In the fast-paced, competitive manufacturing landscape, spare parts management is a crucial procedure for maintaining smooth operations. However, the OEMs widely outsource spare parts to suppliers which adds to the burden of timely recovering the cost from the supplier.
This problem demands an efficient supplier recovery process to ensure profitability and operational efficiency. A streamlined supplier recovery process facilitates OEMs to recover defective part costs from suppliers and build healthier supplier relationships.
This blog will explore how to build a strong supplier recovery process and highlight how digital solutions, like warranty claim management systems, can transform it.
Understanding Supplier Recovery & Its Importance

Supplier recovery is the process through which OEMs recover costs incurred due to defective parts from their suppliers. It ensures supplier accountability, reduces financial losses, and promotes transparency and collaboration, strengthening partnerships with suppliers.
A well-executed supplier recovery process is crucial for:
- Cost Recovery: Enabling OEMs to recover costs resulting from defective parts or products manufactured by the supplier.
- Two-Way Communication: Facilitating two-way communication channels between OEMs and suppliers.
- Supplier Accountability: Holding the suppliers accountable to produce higher quality parts, helping in reducing future warranty claims.
- Cost Control: Recovering warranty costs helps OEMs manage their overall costs, and allocate financial resources better.
- Relationship Management: Maintaining trust and encouraging long-term relationships with suppliers.
