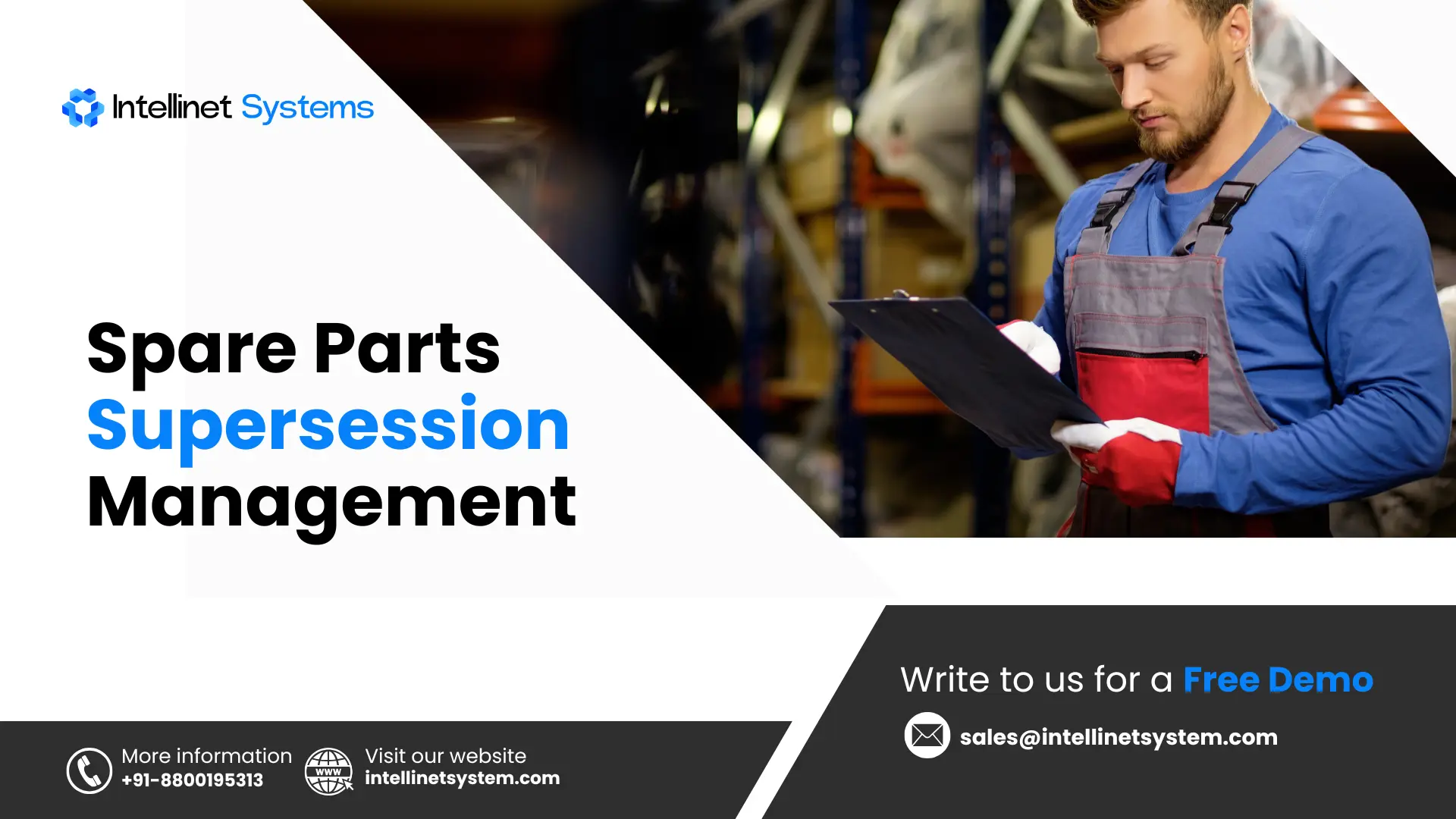
In instances when an old part is replaced by a new one but the parts catalog does not reflect the updated information within time, dealerships might still place orders for the old parts. This process of updating parts information, better known as parts supersession, brings in significant challenges for the Original Equipment Manufacturers (OEMs) as traditional parts catalogs demand frequent reprinting and distribution, which is a costly affair.
