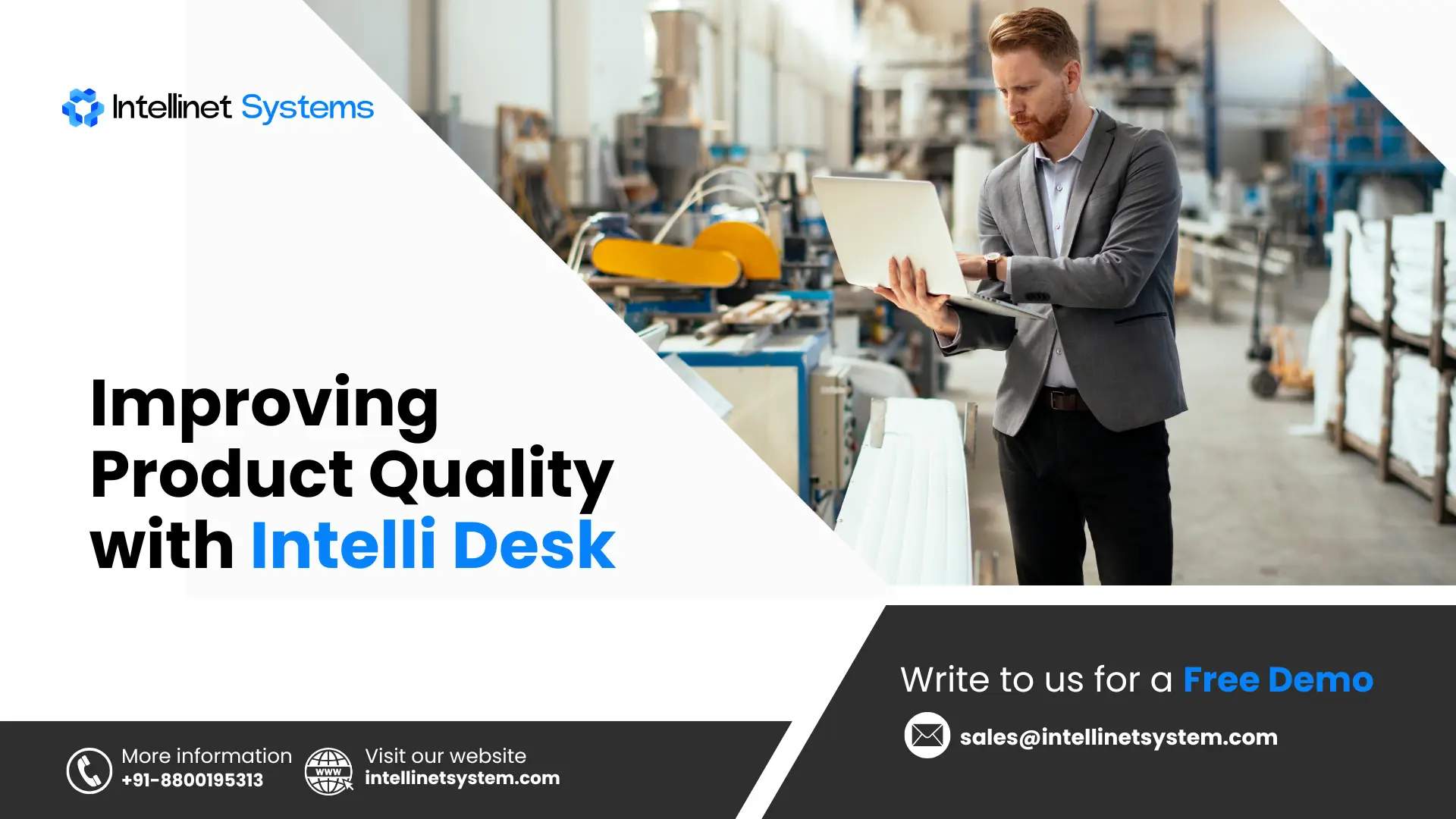
Original Equipment Manufacturers (OEMs) struggle with delivering top-notch product quality while juggling tight profit margins, demanding customers, and complex supply chains. Traditionally, technicians spend hours scanning over paper logs to figure out why a batch of parts failed in the field.
Today, the stakes are higher for OEMs as defects lead to costly recalls, unsatisfied customers, and a deteriorated brand reputation. Issues like poor field issue management and a lack of visibility into the causes of incoming problems only make things worse.
That’s where Intelli Desk comes in. This technical support software isn’t just a tool; it’s a game-changer for product quality improvement. It helps OEMs to dig into the root causes of problems with data-driven precision and stay ahead.
Through this article, let’s understand why improving product quality matters to the OEMs, the barriers they face during root cause analysis, and how Intelli Desk turns this disruption into an opportunity.
