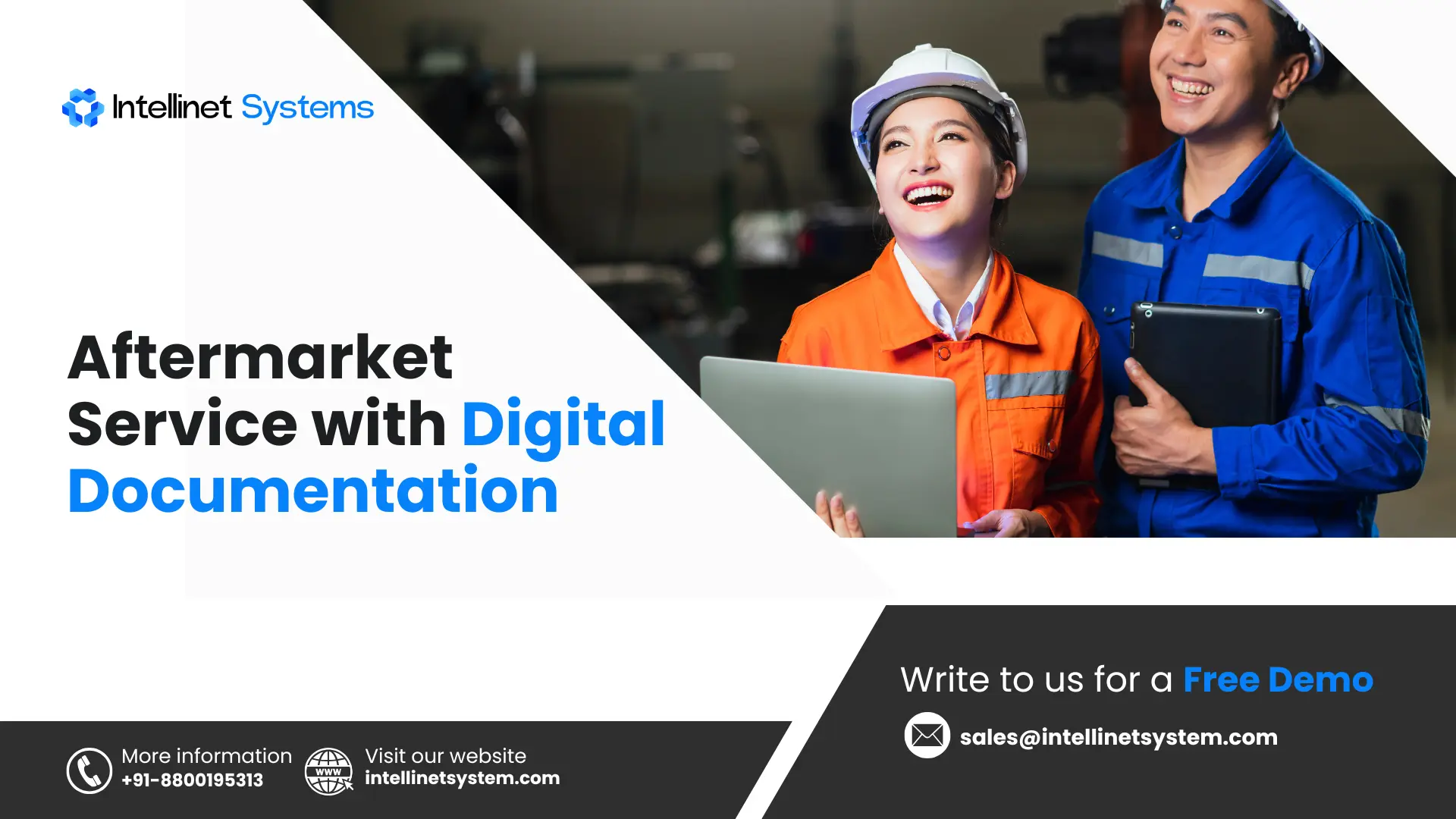
Original Equipment Manufacturers (OEMs) have depended on conventional technical documentation techniques for decades in order to maintain the efficiency of their aftermarket operations. However, the truth is that these traditional forms of documentation, such as static PDFs and paper-based manuals, cause more problems than they solve. These inefficient, non-interactive materials frequently lead to errors, delays, and higher operational costs. The switch to digital manuals is an important innovation that offers OEMs an opportunity to reconsider how they deliver aftermarket service.
