Inspecting products for the last time before they are out for delivery is necessary for manufacturers to ensure they are free of flaws. This pre-delivery inspection process verifies the product quality and helps OEM identify existing flaws or shortcomings.
However, the traditional methods of inspections involve manual processing, extended paperwork, and are prone to errors. This not only slows down the inspections but also involves the risk of omitting the underlying defects and errors in the product. A digital inspection software like Intelli PDI helps manufacturers mitigate these challenges and improve delivery efficiency.
Through this article, we will explore in detail the difficulties OEMs face in conducting pre-delivery inspection and how they can overcome them using Intelli PDI.
What are Pre-Delivery Inspections?
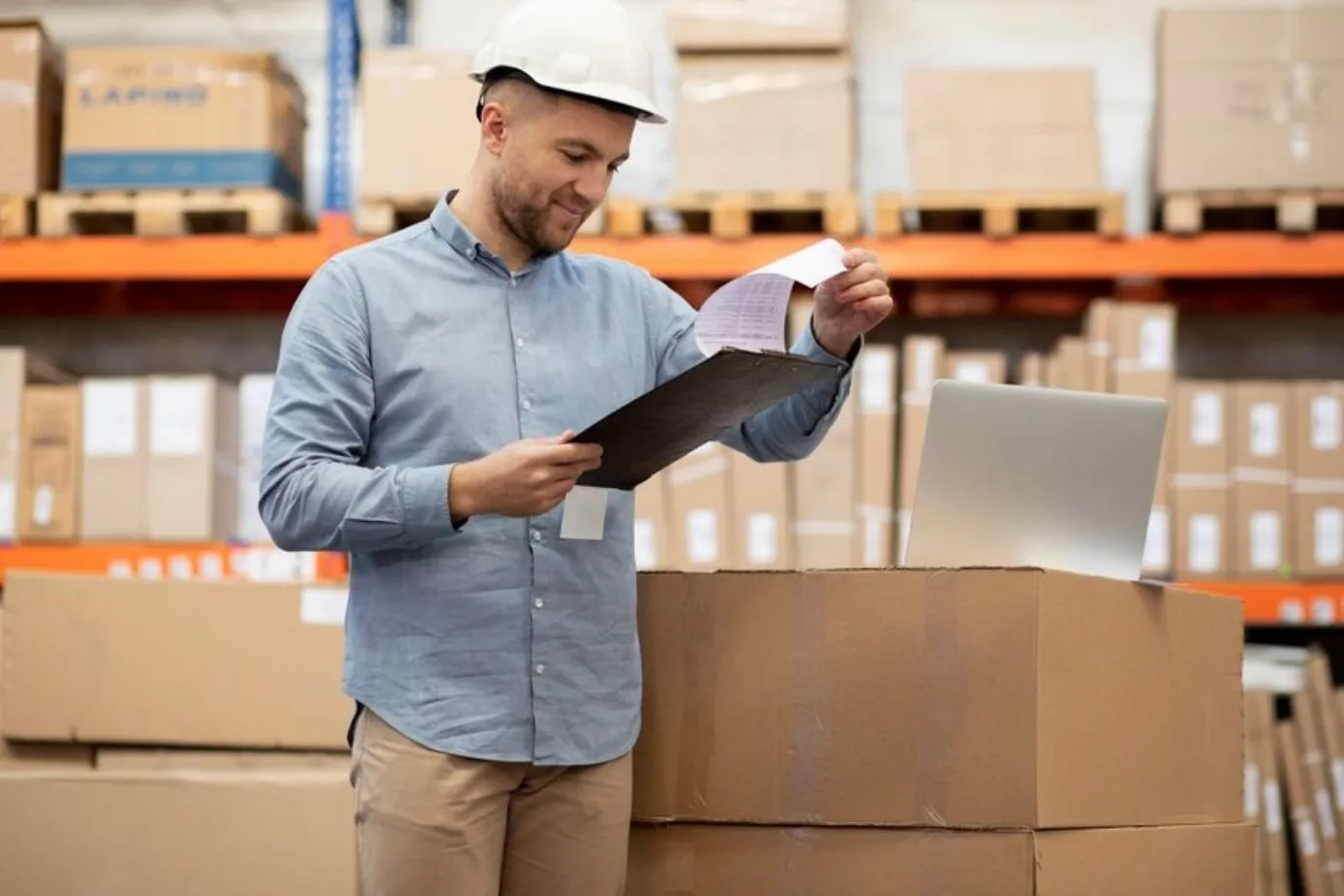
Manufacturers face continuous pressure to deliver the best quality products. It is why it becomes even more necessary for them to ensure the product quality before it leaves the warehouse. This is where the role of pre-delivery inspection comes in.