Need for Product Quality Improvement for OEMs
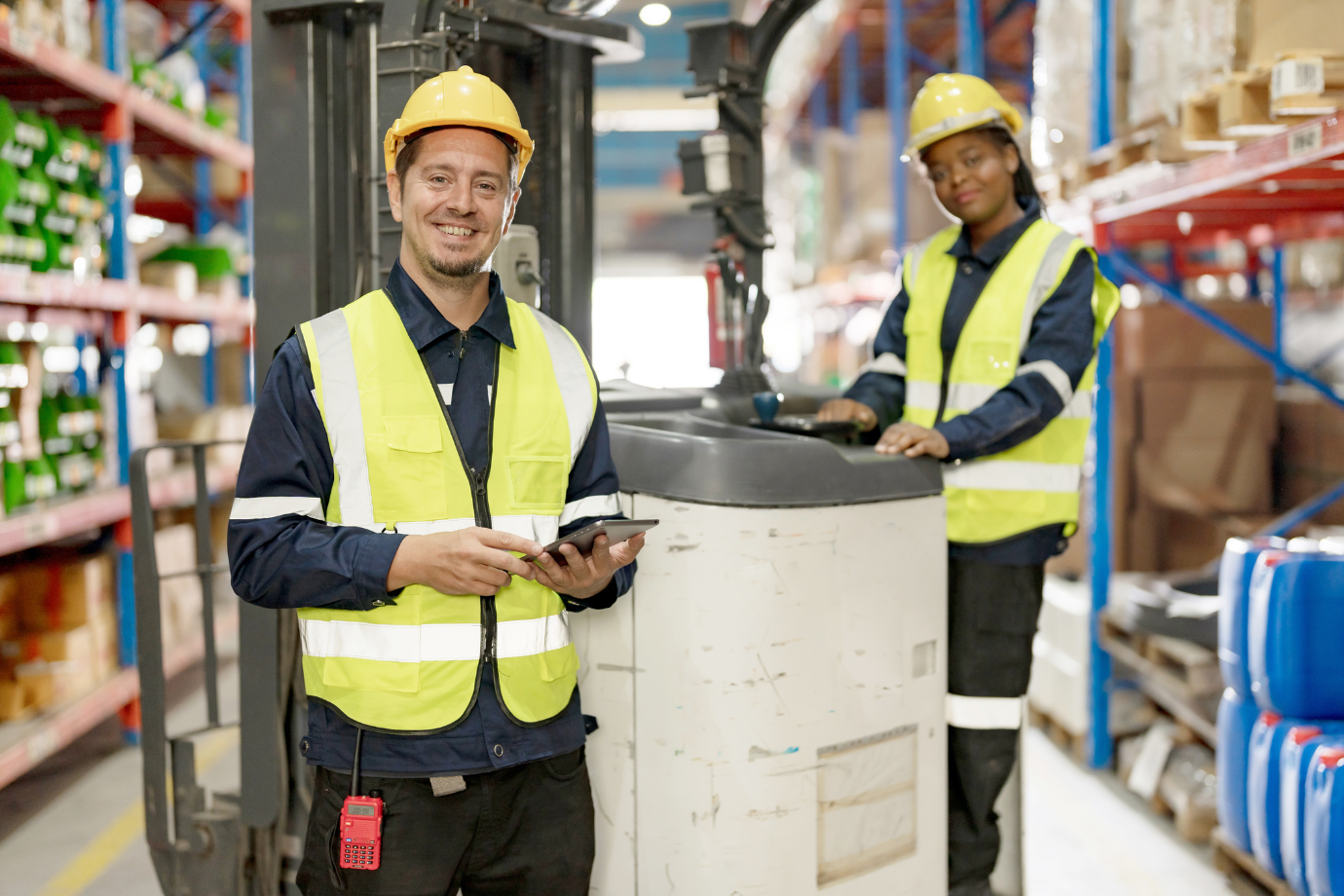
More than just a tag in the aftermarket services, product quality is an OEM’s lifeline. When a part fails, it’s not just a single machine that’s down. A customer’s trust, a distributor’s reliance, and the manufacturer’s profit margins also take a hit.
In the worst cases, when a poor quality product involves safety threats to the user, it may lead to product recalls and drain immense resources. That’s the kind of trouble poor product quality brings to the OEMs.
For OEMs, product quality improvement means fewer warranty claims, stronger dealer partnerships, and a brand reputation that opens opportunities. It’s about delivering parts that work every time, whether they’re in a tractor or a turbine. With global competition fiercer than ever, settling for ‘good enough’ isn’t an option.
Why is Root Cause Analysis Necessary for Improving Product Quality?