- Customer Satisfaction: Quick warranty claim resolution enhances customer experience and helps in building brand value.
This creates the need for automated supplier recovery systems to ensure the supply recovery process stays error-free and efficient, reducing the resolution time and resources.
Implementing a Strong Supplier Recovery Process
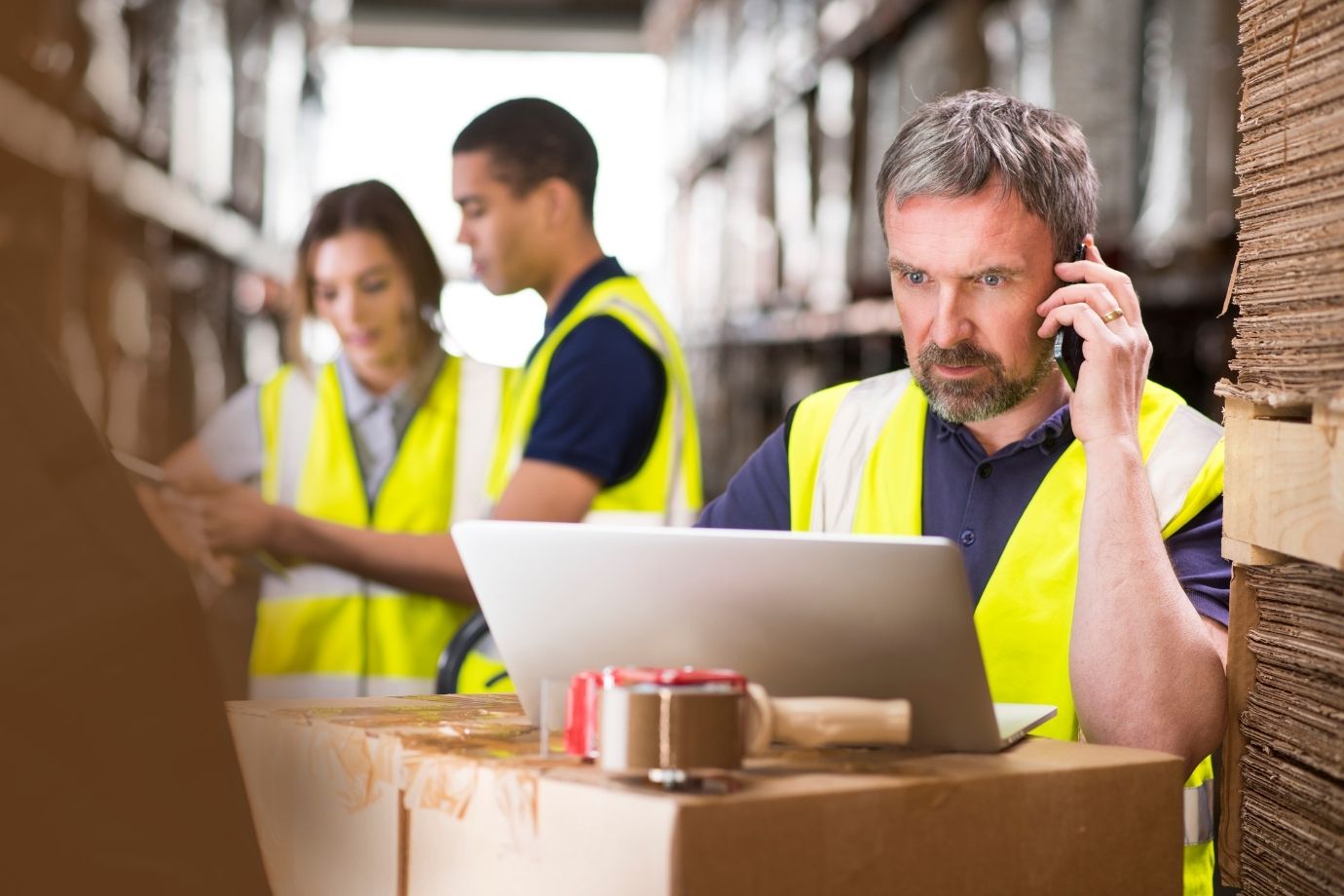
Creating an efficient and reliable supplier recovery process requires a strategic approach. Practices like implementing the latest technologies and tools, supplier collaborations, and data-driven decision-making can help OEMs overcome common challenges.
To build an effective supplier recovery process, consider the following practices:
1. Invest in Advanced Warranty Management Software
Modern warranty management software solutions like Intelli Warranty provide comprehensive solutions for tracking, processing, and analyzing warranty claims. Digital solutions eliminate the need for manual tracking and offer centralized platforms for managing claims. By unifying OEMs, dealers, and suppliers on a single platform, it also enhances visibility and control, ensuring consistent performance.
2. Cultivate Collaborative Supplier Relationships
Promoting open communications with suppliers will actively involve them in the recovery process. This collaboration will ensure smoother negotiations and faster resolutions.
3. Utilize Warranty Analytics
Analyzing data through warranty analytics will help OEMs identify recurring issues, enhance supplier contracts, and improve upcoming recovery outcomes.
4. Train Your Team
Equip your team with the knowledge and skills required to handle automated tools effectively. Training ensures seamless integration of technology into existing processes.