A pre-delivery inspection works as an assurance check that ensures the product works perfectly, is in good condition, and meets the set safety and quality standards. Even a single fault or error in the equipment can result in costly repairs, machine breakdown, or safety threats for the user. These inspections are even more crucial in industries such as automotive, heavy machinery, aerospace, and aftermarket services, where safety is paramount.
Also, customers always expect nothing less than the best value for their money. Faults in the machine or a complete breakdown frustrate customers and shake their loyalty towards the brand. To overcome these shortcomings, PDIs help manufacturers to spot and eliminate errors beforehand and deliver excellence every time.
Challenges Involved in Pre-Delivery Inspections
While manufacturers need to conduct pre-delivery inspections, things might get messy with traditional methods. Here is what manufacturers may find challenging when conducting PDIs:
- Frequent Errors: The traditional methods of executing PDI involve creating paper checklists that are prone to errors. At times, team members might be in a rush, may skip a line, or scribble something unreadable. All such instances create a problem that could have been caught and avoided.
- Time-Consuming Paperwork: Making manual entries in forms, chasing approvals, and stuffing reports into cabinets wastes a lot of time. Lengthy paperwork is a replaceable process that unnecessarily engages your teams and reduces their efficiency.
- Delays Pile Up: One missing signature or a re-inspection due to a single error can hold up a delivery for days or maybe weeks. Customers always need their product on time, but might not be concerned about how you deliver it.
- Safety Hazards: Even the smallest product defects can sometimes result in more than just a warranty claim. It may cause serious safety threats to the user, putting them in danger.