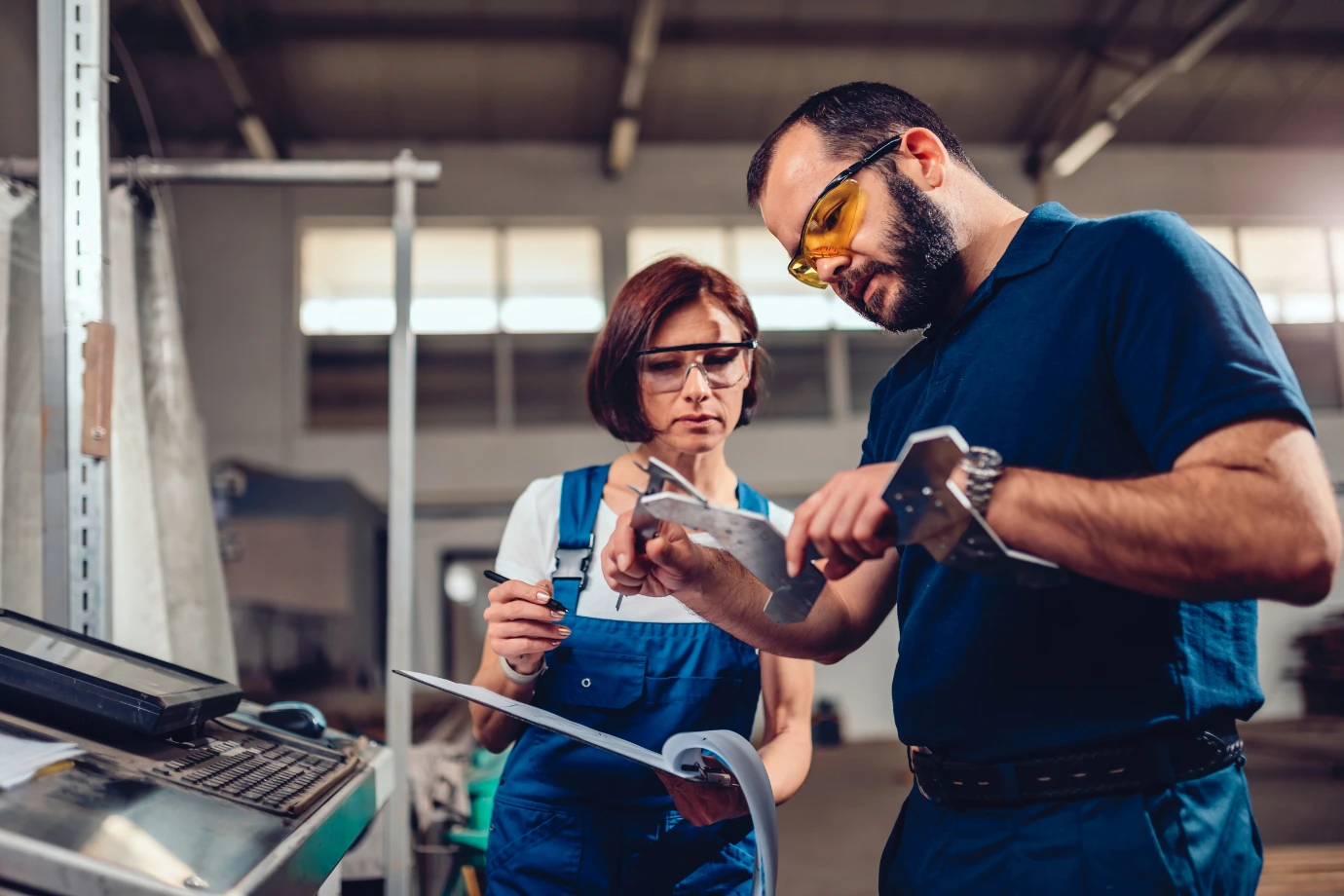
In the spare parts world, just fixing issues is not necessarily enough. A customer walks into a dealership complaining about a leaking seal, and they can’t just make a replacement without knowing why it failed. That’s where the need for root cause analysis comes in.
Root cause analysis is a process that helps OEMs track the actual origin of a defect, whether it’s a poor batch of raw materials or a badly calibrated machine. This process is the backbone of product quality improvement because it helps OEMs prevent field issues from recurring.
Without analyzing the root cause, OEMs remain stuck in a cycle of field failures and frustrated clients. But the reality is: conducting root cause analysis manually using traditional methods is a struggle among paper trails, guesswork, and endless meetings.