To overcome this, digital methods of technical documentation are a revolutionary approach that uses interactive, cloud-based platforms in place of bulky documents. These platforms use AI, illustrative graphics, and real-time updates to empower users and optimize aftermarket processes. For OEMs looking to increase productivity, reduce errors, and maintain their competitiveness, these platforms are a lifeline rather than simply upgrades.
Through this article, we will explore how technical documents like digital service manuals help OEMs in transforming their aftermarket services and how solutions like digital manuals are reshaping the future of technical documentation.
Challenges with Traditional Methods of Technical Documentation
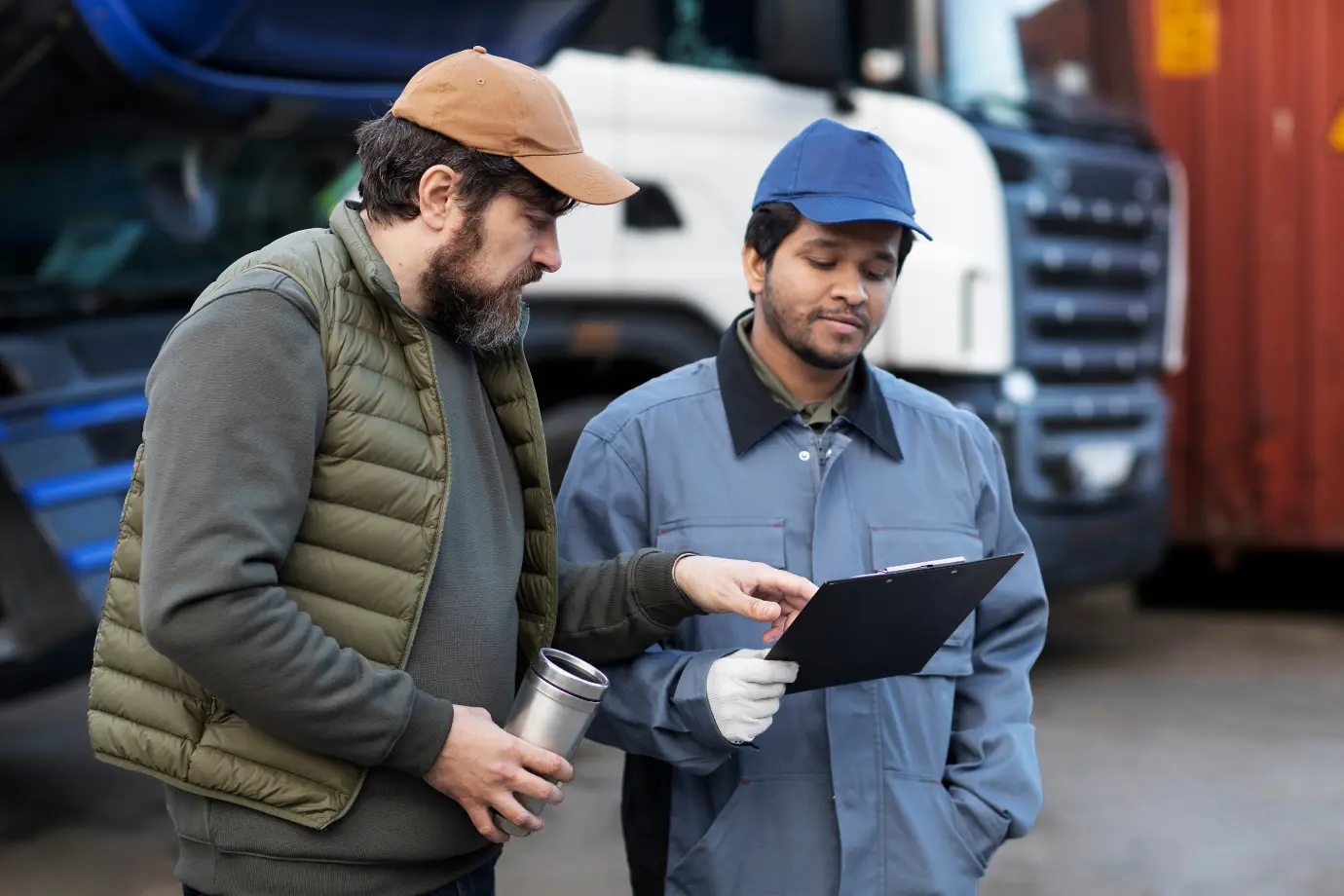
Although technical documentation is a critical aspect for OEMs that drives their success in the aftermarket, there are several challenges they face when following traditional practices. Traditional manuals are either paper-based or static PDFs, and handling them is a tough affair. Here are the significant challenges OEMs encounter during the traditional approaches to documenting technical information:
Lack of Interactivity
Paper-based manuals are bulky and non-interactive. Technicians waste precious time flipping through pages to find a single torque setting or part number. PDFs are marginally better but still static, with no clickable links or zoomable diagrams. Technicians often spend several minutes to sometimes hours searching a PDF for a specific repair guide. This precious time could have been spent fixing the vehicle or on more productive tasks.