Poor parts supersession management can create havoc in industries like automotive, aerospace, and industrial equipment. When mishandled, parts supersession leads to misorders, inflating costs, delayed repairs, and dissatisfied customers who are not likely to come back. The hazards are high as parts misorders don’t just waste money, they also erode dealers’ trust and obstruct OEM’s operations.
Through this article, we will discuss how poor parts supersession management leads dealers to place wrong parts orders and how OEMs can overcome this issue to improve profitability and competitiveness in the aftermarket.
What is Parts Supersession?
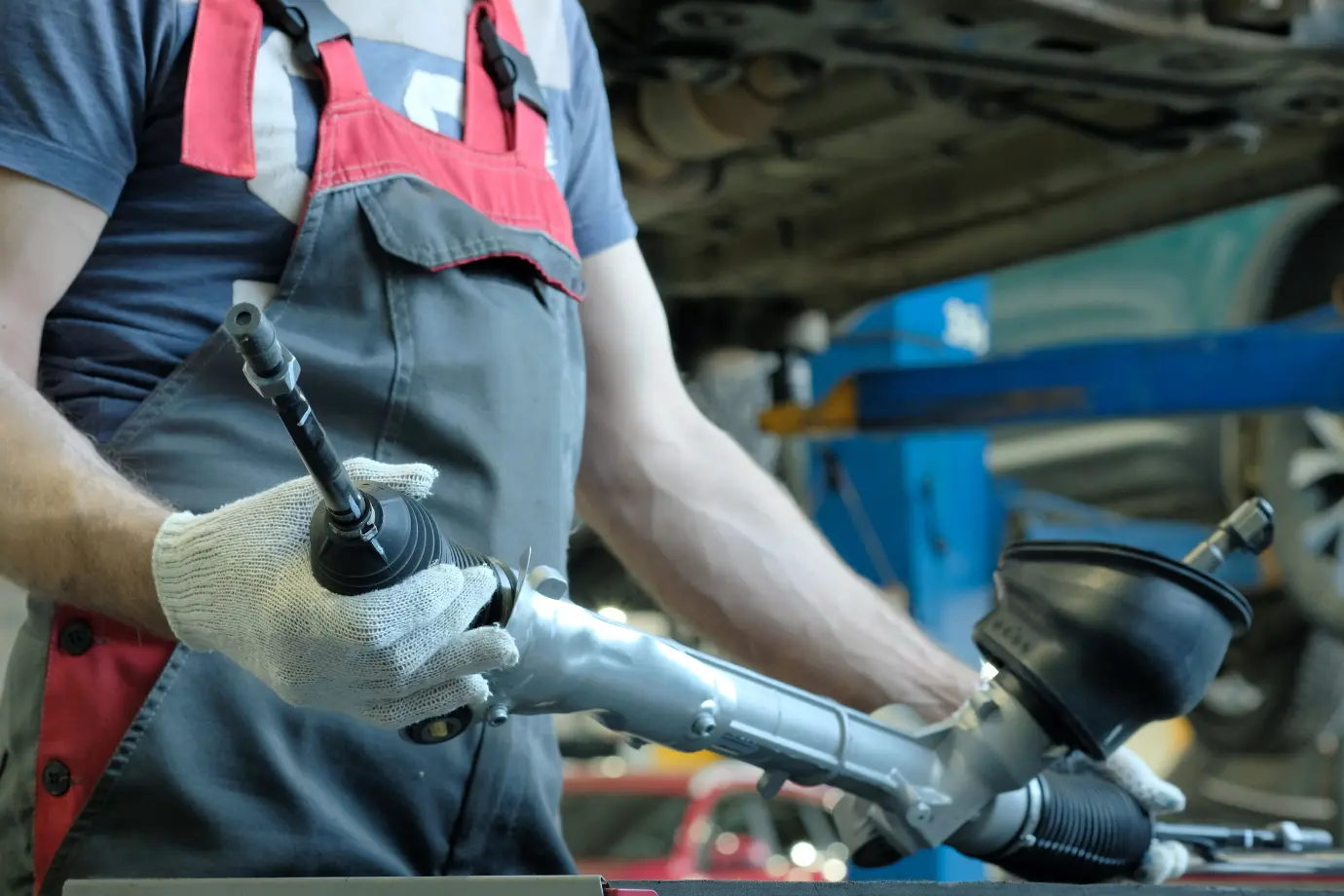
Parts supersession is the process by which an OEM replaces an older or obsolete spare part with a newer, updated version. The main reasons a spare part may be superseded include:
- Changes in Design: The part is redesigned to improve its performance or durability.