Challenges OEMs Face During Product Quality Control
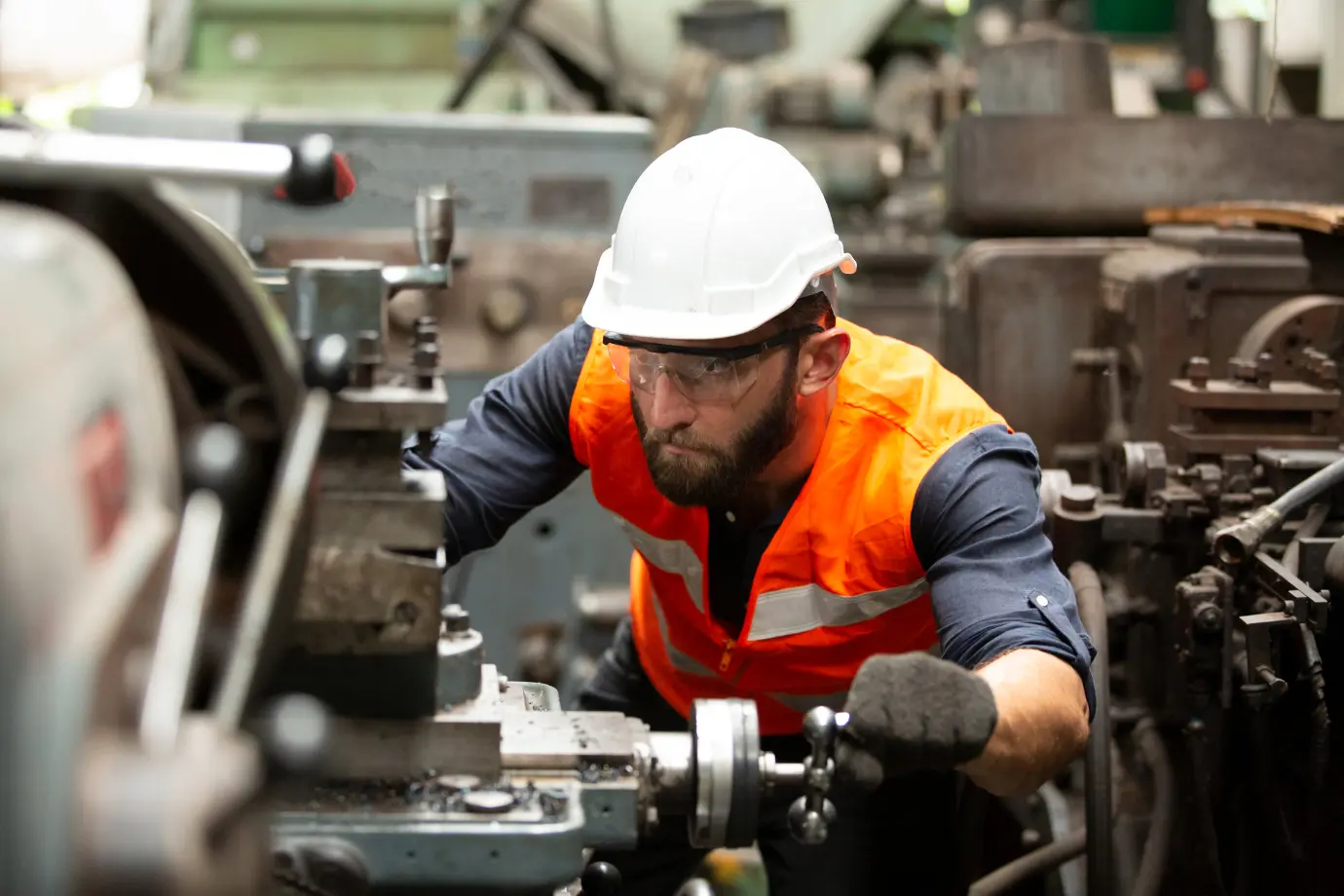
Running quality control in the spare parts market is a task that is more difficult than it seems. OEMs face many challenges that make ensuring consistent quality tough to achieve, including:
1. Data Silos
As different departments use several platforms for documenting data, the issues get scattered and are highly disorganized. While the back office team communicates over email, the service manager might work on spreadsheets. This makes it difficult to pull out the right information when needed.
2. Field Issue Management Hurdles
Customer complaints about failed parts often get buried in inboxes or lost in internal translation between technicians and engineers at the dealer’s workshop. It may take weeks before a critical issue gets noticed, shooting up costs and the number of incoming complaints.
3. Outdated Tools
Some OEMs may still rely on spreadsheets or cumbersome systems to record field issues. Although these methods were widely used earlier, they can’t handle the complexity of modern supply chains. Also, to get the latest updates and have a fair understanding of what’s going on, teams need to communicate frequently.
4. No Real-Time Visibility
When OEMs do not have instant access to field issues data, they are unable to spot patterns and recurring defects early. This allows persisting issues to intensify, which may later turn up as a product concern and lead to costly recalls.
For the OEMs, more than just causing inconvenience, these challenges drain profit margins. Modern technical support software like Intelli Desk helps OEMs deal with the messy challenges of product quality improvement. By making root cause analysis faster and smarter, this software provides OEMs with the edge to build better parts and keep customers coming back.
How Does Intelli Desk Facilitate Product Quality Improvement?