Inefficient Processes
In aftermarket service, time is precious, and conventional technical documentation is a time-waster. Finding a specific method in a lengthy manual causes delays in repairs, which frustrates both dealers and customers. For the OEMs, updating these documents is even worse, as it might take several months to provide updated PDFs across their global network. In such cases, technicians are left operating on out-of-date specifications that lead to errors and further delays.
High Volume of Errors
Errors are inevitable with static paper-based manuals and PDFs. Technicians run the risk of misinterpreting instructions or following the wrong steps in the absence of clear visuals or real-time updates. In industries like aerospace and defense, where non-compliance can compromise safety, these errors are intolerable. These risks are only increased by outdated guides, compromising compliance and safety.
Rising Costs
Paper manual printing and shipping may be quite expensive, particularly for OEMs with dealer networks across the globe. Even PDFs have additional hidden costs since they need to be manually updated and redistributed. Then there is the environmental impact of piles of paper manuals. These expenses drain resources that might be better used for innovation or training.
Although these challenges are not new, they may be avoided. Digital manuals serve as an alternative, offering better, more efficient technical documentation that meets modern needs.
Must-Check Related Resource:
A Complete Guide to Interactive Electronic Technical Manuals (IETMs)
How Does Digital Documentation Solve These Problems?
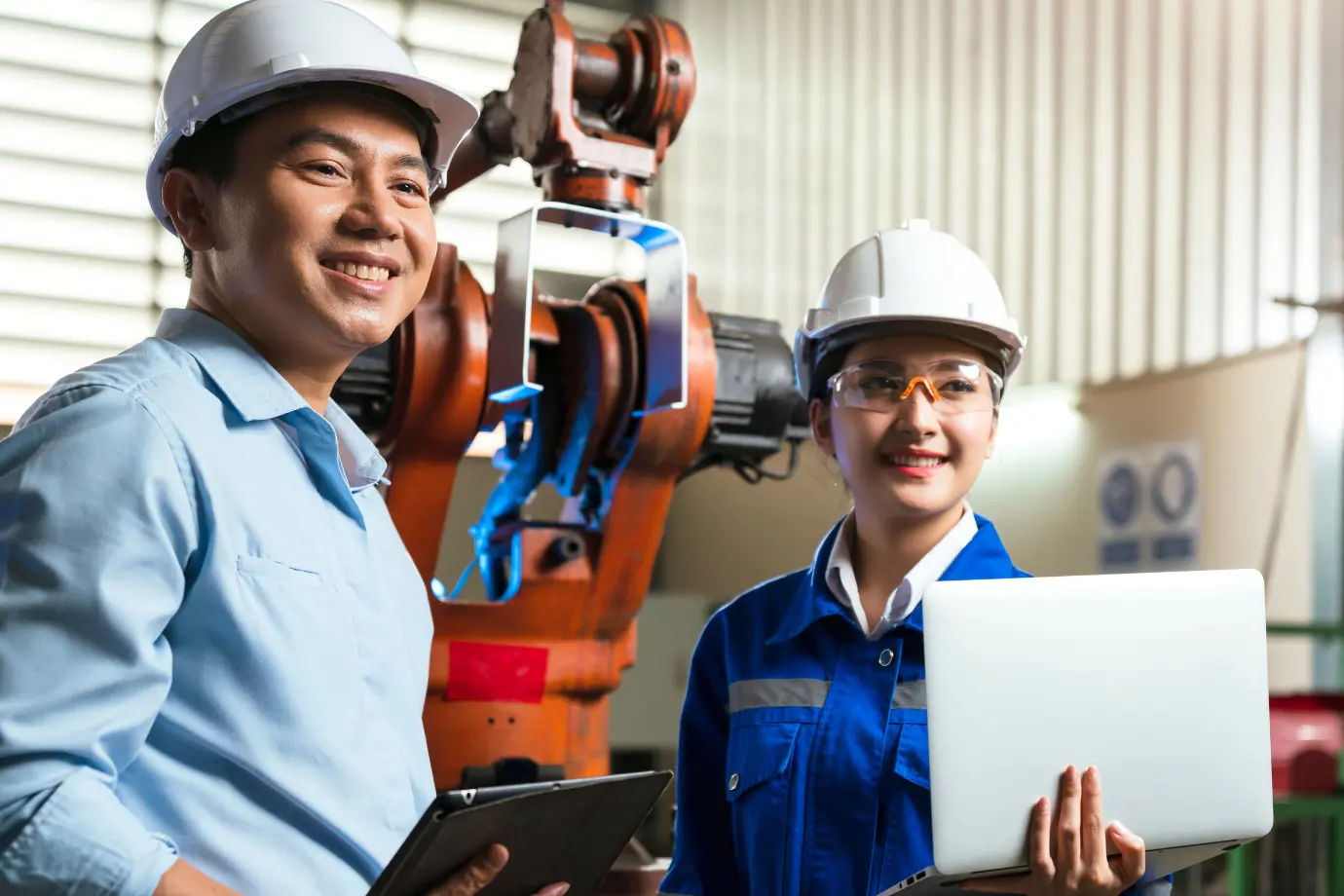