- Model Updates: Model upgrades in equipment require slight modifications or updates to the parts.
- Supplier Changes: Due to shifts in sourcing, OEMs may switch between suppliers, affecting parts specifications.
- Manufacturing Alterations: Changes in production materials, techniques, and compliance standards might lead to manufacturing shifts.
- Obsolescence or Discontinuation: When the original part is no longer produced and replaced by a compatible alternative.
- Cost Optimization: Introduction of a cost-effective but equivalent spare part.
For better understanding, let’s consider an example: an automotive OEM could replace a fuel injector with a new one that improves efficiency or complies with current emissions standards. Alternatively, a hydraulic connection may be upgraded by an aeronautical manufacturer to withstand higher pressures. These adjustments are common and frequently triggered by the need for compliance, cost reduction, or technological innovations.
But the problem is if dealers and technicians aren’t informed within time, they’ll order the same old parts. This will in turn result in receiving a spare part that’s either obsolete or incompatible. Not only does that part become useless, but it also causes delays in repair and leaves both customers and dealerships frustrated.
How Poor Parts Supersession Management Leads to Part Misorders?
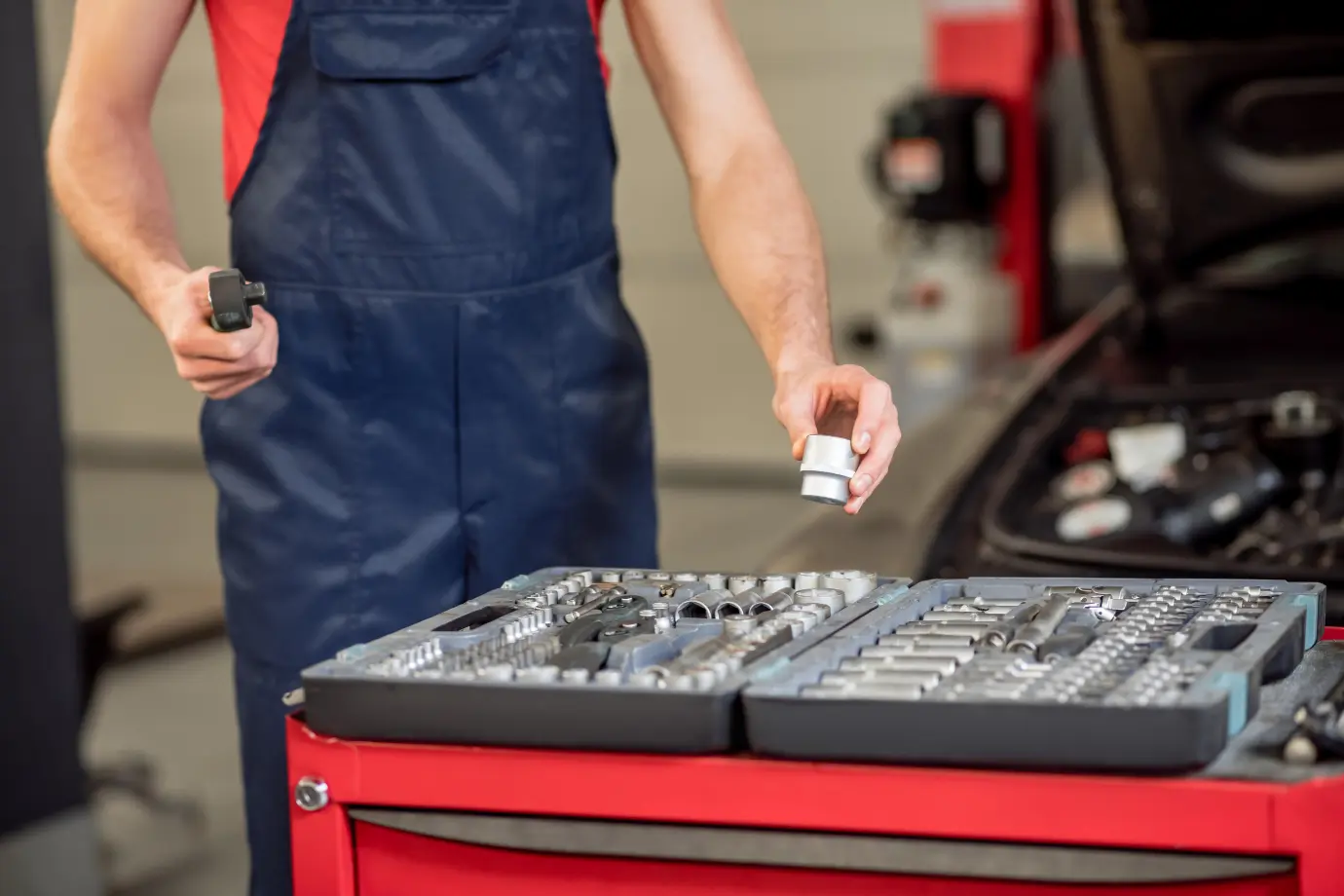
Let’s understand the impact of poor part supersession management on part orders through an example. Suppose a dealer orders a $3,000 transmission part for a combine harvester, only to discover it had been superseded weeks earlier. The catalog was outdated, the OEM hadn’t sent an update, and the customer (in this case, a farmer who was in the middle of harvest) waited a week for the right part.
In a nutshell, that’s what poor part supersession management is all about. Dealers are taking a risk with each part order when part information becomes out-of-date or when the OEM fails to update it on time.
Other Consequences of Poor Parts Supersession Management
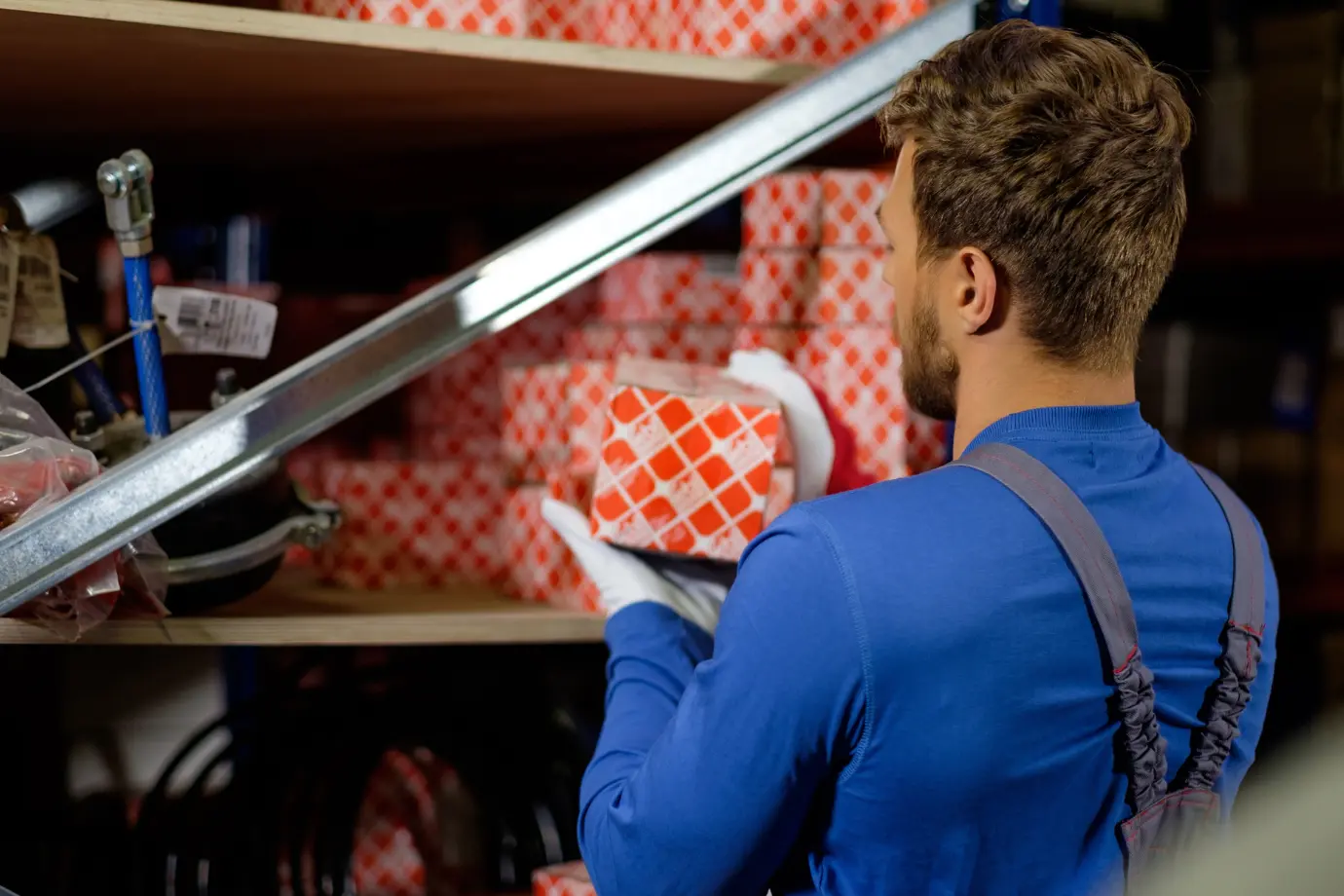
Part misorders are only the beginning and lead to further consequences across the supply chain. Customers, dealers, and OEMs are all impacted when parts supersession goes wrong. Let's discuss the damages caused by poor parts supersession management in more detail:
Financial Losses
Ordering the wrong part isn’t inexpensive. Beyond the cost of the part itself, there’s return shipping, restocking fees, and inventory sitting idle. Dealerships remain stuck with high capital on obsolete components due to pending or delayed supersession updates in the spare parts catalog. That’s money that they could use in hiring more staff but instead runs down the drain.
Increased Downtime
In industries like agriculture, time is everything. A farmer waiting on a tractor repair during planting season can lose thousands daily. In instances when a superseded hydraulic pump delays a repair for two weeks, it may cost the customer a significant share of their yield.
Inventory Mismanagement
Without clear supersession data, dealers overstock outdated parts or run dry on new ones. When there is no update on supersession, dealerships may stock warehouses with parts with no or low demand, tying up storage space and capital.
Customer Dissatisfaction
When parts don’t show up as promised, customers may lose trust in the OEM’s brand. Dealerships lose long-time customers over repeated supersession-related delays.
Why Do Traditional Methods of Parts Supersession Management Fail?