These problems are more than obstacles. They increase operational costs, reduce the team’s efficiency, and compromise user safety.
The Need for Digital Transformation in Pre-Delivery Inspections
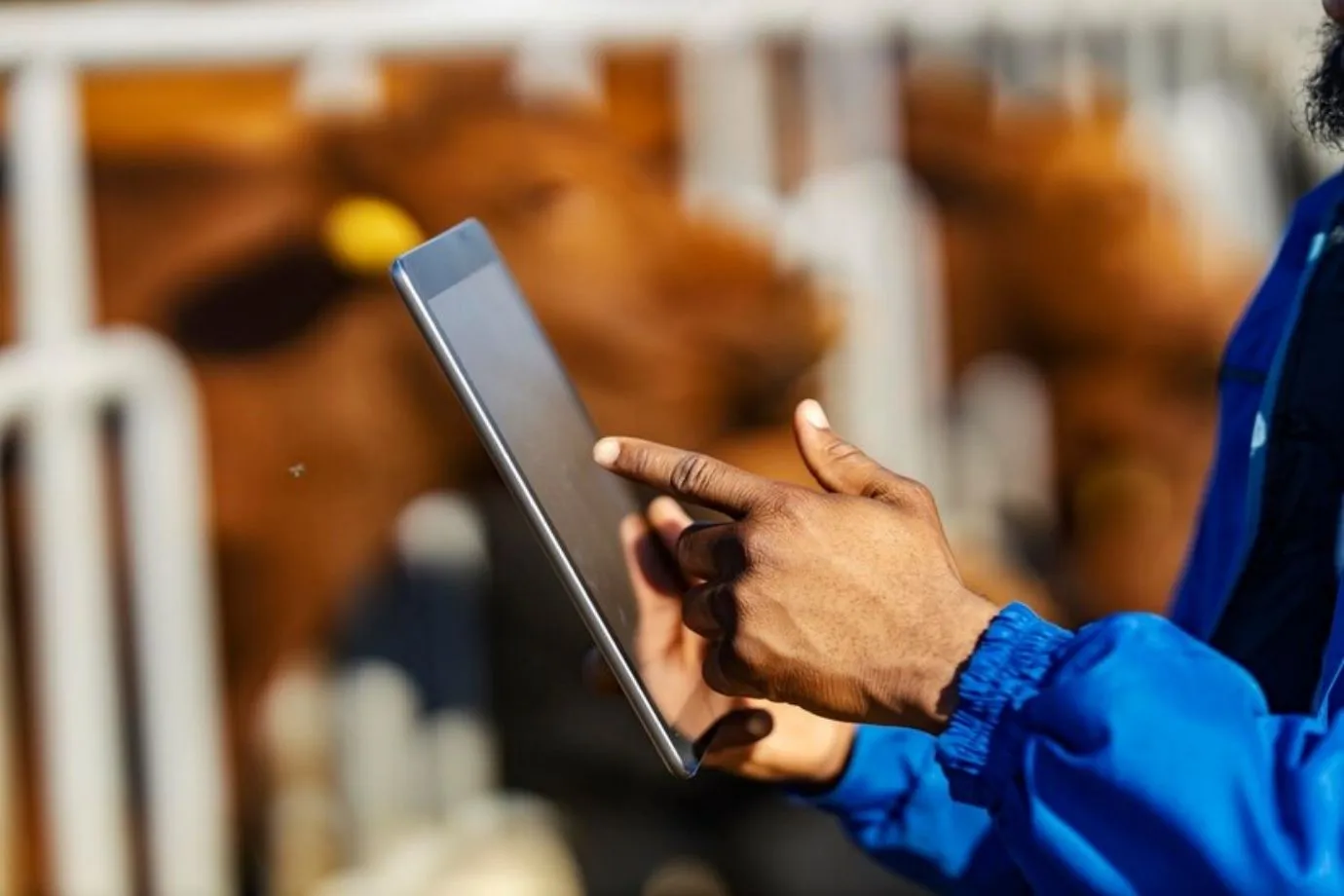
Limitations of Manual PDI Systems
The manual PDI systems are stuck in errors and inefficiencies. Manual processing in inspections, instead of focusing on quality, ends up with teams staring at stacks of paper checklists and drowning in paperwork. Here’s why manual PDI systems are a big no in today’s digital world:
- They’re Slow: Writing everything by hand, compiling them as reports, and passing them around takes a lot of time and results in delivery delays.
- Limited Visibility: Paper records provide limited information, preventing teams from looking into the bigger picture. This leads to overlooking recurring errors that might pose safety issues or emerge as a product defect later.
- Lead to Inconsistency: Teams working at different locations work differently. It leads to variability emerging among teams and might compromise product quality.
- Storage Issues: Paper-based files take up more space and are easy to misplace. It's also difficult to search for the required file during an audit or customer query.
Why is Digitalization of the PDI Process Necessary?
Digitalization of inspections is a game-changer for manufacturers. It helps them fasten their processes while saving time and effort. Here’s how the digitalization of pre-delivery inspections makes a difference for manufacturers:
- Faster and Reliable: When checklists are digitized, there is no room for human error. Your teams follow a clear set of predefined instructions so nothing slips out of the guidelines. It also saves time as team members have clarity on what to do and how to do it.
- Real-Time Updates: Digital platforms enable the instant flow of data. This eliminates the need to manually escalate information from one source/team to another, reducing waiting time and accelerating decision-making.
