Equipment manufacturing organizations invest billions of dollars worldwide in planning, management and other computerized systems to meet their maintenance and reliability goals. Yet, many fail to ensure that systems data is accessible easily to maintenance personnel. Without an adequate illustrated parts catalogue they will fail to boost the business. It is simply not possible to be strategic, and continuously improve operations without valid software like auto parts catalog.
While auto parts catalog is a necessary component of their day-to-day responsibilities, most maintenance personnel ignore information section. Finishing detailed, accurate, and timely notifications, work orders, and work order close-outs in their enterprise system rarely ranks as a top priority. Often, technicians skip steps, or omit critical details that business requires to properly maintain assets, ensure the safety of its parts, and true dependability considers.Productivity is the dream when comes to managing a work order. It is essential to have the capacity to rapidly discover and visualize your benefits, parts and equipments. Organizations are as yet utilizing antiquated techniques for finding resources and parts. They depend intensely on effective spare parts administration to decrease costs and to keep operations running effectively.
However, there are numerous ways to increase wrench time in progressing support and cut operations cost by giving better representation of information to the maintenance personnel.
When equipment breaks down or requires routine maintenance, maintenance personnel need to be able to figure out what spare parts are required to complete the work, spare parts information from an illustrated parts catalog to make plans, errand records, or bills of materials. In case that parts books are lost, or put away at an alternate location, acquiring the right data can be an exceptionally tedious. This result in money and time lose, and can result in crucial mistakes. Moreover, it might lead to requesting of wrong stock.
In many organizations, when maintenance personnel come across a work order, they begin via hunting down the merchant documentation. These records are commonly available in paper, on a server, or in some separate form. Consequently, you initially should guarantee all merchant records are updated and then proceed to figure out which parts are required for the repair. It's a tedious assignment. Once you've distinguished from illustrated parts catalogue which parts you required to finish the work, still you have to arrange the parts.
Normally it's a different wing of an organization that is in charge of inventory and acquisition of parts. In many organizations, the maintenance personnel that need part don’t have access to that wing. They just give the merchant data to the procurement group and let them manage it all alone.Issues normally emerge as that wing can't discover a part that as of now exists in the system. What is the reason of that? Here are the most widely recognized situations for such issue:
- Information may have been entered inaccurately or deficiently due to hurry in request process.
- There is no proficient method to scan your acquisition framework for potential coordinating parts.
- There may not be sufficient data to check that parts found are similar as asked.
The parts might be in stock or they may require to be ordered. Info on where and how to acquire the parts might be set up in the framework or, more often than not, it might be important to submit a surge request for the part. Generally, it results in double entries of parts into the framework and costs extra. Moreover, parts list in your computer system is frequently loaded up with conflictingly named parts, duplicity, out of date parts and other terrible data. This procedure happens again and again, and bringing pointless deferrals, downtime, costly acquirements, and much more.
Also, maintenance personnel regularly need to locate spare part in large facilities, and waste time in physically hunting down equipment in a new territory. Illustrated parts catalogue helps you in exploring through a huge space warehouse to find a particular piece of spare part. You can rapidly find spare part or areas, decreasing the time spent searching. Invest more energy performing support, and less time searching for needed part.
Access Parts Books and Maintenance Manuals Faster Maintenance personnel don’t need to waste time in search for parts in manual catalogue. By having the right data readily available through illustrated parts catalog, save time in finding part numbers, and diminish issues while searching the right parts. At the point when maintenance plan and undertaking records refer to right parts, workers can more effortlessly identify duplicate and out of date stock, and reduce their dependence on manual procedures for material orders.Auto parts catalog coordinates with all major interfaces straightforwardly from a work request to illustrated Parts Catalogue for a spare part. You can outwardly choose a part from a detonated parts chart and rapidly select the part to be added to the work order. You would then be able to determine amounts, and refresh the work orders consequently, decreasing mistakes.
Auto parts catalog enables you to solidify all asset related documentation, including illustrated parts books, graphical manuals, and building reports into a solitary, dependable source, and integrating these records specifically to an asset. You can stack electronic parts books from illustrations and diagram to parts in a list, making it simple to find part numbers.
Illustrated parts catalog gives simple access to all data in a solitary place connected to all features, laborers will eventually spare torque time. With everything taken into account, you execute work order quicker and invest less energy searching for parts and data, and additional time executing work. Customers looking for a solution to help them guide in their maintenance plan, supply chain, and reliability operations can simply take services of illustrated parts catalogue. Having an experience of a decade in providing software to equipment organization and helping them in boosting their business Intellinet is well known for its illustrated parts catalogue and other important software.
For more queries about the software please click here
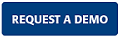
Explore More Insights
About the Author
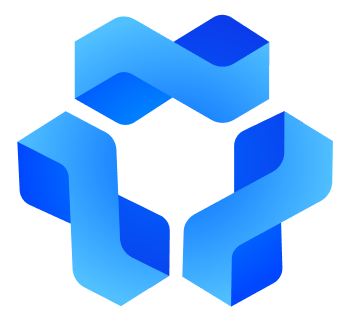