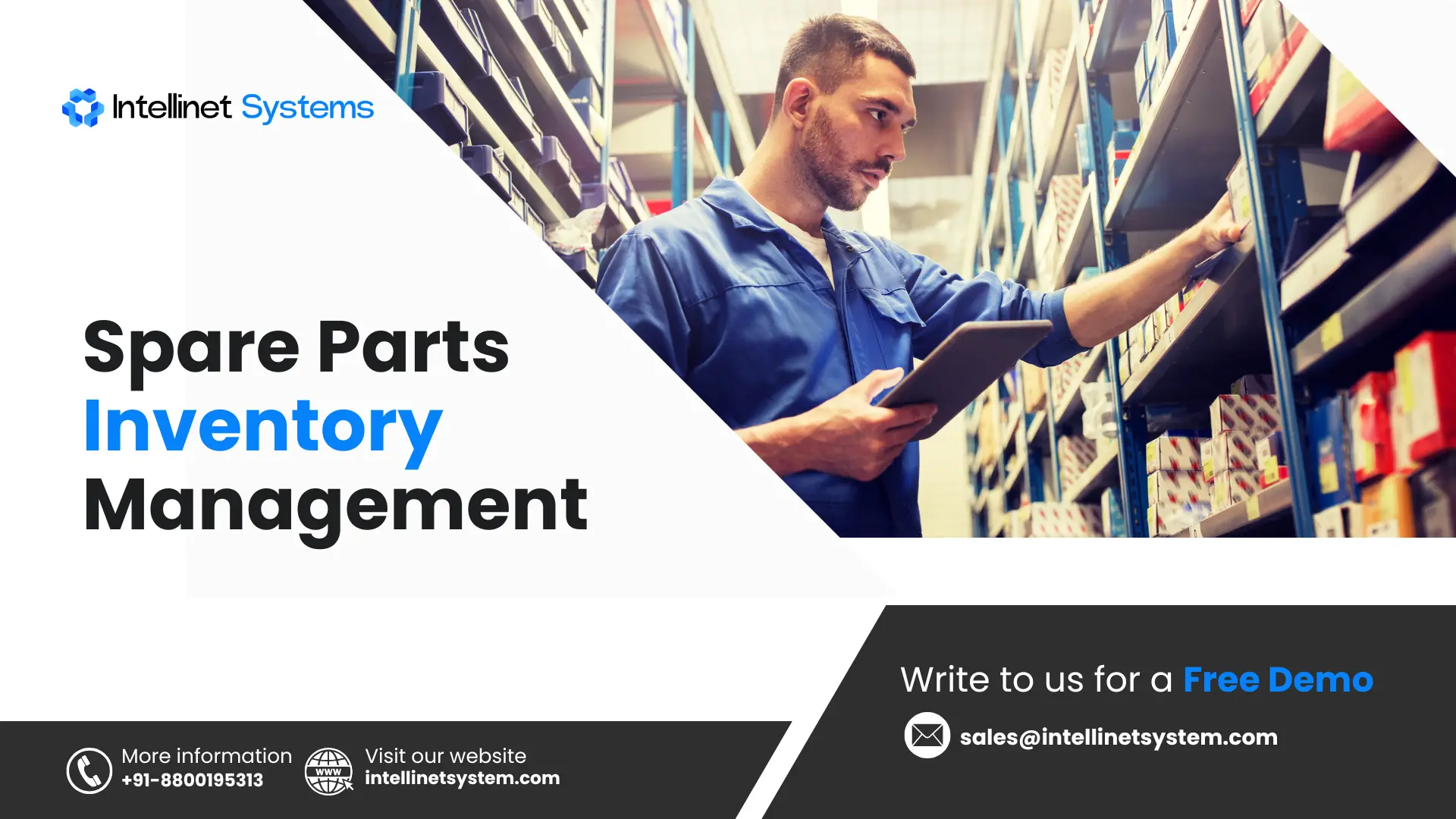
Spare parts inventory management is crucial in every operation, whether it is a busy production line, a service store, or a large warehouse with thousands of parts. When supported by the right inventory management software, everything runs smoother: machines stay up, unexpected breakdowns decrease, and assets last longer. But get it wrong, and you end up burning cash on parts you don’t need, cramming valuable storage with junk, and dealing with delays that frustrate your team and your customers alike.