- Consistency Among Teams: Despite where teams are working from, digital tools ensure that everyone follows the same process.
- Secure records: Every digital inspection gets recorded with photos, notes, and videos. This provides a sturdy trail for audits and prevents future disputes.
- Data Insights: Digital platforms analyze data and spot patterns that exist, such as which parts fail the most. It comes in handy for manufacturers to fix shortcomings before they escalate further.
- Easy Integration: Digital PDI software keeps everything in sync by integrating easily with other existing systems such as CRM, DMS, and ERP systems.
- Centralized Access: When manufacturers use cloud-based systems, it provide centralized access to their teams. This enables them to make inspections from any location through their phone.
- Cost Savings: Manufacturers can save on costs and maximize profits when errors and reworks are minimal and no paperwork is involved
These features indicate that pre-delivery software is no longer a luxury but a necessity. For manufacturers looking to stay ahead of their competitors, it is essential to have a digital inspection process.
Intelli PDI as a Digital Pre-Delivery Inspection Software
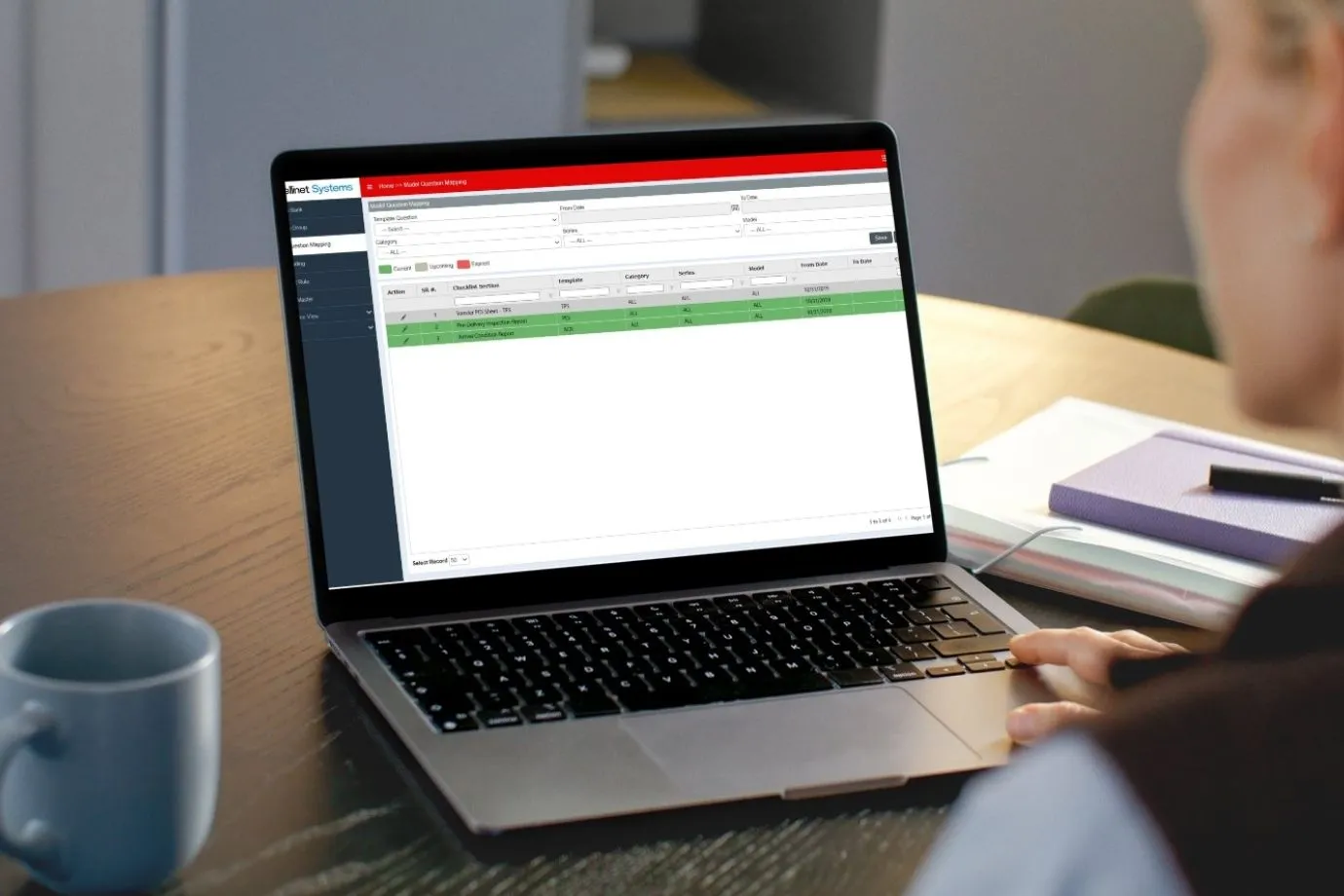