Digitization of service-related technical documentation turns the chaos involved with traditional service manuals into clear, actionable information. These instructions effectively address significant challenges involved with traditional manuals, such as non-interactiveness, inefficiency, errors, and costs. Instead of struggling with a 500-page guide or a static PDF, technicians can use these interactive manuals to tap into clickable menus or zoom into images, making complex repairs clear and easy to follow.
OEMs are at ease as cloud-based platforms eliminate the delays in updating manuals. Revisions, such as safety upgrades, are delivered instantaneously to worldwide teams through digital platforms, which was previously a months-long process. Additionally, digital service manuals eliminate the need for printing and shipping, saving OEMs thousands of dollars a year on this expensive endeavor. Beyond just addressing challenges, these manuals transform technical documentation into a seamless part of OEM’s workflow.
Benefits of Digital Technical Documentation for Aftermarket Success
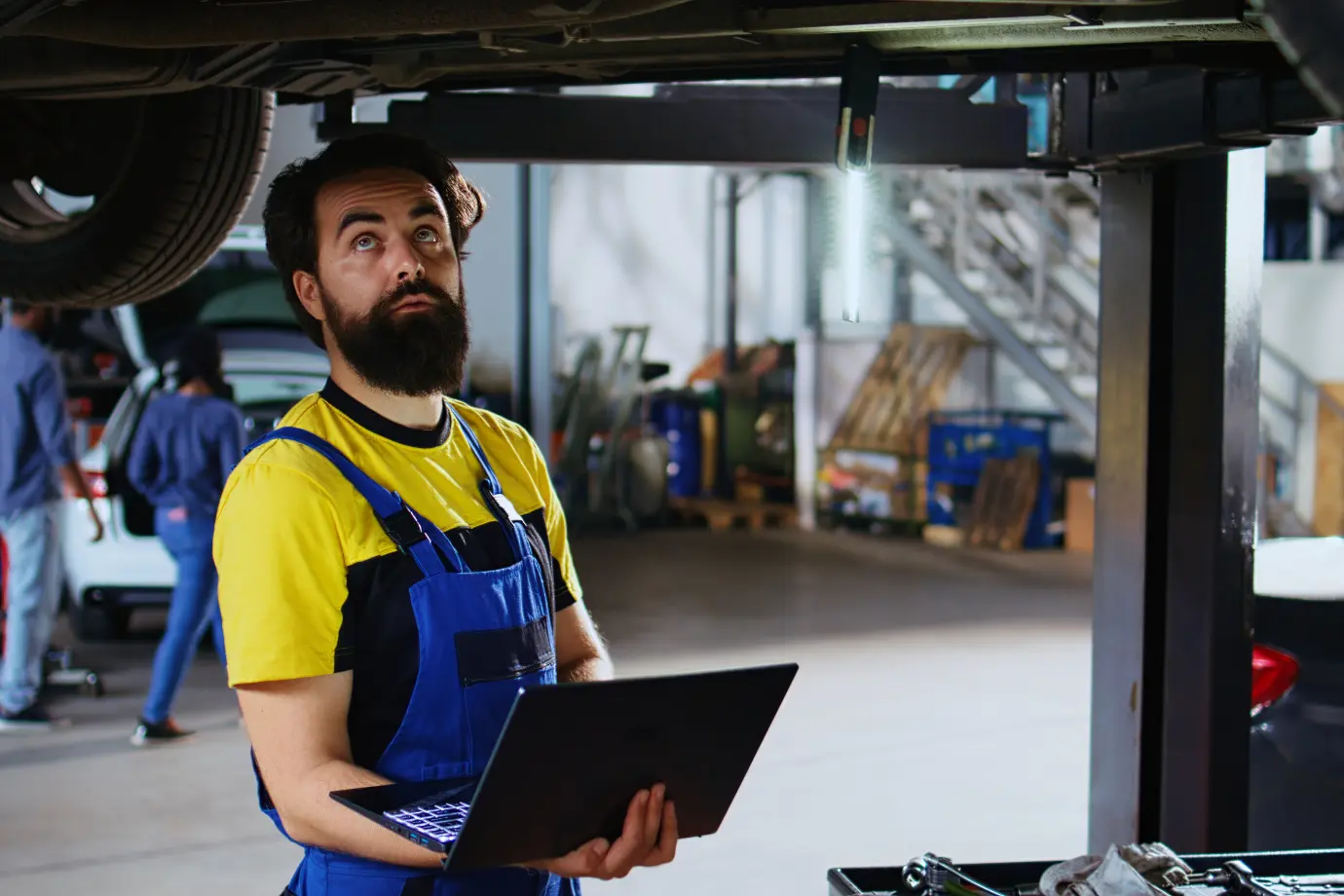
Digital manuals evolved Technical documentation that was earlier a logistical burden for OEMs into a competitive advantage. These manuals deliver transformative benefits that boost efficiency, accuracy, and innovation. Here’s why they’re essential for OEMs looking to succeed in the aftermarket:
Improved Efficiency and Productivity
Digital manuals save time. With AI-driven search and interactive navigation, technicians access critical information instantly. Service staff can take on more tasks and save downtime by using features like multiple search options. The impact of digital technical documentation on OEMs and their teams' productivity significantly increases overall output by 40%.
Reduced Errors and Improved Accuracy
Clear visuals are a lifesaver for technicians when they are midway through making repairs. Digital manuals include step-by-step instructions and videos to help avoid expensive errors. Real-time updates and feedback features in digital manuals ensure that documentation is accurate.
Cost Savings and Sustainability