In the current times, businesses simply cannot afford to take chances or use outdated spreadsheets that become obsolete in a day. In essence, intelligent spare parts management comes down to clear procedures, well-trained personnel, and the right tools to track, store, and replenish parts efficiently, without headaches or financial losses. By doing so, you will have your parts in order, make the life of your maintenance staff easier, and keep things running smoothly, regardless of how complex your equipment is or how busy your production becomes.
Key Strategies
Smart management of spare parts inventory does not occur unintentionally. It is based on set goals, trained workers, and consistent systems. Companies that take time to improve their spare parts management tend to have fewer sudden breakdowns. Besides, it decreases the cost of maintenance and instills confidence in the maintenance plan. Here are 13 proven strategies to give you better command, cut the losses, and keep the operations flowing sans costly breaks.
1. Spare Part Prioritization
Not every spare part deserves equal attention or investment. Begin by categorizing your inventory of parts by how critical they are to production and safety. For example, parts that could stop an entire production line should always be stocked at minimum levels. Apply ABC analysis or risk ranking to identify these crucial items. Prioritization helps focus your budget where it counts and keeps your parts inventory tracking clear and simple.
2. Create A Comprehensive Lead Time Resource
Unexpected supplier delays can throw off your entire maintenance schedule. Build and regularly update a lead time chart for every spare part you keep in stock. This resource helps your purchasing team know when to reorder and how much buffer time to allow for shipping. A clear lead time database turns your maintenance and spare parts management from guesswork into a well-oiled routine and reduces emergency shipping costs.
3. Leverage Data
Stocking too many parts ties up your money; not having enough can shut things down when you least expect it. Look at past usage, seasonal trends, and how often things break to make smart calls. A good spare parts inventory software can help you balance it all without the guesswork. A robust spare parts inventory software can automate this data and make forecasts that will work. Backed by facts, you avoid hoarding unnecessary spares while ensuring mission-critical parts are always on hand. Better insights also make parts room organization more efficient.
4. Factor in New Machinery Parts
When adding new equipment to your operations, it’s easy to forget about the spare parts it requires, until you urgently need them. Add all new parts to your inventory and procurement system as soon as the machine arrives. This proactive step keeps your spare parts management process flow updated, prevents last-minute purchases, and helps your maintenance team stay ready for planned or unexpected repairs.
5. Implement Security Measures
Small parts cumulatively lead to substantial losses in the long run if mislaid; use padlocks, watchful eyes in the form of cameras, and proper sign-out procedures for controlling access to high-value spares. In such a big warehouse, proper accountability will not only prevent mismanagement but will also reduce pilfering. Complement the above measures with the maintenance of an effective spare parts management system that records each transaction regarding the movement to and from storage; hence, the location of each part is always known.
6. Optimize Bill of Materials (BOM)
An accurate Bill of Materials (BOM) is your maintenance team’s best friend. List every spare part associated with each piece of equipment, including preferred suppliers and alternative options. This ensures you can store spare parts correctly and reorder replacements without delays. A precise BOM supports your overall maintenance spares management by minimizing errors and saving precious time during emergencies.
7. Create a Standard Process
When everyone does things their way, mistakes pile up fast. Take the guesswork laying down clear step-by-step instructions for ordering, checking, storing, and handing out parts. Then make sure your whole crew sticks to it every single time. A good spare parts management process helps keep everything running smoothly and keeps mistakes to a minimum. The standard spare parts inventory software system shall be updated and shall not allow anything to be overlooked, whoever may be on shift, however, busy the warehouse is.
8. Make Spare Parts Accessible
A messy storeroom is a time-waster and a headache for everyone. Set up your space for easy spare parts management — think clear labels, color-coded bins, and wide, clutter-free aisles. Keep the parts you grab most often right up front so no one has to dig around or waste time hunting for them. A good organization will support smooth maintenance, spare parts management, downtime during repairs, and help new staff find what they need without guesswork.
9. Strategic Spare Parts Storage and Distribution
Consideration of how a layout will affect productivity. Store high-demand parts close to the work area to minimize walking time and place infrequently used items in a locked central storeroom. This smart distribution reduces technician delays and increases wrench time on the floor. It’s a major perk of investing in reliable parts inventory management software, whether it’s free or premium, good software supports this balance beautifully.