To mitigate the challenges of traditional PDIs, we at Intellinet Systems developed Intelli PDI. This is a digital inspection platform that helps manufacturers inspect products before or after their scheduled delivery. Intelli PDI is a mobile-based software and can also be used to conduct internal plant inspections.
Features of Intelli PDI
Here’s what Intelli PDI does to your pre-delivery inspections:
- Creates Customized Checklists Effortlessly: Intelli PDI allows for checklists creation whenever required. Our user-friendly interface enables users to customize the checklist for each model with ease.
- Visual Documentation: During inspections, inspectors can also capture images or video through the app directly using their mobile. This visualization helps in supporting the findings, enhances the document's value, and simplifies issue resolution.
- Mobile-Based Inspections: Field teams can easily access Intelli PDI on their mobile using our native Android app. This allows them to conduct inspections from anywhere, anytime.
- Real-time visibility: With instant access to inspection data, manufacturers can make decisions swiftly and stay updated on on-field inspections.
How Does Intelli PDI Address Pain Points of Pre-Delivery Inspection?
Intelli PDI solves the challenges manufacturers faced with manual PDIs:
- Eliminates Errors: Digital checklists ensure teams make inspections and checks smartly and keep errors at bay.
- Improves Efficiency: With organized checklists for each inspection, teams can access the required documents and share them as needed.
- Boosts Product Safety: Manufacturers can identify product errors and defects early through robust checks and inspections, helping them keep safety-related risks away.
Business Benefits of Intelli PDI
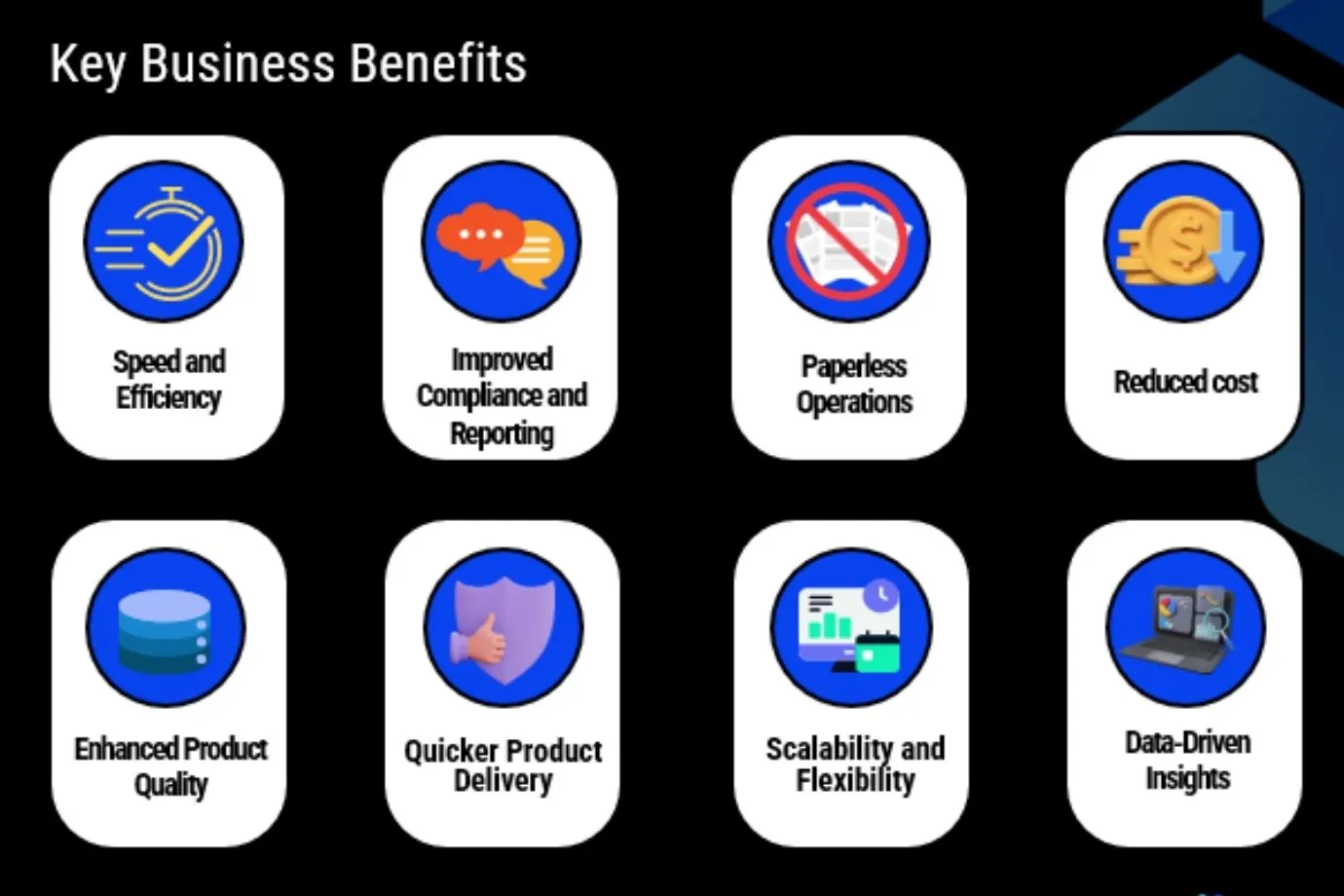
Intelli PDI turns the once inefficient pre-delivery inspection process into a potent, effective opportunity for manufacturers.
- Time-Saving: Automation of inspection processes and real-time data reduces the burden on inspectors. This automation increases their efficiency and allows them to focus on more crucial tasks.
- Cost-Saving: No paperwork means no more documentation or storage expenses involved, and savings on costs.
- Improved Product Quality: With centralized access to standard quality guidelines, it's easier to ensure product quality everywhere and sustain it.
- Quick Delivery: With quick inspections, manufacturers can finish deliveries quickly.
- Data-Driven Insights: With real-time data, manufacturers can see if things are working. This helps them spot product defects earlier and make modifications as needed.