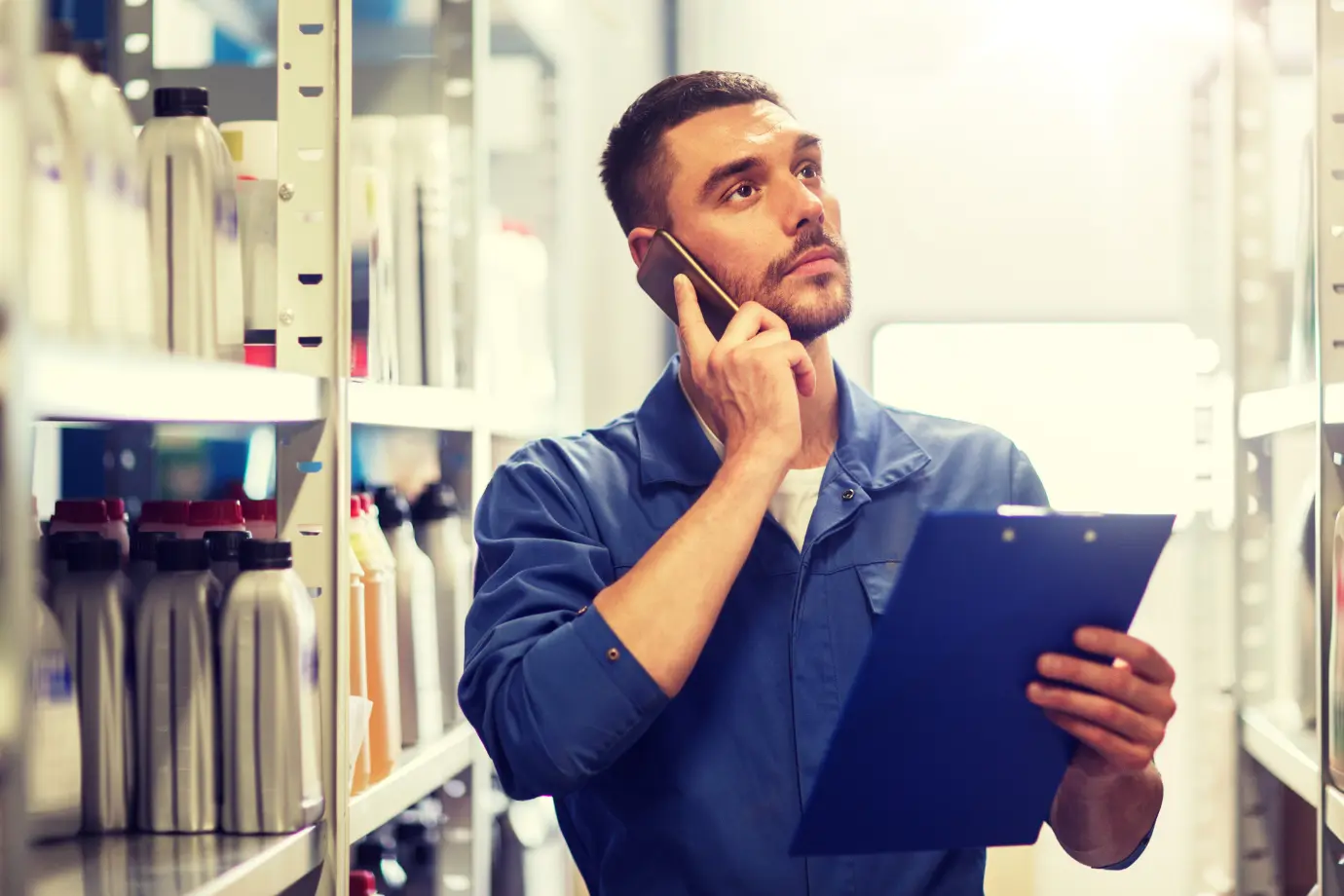
In the past, parts catalogs were bulky paper books, and identifying the right part was no less than a battle. Static PDFs, which offered an updated solution, could also not keep up with the pace as they were unable to meet the needs of modern parts supersession demands.
Here’s why these traditional methods are doomed to fail:
Growing Catalog Complexities
For paper-based systems, handling the modern complex inventories which involve thousands of parts that are updated every week, is no less than a nightmare. For the OEMs that managed innumerable SKUs, updating the catalog was ineffective in a matter of weeks.
Delayed Updates
It may take months to generate and then distribute the updated PDFs or paper catalogs. When dealers keep waiting this long for an updated catalog, the risk of new parts becoming obsolete still exists. This newly updated catalog might become outdated by the time dealers receive it.
Human Errors
Human error is unavoidable. Even a small mistake like a single error in part number can cause the dealership to place a wrong parts order. Manual systems are a minefield packed with potential blunders.
Communication Breakdowns
To communicate supersession changes, OEMs and dealers frequently use emails, which are frequently misplaced or ignored. Many times, the memo does not reach the dealer, leading them to place the wrong parts orders.
No Real-Time Access
Dealers want immediate results and not a catalog that is out of date before it is accessed. Traditional methods leave them guessing about supersession modifications and drain their trust in the OEM’s brand.
How Does Intelli Catalog Solve Challenges Involved in Parts Supersession Management?