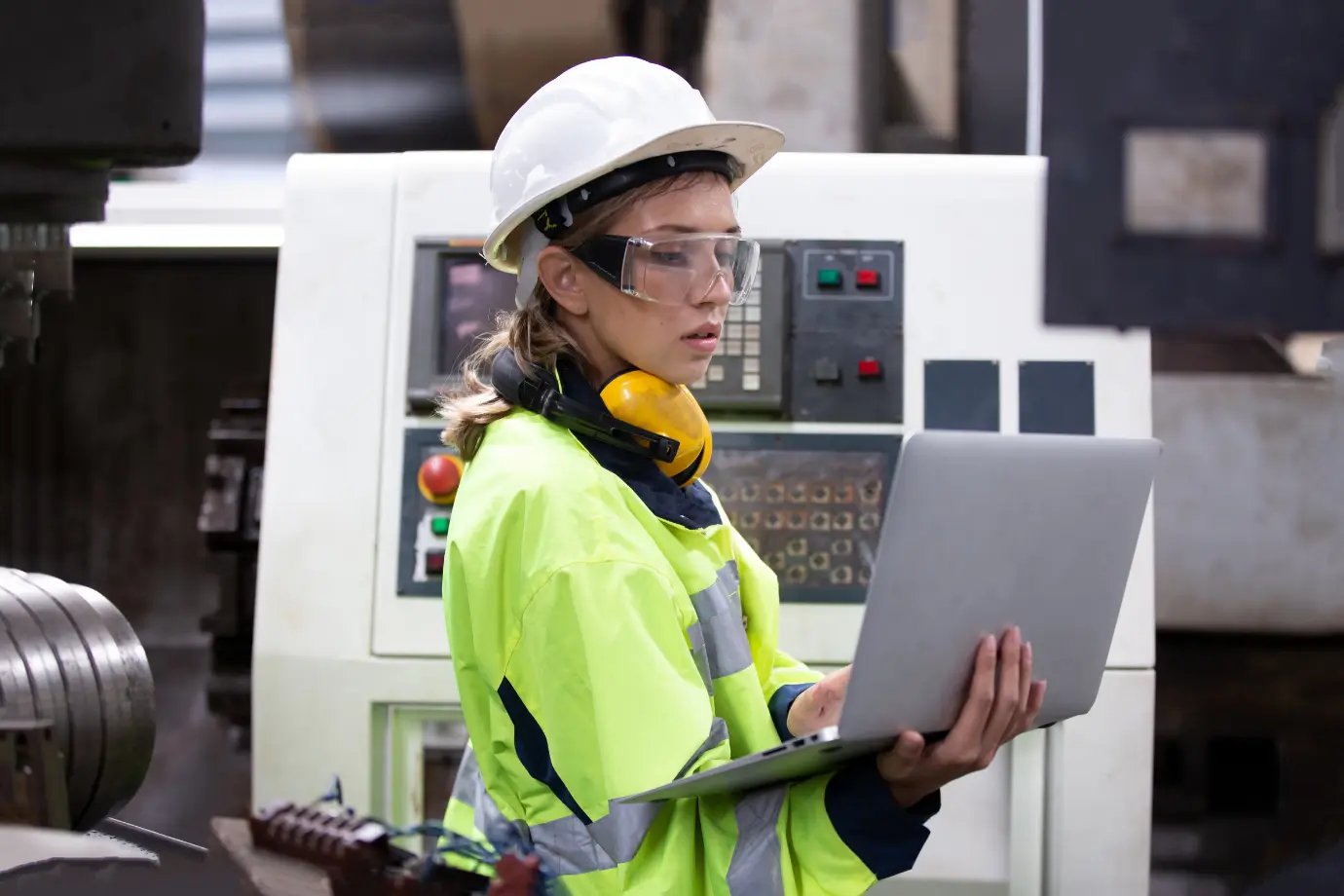
Intelli Desk is a technical support software that helps OEMs streamline their field issues, provide quick resolutions, and prevent future warranty disputes. It’s the kind of tool that tackles OEM challenges head-on, turning quality control from a headache into a strength. Here’s how it makes a difference:
1. Mastering Field Issue Management
Intelli Desk pulls customer complaints, field failure reports, and warranty claims into one place. Its automated workflows overcome the need for chasing emails or decoding handwritten notes. Such a streamlined process cuts resolution times, reduces costs for OEMs, and keeps customers happy.
2. Smart Analytics
Intelli Desk uses advanced analytics to spot patterns in data, like a spike in failures tied to a specific supplier, allowing OEMs to act fast.
3. Real-Time Insights
Dashboards that get updated in real-time give a clear view of what’s happening, right from production lines to field performance. It eliminates the need for frequent meetings and follow-ups across different departments.
4. Team Alignment
It connects dealerships, service managers, and back office teams to ensure everyone is in sync and working on the same data.
Instead of just fixing field issues, Intelli Desk helps OEMs in preventing them. This allows them to drive product quality improvement that is visible as cost savings and customer satisfaction.