Practices for Implementing Intelli PDI
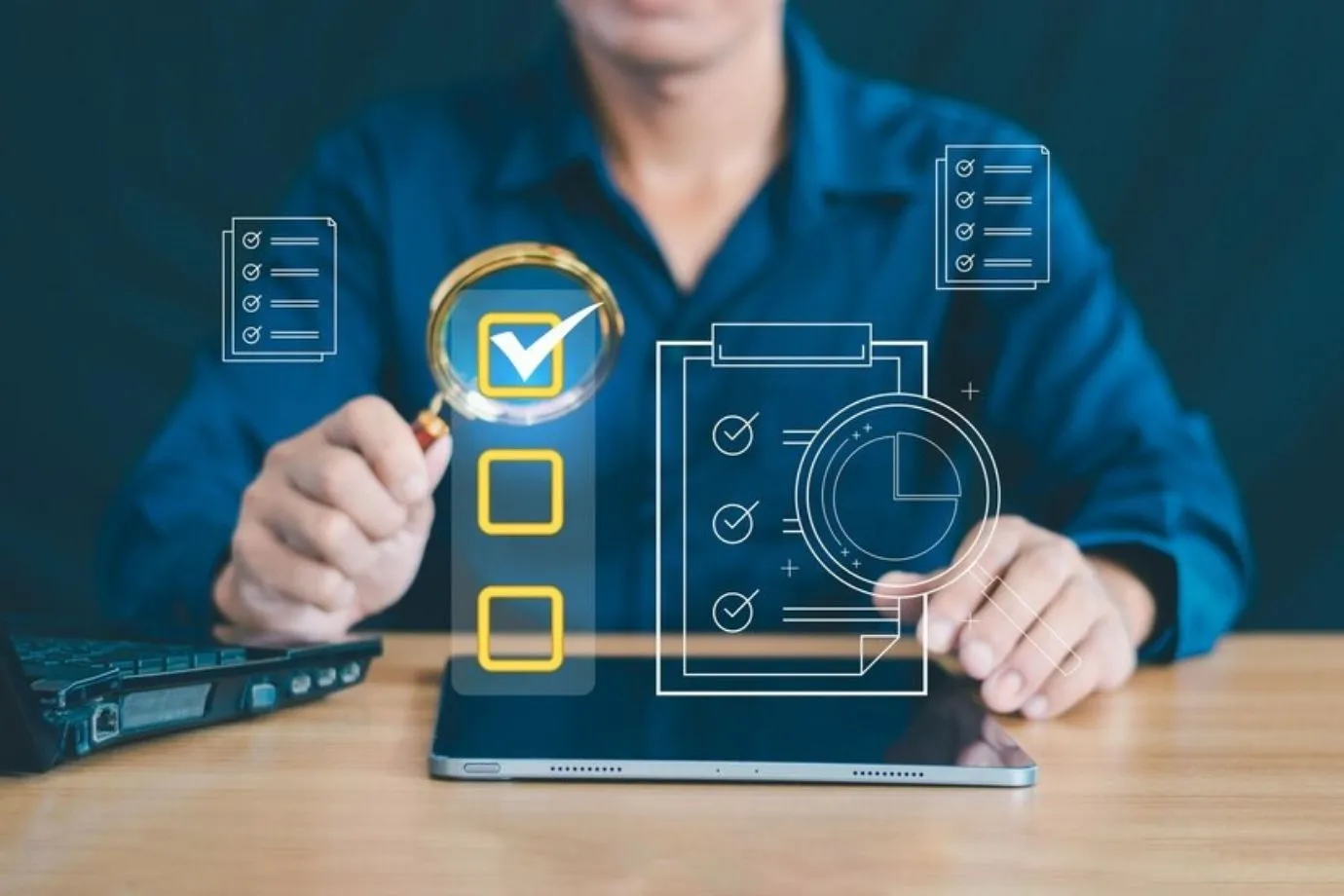
Manufacturers should adopt these practices when implementing Intelli PDI:
- Keep Checklists Precise: Try to keep the checklists sorted and as minimal as possible. Avoid adding unnecessary stuff and overloading with extra steps that slow the inspection process.
- Provide Training: Teams work efficiently when they know how to use the software the right way.
- Promote Visual-Based Inspections: Ask your teams to add visual evidence like photos and videos. This will enhance transparency in inspections and help spot errors and faults easily.
- Analyze Inspection data Regularly: Checking the analytics data regularly enables manufacturers to spot trends in defects or errors early. It helps you set goals like reducing defect rates and speeding up inspections.