The cost of producing and distributing paper-based and PDF manuals is high. Digital manuals eliminate those costs. Cloud-based solutions reduce paper waste and save time and money by providing real-time updates. OEMs can instead use these savings in new technologies or better training initiatives to expand their businesses.
Scalability and Smooth Integration
Growth shouldn't necessarily come with chaos. Because they are easily expandable, digital manuals are perfect for both small and large teams. These manuals ensure that technical documentation corresponds with inventory and service data when they are connected with systems such as SAP. This helps global OEMs in streamlining operations across countries by integrating the manual with their global service network.
Enhanced Training Programs
Training new technicians is tough, especially with complex equipment. Digital manuals simplify this training process by providing videos, FAQs, and interactive guides. Digital manuals' troubleshooting guides facilitate new hires' learning, and on-the-job training is supported by real-time assistance. By ensuring continuous service and reducing the learning curve, this is helpful for OEMs who are having trouble with a high turnover rate.
Why Intelli Manual Stands Apart?
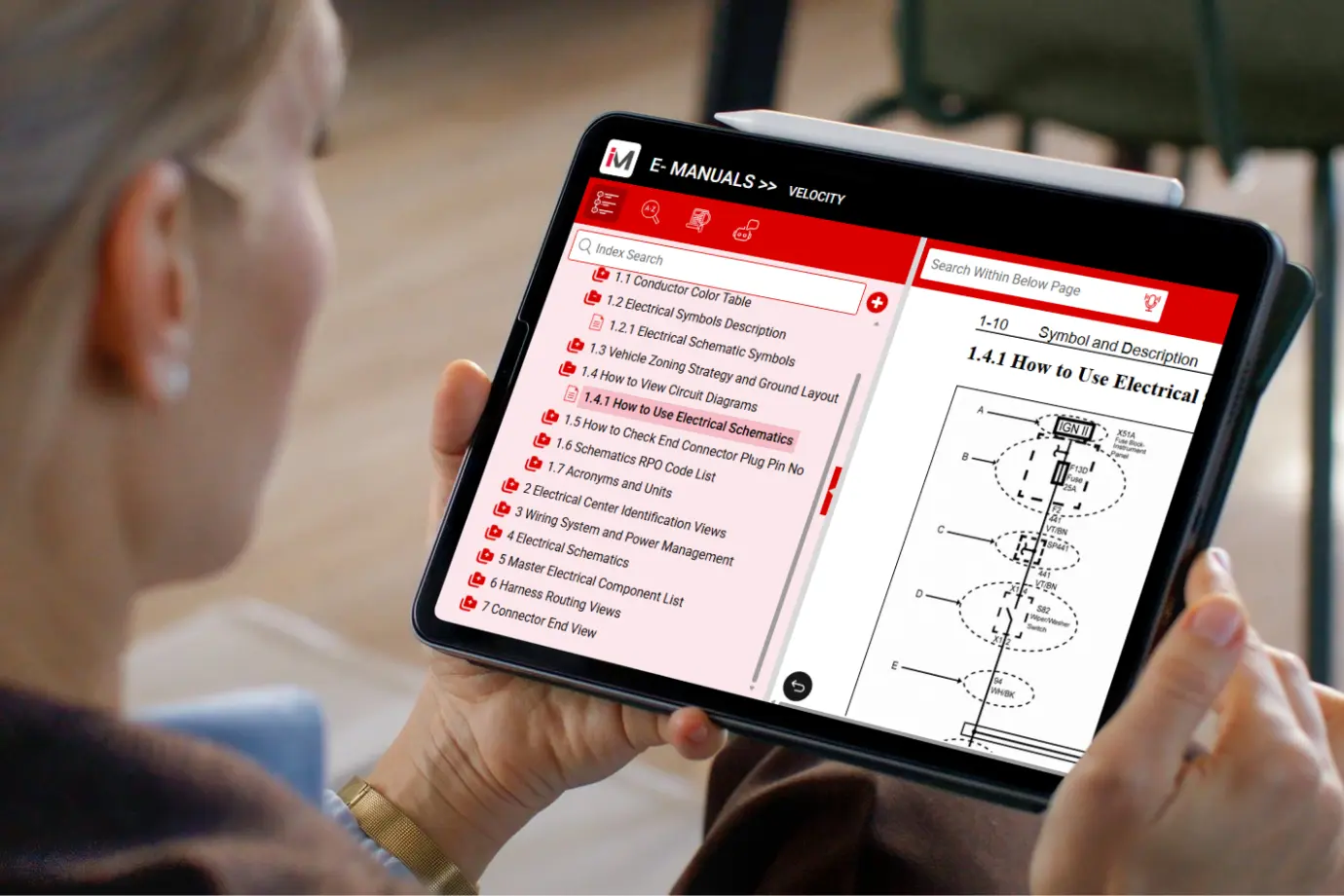
Intelli Manual is an interactive digital manual that makes technical documentation seamless. Beyond just a simple documentation solution, it is a revolution in digital technical documentation that is designed to address the practical issues of OEM aftermarket service. OEMs can convert their static PDFs into interactive HTML manuals that improve their usability and interaction.
Here is a list of offerings provided by Intelli Manual that make it a comprehensive solution for managing technical documentation:
Intuitive HTML Editor