Automation in Supplier Recovery
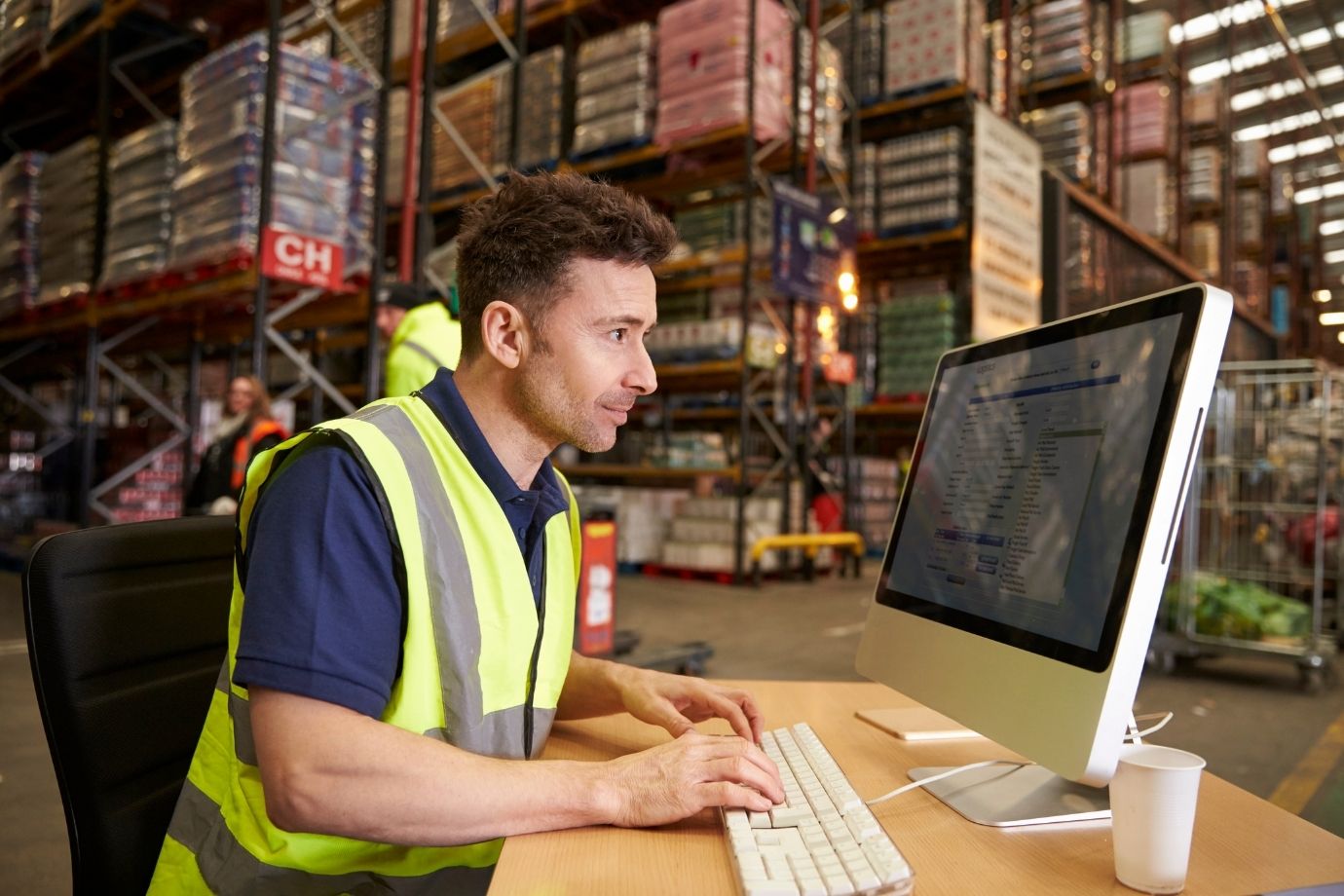
Automation has upgraded the supplier recovery process by enhancing downtime, accuracy, and overall scalability. Innovative tools like Intelli Warranty facilitate end-to-end solutions for efficiently managing warranty claims and supplier cost recovery.
Below is a list of benefits of automating the supplier recovery process:
- Quicker Claim Processing: Automating the recovery process minimizes manual actions, significantly reducing processing time for warranty claims.
- Improved Accuracy: By predefining workflows and validation authentications, modern tools significantly reduce errors in the process and boost accuracy.
- Cost Savings: Reducing errors minimizes inefficiencies and downtime, saving costs in the long run.
- Stronger Relationships with Suppliers: Automated process enhances transparency, builds trust, and improves supplier partnerships.
Intelli Warranty for an Efficient Supply Recovery Process
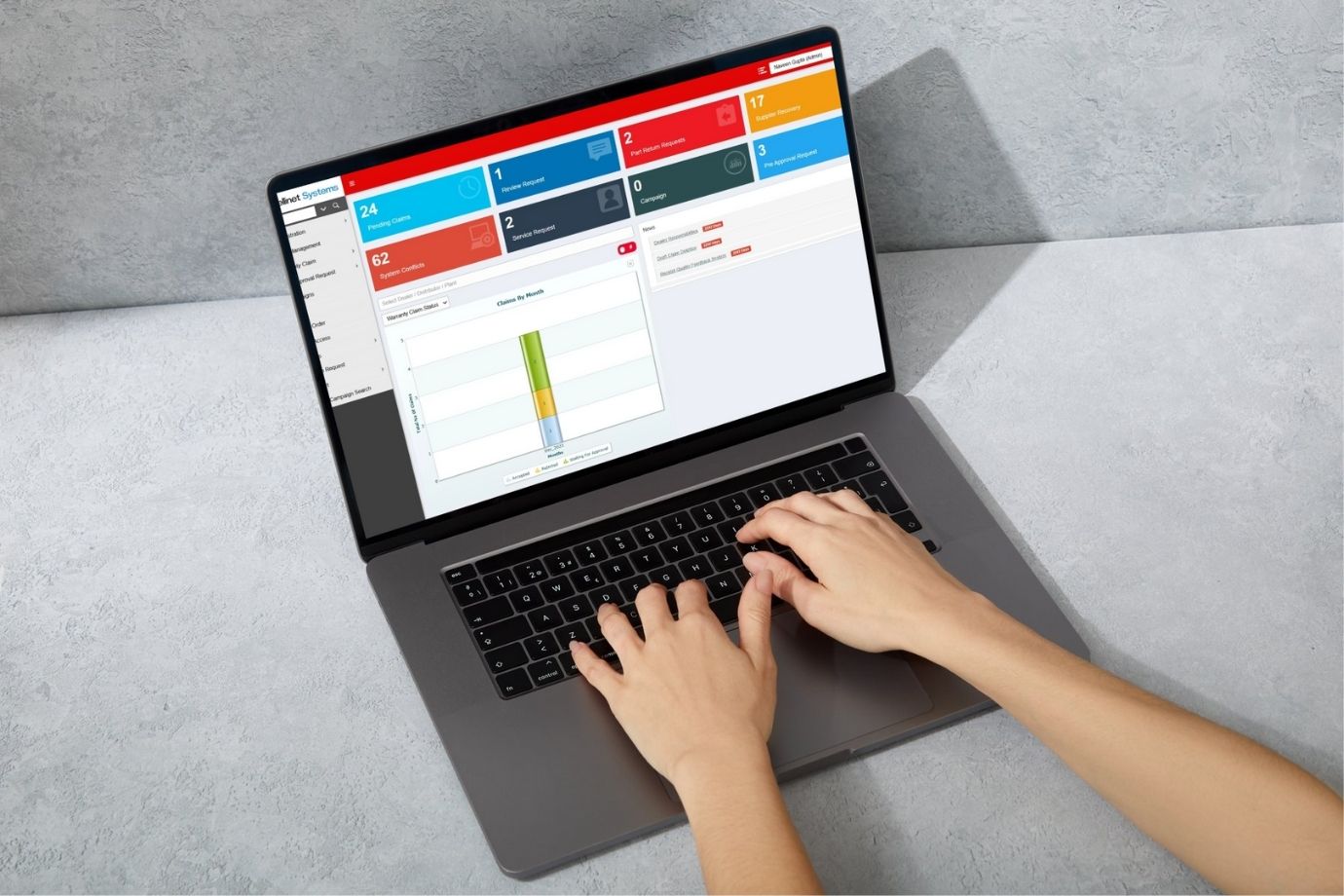
Intelli Warranty is an advanced warranty management software developed to organize and improve the supplier recovery process. Our solution integrates automation, real-time insights, and innovative features with user-friendly navigation.
Every time a dealer raises a warranty claim on the portal, the OEM reviews it for authentication. Once the claim gets approved by the OEM, Intelli Warranty automatically notifies the concerned supplier. The supplier can either process a reimbursement or replace the defective spare part. By minimizing manual intervention, our warranty management solution helps streamline and speed up this claim process.