- Integrate Well: Integrate Intelli PDI with your existing business systems, like CRM and ERP. It will ensure data flows smoothly without the need for any manual processing.
- Start Small: When making changes or trying new things, make trials in a specific team or department. It will save you in case things don’t go well and prevent huge losses.
- Collect Active Feedback: Ask your teams for genuine feedback. It will help you understand the achievements and spot areas of improvement.
Takeaways
Manufacturers conduct Pre-delivery inspections to identify errors and defects in products before they are delivered. The traditional methods involved manual work and a high risk of errors. This often caused delays in approvals during inspections and product delivery. A digital Pre-Delivery Inspection (PDI) software solved these difficulties. This software digitizes documentation of inspection reports to prevent errors from creeping into the inspections and improves efficiency.
PDI software like Intelli PDI provides a dynamic checklist to ease this process. Users can access this platform on their mobile anytime from any location. Field teams can use this accessibility to add relevant images and videos and support their findings. With accurate and reliable PDIs, manufacturers can cut unnecessary costs, minimize delivery time, and improve product quality. Beyond just being a software, Intelli PDI helps manufacturers inspect smarter, deliver products better, and stay ahead in the competitive market.
Wish to know how Intelli PDI can transform delivery inspections for your business? Get a free demo today.
Explore More Insights
About the Author
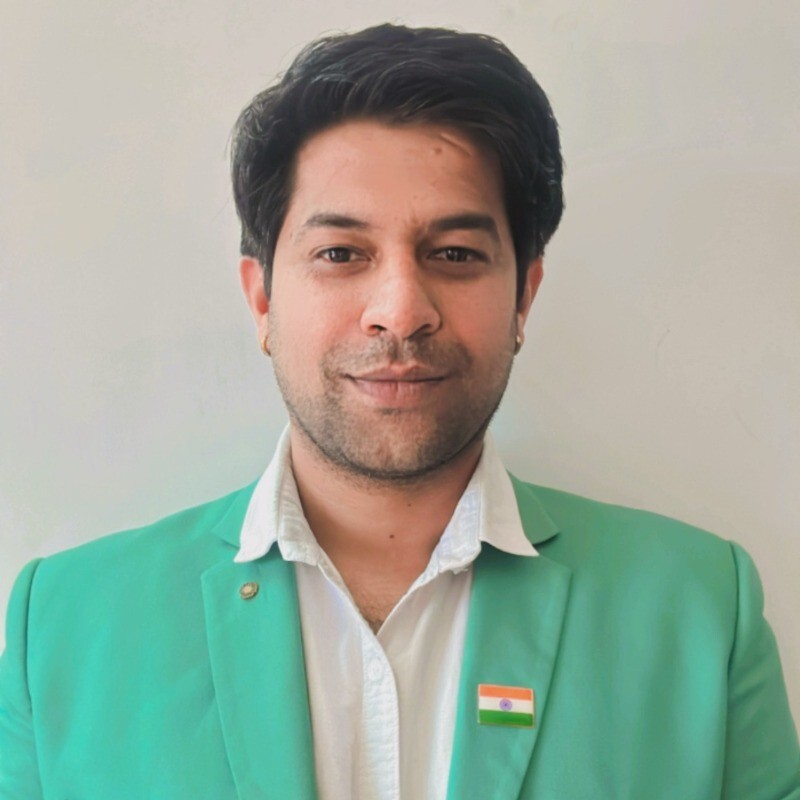
Chandra Shekhar
Chandra Shekhar is the Senior Manager, Strategy & Business Development at Intellinet Systems. With over a decade of experience in the automotive industry, Chandra Shekhar has led digital transformation and aftersales strategy initiatives for OEMs across multiple markets. His background combines deep industry knowledge with a practical understanding of how technology can solve real operational challenges. He focuses on making complex ideas clear and relevant for automotive and aftermarket professionals navigating ongoing change.