Static PDF manuals are a thing of the past. Intelli Manual’s HTML platform turns service manuals into a dynamic tool. Technicians can switch between sections, bookmark pages, view a clear exploded image, or zoom into SVG images with ease. This clarity saves time and helps in eliminating hours of guessing involved with complex repairs.
Multiple Search Functionalities
Time is critical in the aftermarket, and Intelli Manual delivers speed. Several search options, such as keyword search, within-index search, page search, and full-content search, help technicians find answers fast.
Data-Driven Insights
Intelli Manual’s analytics provide OEMs with insights on how dealerships and their technicians use digital manuals. This helps OEMs identify the popular sections and the ones the users struggle with. OEMs can refine content based on real data, keeping manuals relevant. These insights help them streamline troubleshooting guides and cut repair times by 15%.
QR-Driven Video Access
Intelli Manual embeds QR codes linking to repair videos. It's that easy for technicians to scan a code and get detailed instructions. This function is extremely helpful for training new staff since it breaks down complex repair procedures into easy-to-follow stages.
Visual Reviews
This feature centralizes feedback and edits within the manual. Instead of making suggestions through the usual email threads, reviewers can directly highlight the section that requires an update, suggest the changes, and submit them instantly. This not only speeds up the review process but also helps OEMs in tracking changes with improved user accountability.
Scalable Platform
Intelli Manual is built for teams of all sizes, from early startups to global giants. The software integrates well with ERP and CRM systems through the cloud and streamlines data flow. Its pay-per-use model keeps costs manageable and is ideal for teams that are just beginning. OEMs can unify their dealer networks with Intelli Manual and boost service consistency worldwide.