10. Maintenance Strategies and Work Order Management
An effective spare parts management for maintenance strategy ties parts availability directly to your maintenance plan. Associate your stock setup with job requests so that items are set aside beforehand for scheduled tasks. This matching stops final rushes and keeps the production schedules on track. A system makes it simple to order again when the stock goes below the set levels.
11. Reduce Unplanned Downtime
It’s way cheaper to stop a breakdown before it happens than to deal with one after. Use sensors and smart monitoring tools to spot wear and tear early. Back it up with solid automotive parts inventory management software so you’ve always got the right spare parts on hand when something needs fixing. A little prep means fewer surprises and a lot more uptime.
12. Enhancing Supplier Management
Your suppliers have a dramatic impact on your spare parts strategy. Build relationships with vendors that will help you achieve your objectives of supplying parts on time, at the right price, and supporting urgent orders when needed. Use a good spares management application to monitor their performance, get quotes, and manage contracts. Good relationships and clear expectations mean no surprises when you need critical parts in a hurry.
13. Training and Security Measures
The best system will not work if your staff are not properly trained. Invest in regular training sessions to ensure everyone understands how to use your spare inventory management system accurately. Reinforce security through regular audits and spot checks. A knowledgeable, responsible team keeps accurate records and handles every part with care— this protects your investment in modern inventory management software.
Conclusion
A well-organized spare parts system saves time, reduces costs, and helps prevent production delays. By following key strategies and using the right tools, you lay the groundwork for continuous improvement.
Whether you're managing spare parts for automotive or complex machinery, the right software strategy keeps your business moving forward.
Explore More Insights
About the Author
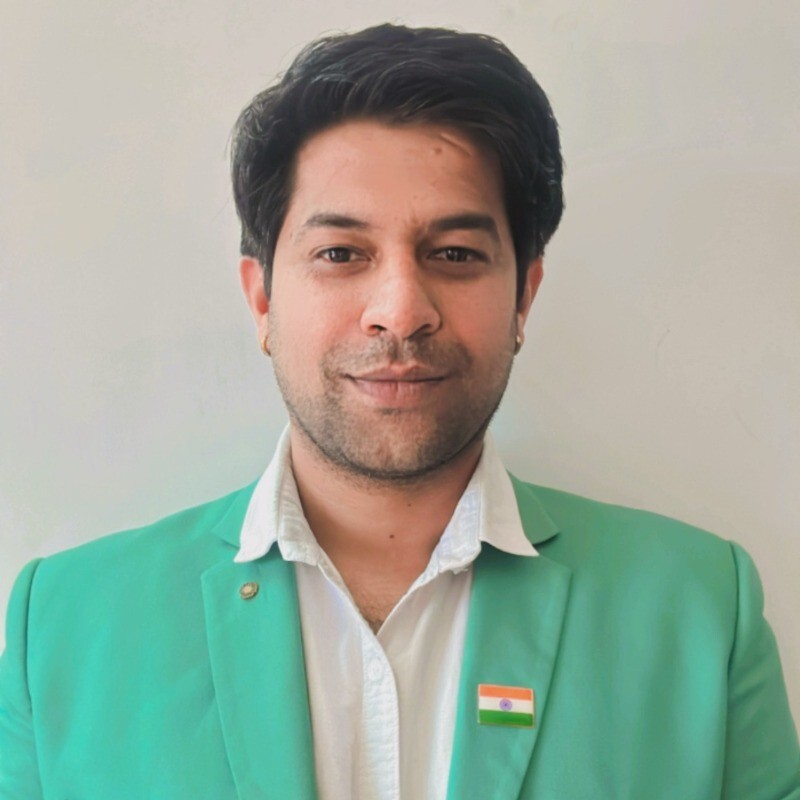
Chandra Shekhar
Chandra Shekhar is the Senior Manager, Strategy & Business Development at Intellinet Systems. With over a decade of experience in the automotive industry, Chandra Shekhar has led digital transformation and aftersales strategy initiatives for OEMs across multiple markets. His background combines deep industry knowledge with a practical understanding of how technology can solve real operational challenges. He focuses on making complex ideas clear and relevant for automotive and aftermarket professionals navigating ongoing change.