Using Intelli Desk For Root Cause Analysis
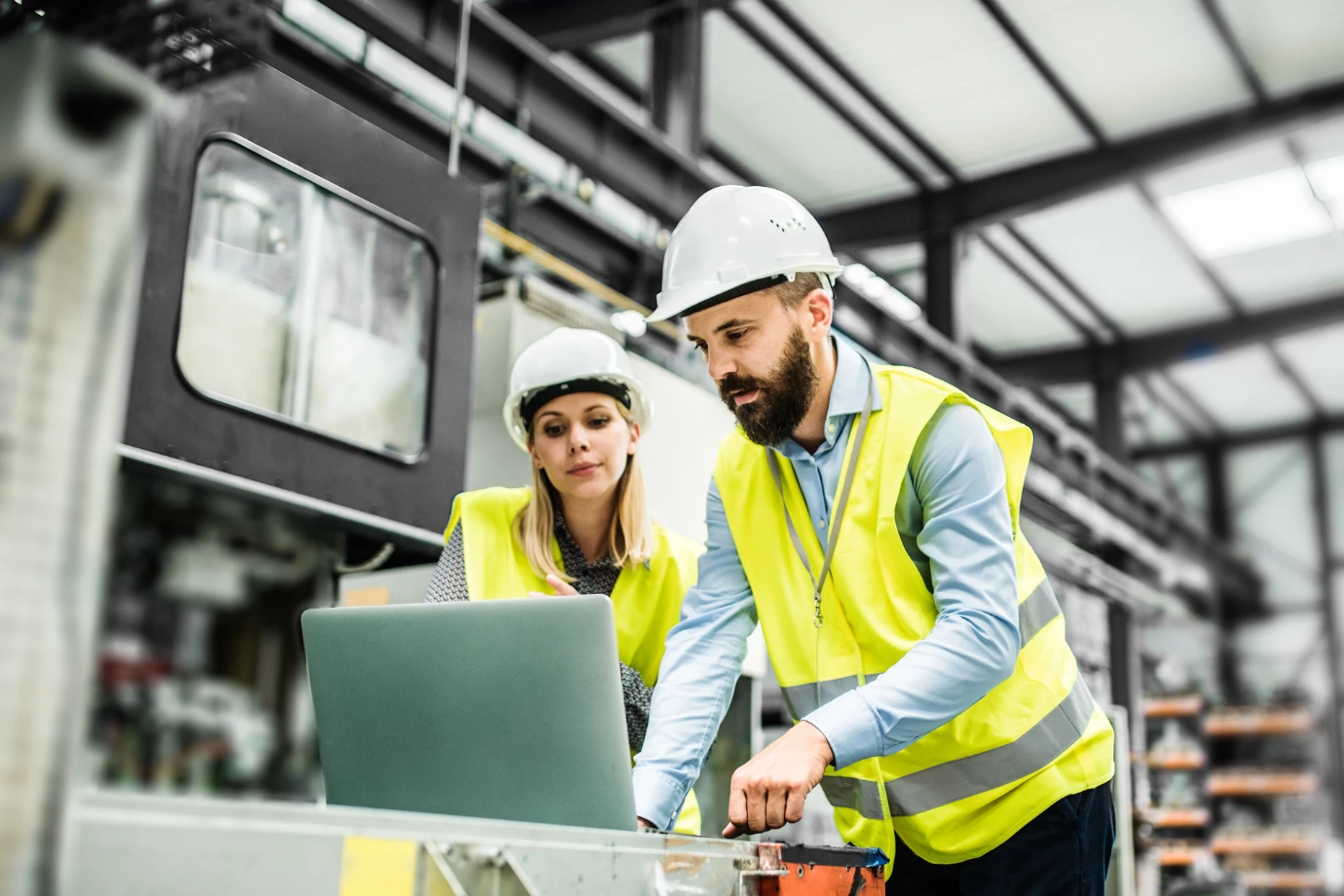
Traditionally, root cause analysis meant huddling in a conference room and having endless discussions around how field issues can be fixed. It worked, but it was slow, and teams missed things. A technical support software like Intelli Desk changes this scenario, making root cause analysis faster and more accurate.
For better understanding, let’s consider an example: A customer reports a bearing failing in a heavy-duty pump for which the dealer is unable to provide a possible solution. Here’s a detailed guide to using Intelli Desk for root cause analysis:
1. Log the Issue with Precision
The representative at the dealer’s end can start the documentation to generate a Technical Assistance Report (TAR) by recording the issue in Intelli Desk. The software enables users to log details like part number, failure mode (e.g., overheating), and customer impact. They can also attach photos or videos to support their observations. This TAR is forwarded to the service managers for review.