Here’s how Intelli Warranty proves as a game-changer for OEMs, helping them achieve operational excellence in supplier recovery:
- Ease of Use: Intelli Warranty’s user-friendly interface ensures quick adoption by teams, reducing training time and costs.
- Scalability: Whether you’re a small business or a large enterprise, Intelli Warranty adapts to your needs, scaling parallel to your operations.
- Expert Support: Our software offers dedicated support to OEMs and suppliers to ensure seamless implementation and ongoing success.
- Proactive Compliance: Stay ahead of regulatory requirements with automated documentation and tracking, ensuring compliance without added effort.
By implementing Intelli Warranty, OEMs can transform their supplier recovery process. A streamlined, automated, and highly efficient recovery process.
Key Takeaways
An effective supplier recovery process is crucial to maintain operational efficiency and foster long-lasting supplier relationships. Implementing a smooth recovery process enables OEMs to reclaim the cost of defective parts and products from the suppliers, reducing revenue leakage significantly.
By implementing the right strategies and digital solutions, OEMs can optimize their supplier recovery process. Additionally, automating supplier recovery by introducing advanced tools like Intelli Warranty can prove as a game-changer. These tools help OEMs optimize their supply recovery process, further overcoming traditional challenges and making significant cost savings.
To learn how Intelli Warranty can streamline your supplier recovery process or request a free demo, contact us today.
Explore More Insights
About the Author
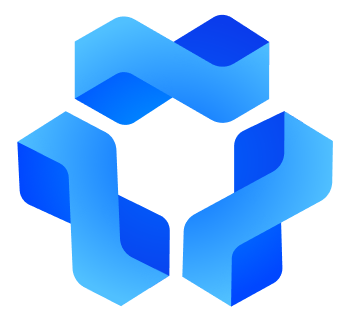