How Does AI Further Improve Technical Documentation?
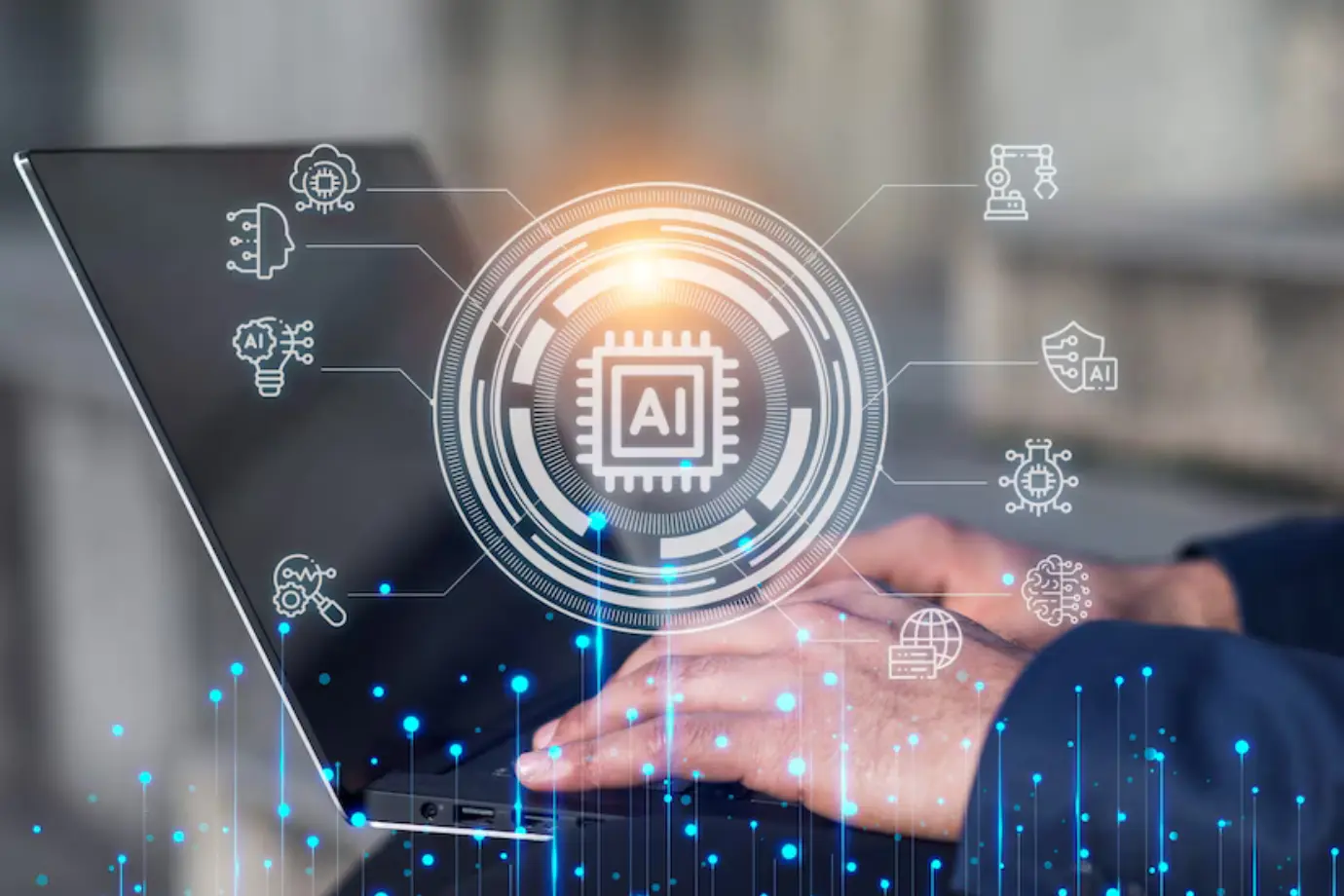
Technological advancements have upgraded technical documentation with time, and Artificial Intelligence (AI) has taken it to another level. To improve the functionalities of the manual, AI-assisted features were added to it, such as AI search, content summarization, and others. Let’s explore them in detail below:
AI-Assisted Search
AI-assisted search makes finding the needed information easier and quicker. Intelli Manual’s natural language processing allows technicians to enquire things like, 'What’s the fix for a cooling system leak?' and get a clear answer instantly. Its voice command feature ensures they need not slow down while working on the repair with greasy hands.