2. Collect Data
Intelli Desk pulls in everything you need, including production records, supplier guidelines, support tickets, and field data. Considering the bearing failure example, it might show the batch number, machine settings, and past complaints about similar parts. The software assimilates data from integrated systems like ERP and CRM, so users are not stuck hunting for required information.
3. Inspect Root Causes
Based on their experience and expertise, the service manager will find a possible solution to the problem and will revert to the dealer’s workshop. In case they are unable to find a suitable solution, they would inspect the historical data further. Based on this analysis, service managers can detect patterns in incoming issues and document their findings. They may compile several TARs to create a Field Technical Report (FTR), add their comments, and forward it to the OEM’s back office team.
4. Implement Solutions
Once the cause is identified, a faulty heat treatment in this example, the back office team can assign corrective actions in Intelli Desk. It can include switching suppliers or making modifications to product design or manufacturing. This technical support software lets users set tasks, deadlines, and accountable persons, with notifications to keep everyone on track. Considering the bearing example, they might task the procurement team to audit the supplier and the engineering team to update the design. Intelli Desk also tracks end-to-end progress, eliminating the need for micromanaging.
5. Verify and Prevent Recurrence
After the solutions are executed, Intelli Desk monitors their outcomes. Users can set alerts for similar failures or track key metrics, like defect rates, to ensure the problem is resolved completely. For the bearing example, OEM can analyze field data to confirm no new failures. The software also allows users to document these solutions by building a knowledge base for future root cause analysis. This step is critical as it prevents the same issue from popping up again and closes the loop.
6. Engage Stakeholders
Intelli Desk allows OEMs to share their findings with their internal teams, suppliers, and dealerships. For example, they could send a report to the pump dealer showing how they fixed the bearing issue and rebuild trust with them.
Intelli Desk’s intuitive interface allows service managers, support staff, and even field technicians to contribute, making root cause analysis a team effort. This technical support software saves OEMs from countless headaches and drives product quality improvement with every step.
Benefits of Using Intelli Desk for Product Quality Improvement
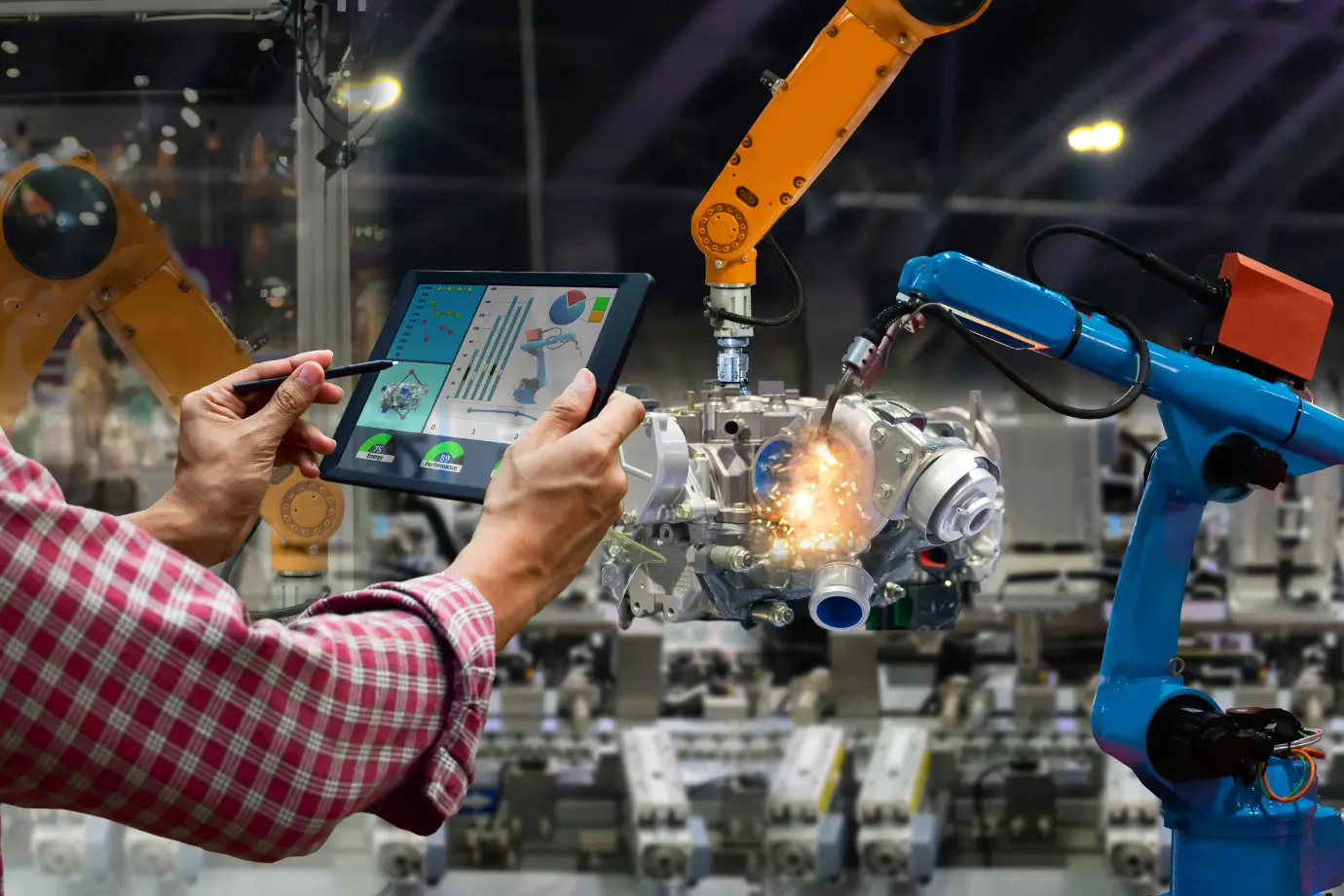
Intelli Desk delivers several benefits for OEMs to improve product quality, such as:
- Faster Issue Resolution: Automated root cause analysis and field issue management cut resolution times, getting parts back in service quicker and reducing downtime.