Chatbot Assistance
The AI chatbot in the manual makes it work as a 24/7 assistant for the technicians. It answers questions, suggests sections, and also guides new technicians through complex repair tasks. Such functionality allows even beginners to tackle their jobs with confidence. This reduces downtime and eases the load on senior staff.
Relevant FAQs
Intelli Manual’s machine learning abilities curate FAQs based on how dealers and their teams use the manual. It spots common questions, such as ‘How do I reset this sensor?’ and provides quick answers. This saves time and keeps technicians moving. By anticipating the actual needs of users, the manual fulfils their real needs.
Feedback Loop
Intelli Manual’s Smart Feedback lets technicians flag unclear sections, feeding insights back to OEMs. This keeps technical service documentation accurate and relevant.
Content Summarization
Long manuals can overwhelm technicians and make things confusing. AI generates clear and concise step-by-step summaries of complex procedures that are easier to understand. Such clarity is critical when technicians are working on urgent repairs, like a production line fix. This functionality becomes the basis of distinction between a quick repair and a costly delay.
Artificial Intelligence turns digital manuals into innovative tools that adapt to OEM’s business needs. Intelli Manual’s AI features make technical documentation a competitive edge for OEMs, driving efficiency and innovation across their aftermarket services.
Takeaways
Digital technical documentation is a must for OEMs to maintain efficiency in their after-market services. Paper and PDFs can’t keep pace in the modern, demanding markets as they’re slow, error-prone, and costly. Digital manuals like Intelli Manual change that, offering AI-driven search, 3D visuals, and QR-linked videos to boost efficiency and accuracy.
Its analytics and feedback keep manuals functioning, while secure cloud access supports global teams. AI takes it further with intuitive search, chatbots, and accurate summaries, making technical documentation a strategic asset for OEMs in the aftermarket. The results are real as OEMs notice a significant boost in their service efficiency with Intelli Manual.
Connect with our experts to learn how Intelli Manual can transform your aftermarket operations or request a free demo today.
Explore More Insights
About the Author
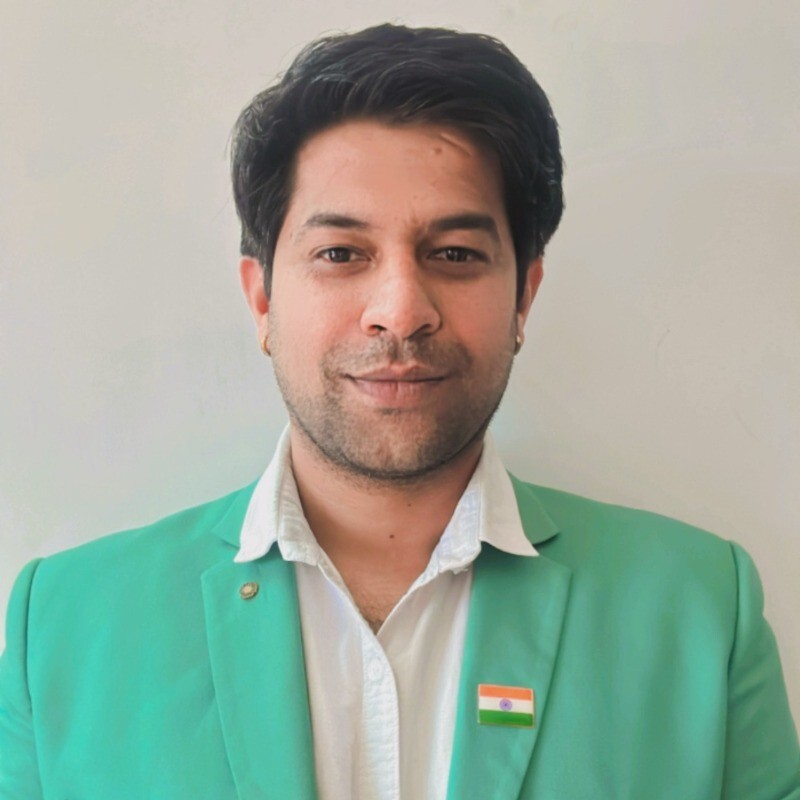
Chandra Shekhar
Chandra Shekhar is the Senior Manager, Strategy & Business Development at Intellinet Systems. With over a decade of experience in the automotive industry, Chandra Shekhar has led digital transformation and aftersales strategy initiatives for OEMs across multiple markets. His background combines deep industry knowledge with a practical understanding of how technology can solve real operational challenges. He focuses on making complex ideas clear and relevant for automotive and aftermarket professionals navigating ongoing change.