- Improved Parts Quality: Fewer defects mean higher reliability, which translates to happier customers and stronger relationships with dealers.
- Lower Costs: Finding the root cause early helps OEMs in reducing rework and warranty claims and saves on costs.
- Smoother Field Issue Management: Centralized tracking and real-time data ensure customer complaints don’t spiral into trouble.
- Scalability: Intelli Desk adapts to OEM’s growing business needs, so they don’t need to worry about working in global supply chains.
More than just providing business benefits, this technical support software empowers OEMs to build quality parts and keep customers satisfied.
Takeaways
As a technical support software, Intelli Desk tackles the toughest challenges OEMs face in improving product quality. Ranging from messy field issue management to complex root cause analysis, these challenges lead to high operational costs and drain OEM’s brand reputation.
By pulling data together, streamlining processes, and empowering teams, Intelli Desk drives product quality improvement that shows up as increased profit margins and higher customer satisfaction. Using this tool helps OEMs transform their operations and turn challenges into opportunities.
Want to see product quality improvement in action? Connect with our experts to know how Intelli Desk can help you in product quality improvement or request a free demo today.
Explore More Insights
About the Author
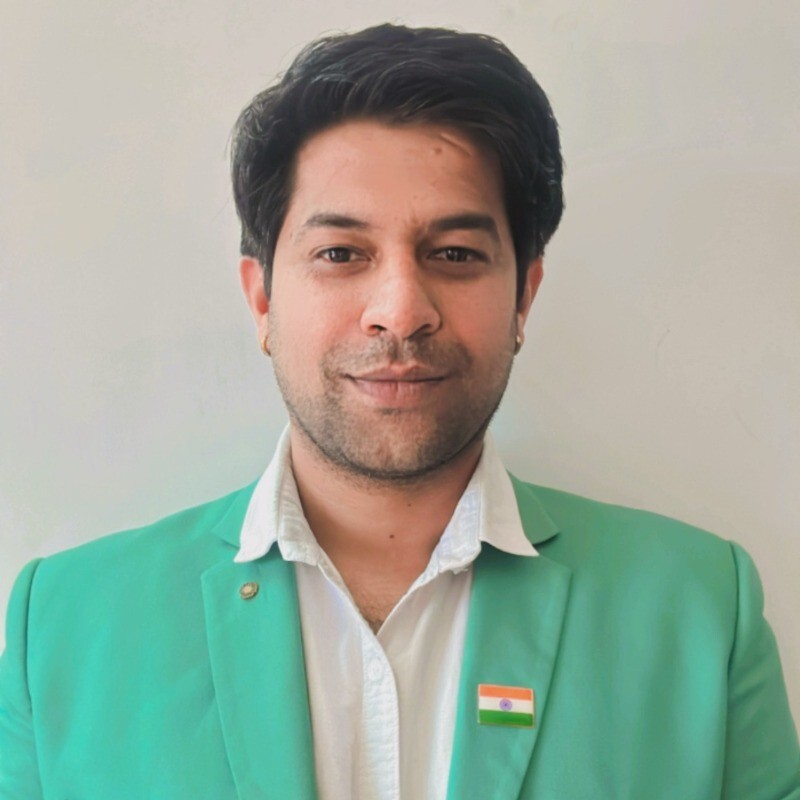
Chandra Shekhar
Chandra Shekhar is the Senior Manager, Strategy & Business Development at Intellinet Systems. With over a decade of experience in the automotive industry, Chandra Shekhar has led digital transformation and aftersales strategy initiatives for OEMs across multiple markets. His background combines deep industry knowledge with a practical understanding of how technology can solve real operational challenges. He focuses on making complex ideas clear and relevant for automotive and aftermarket professionals navigating ongoing change.