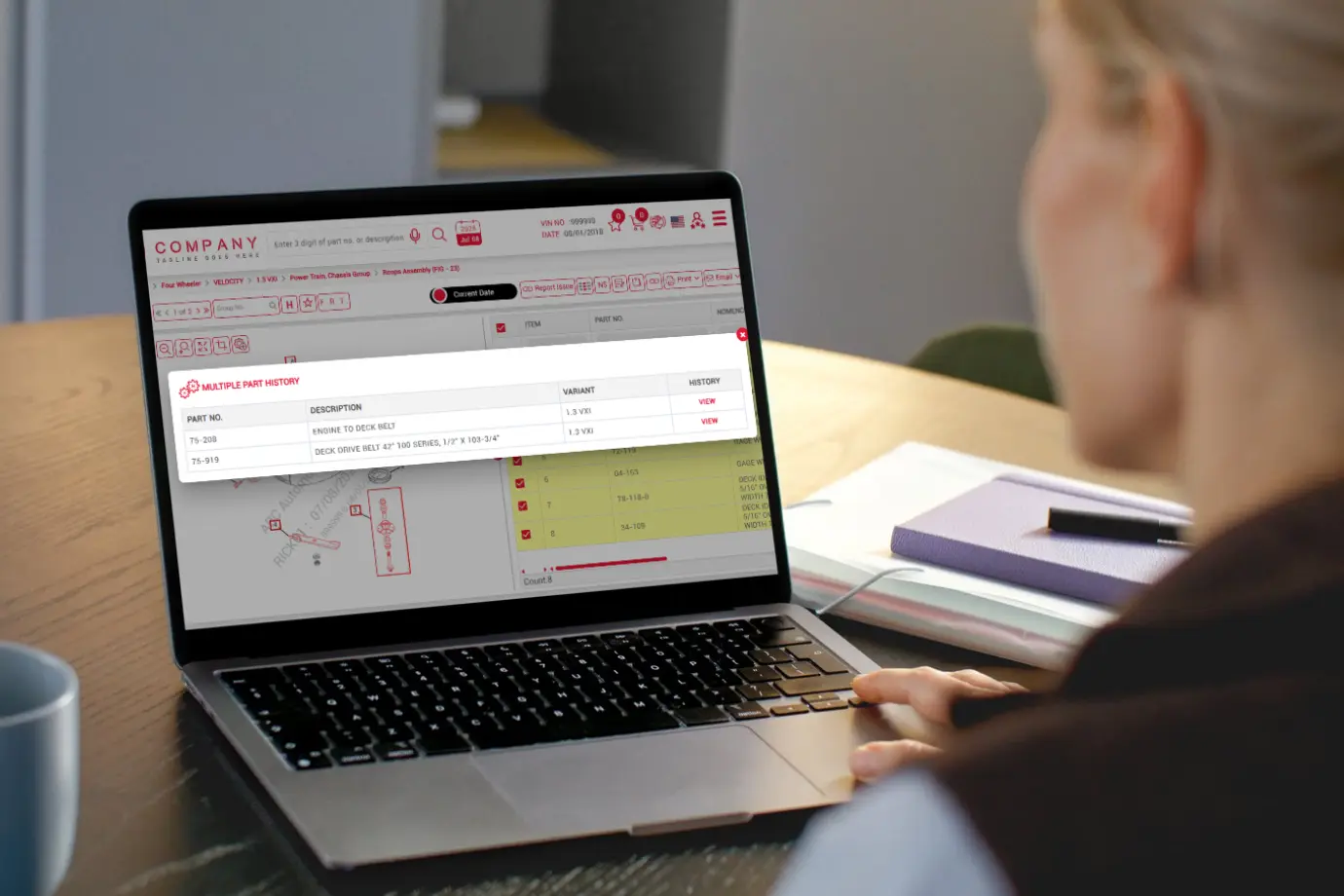
Intelli Catalog is an AI-powered electronic parts catalog software that provides OEMs with a digital, interactive edge to managing spare parts, offering a complete parts marketplace. Intelli Catalog follows a structured approach to managing frequent parts supersession, making things easier for OEMs and their stakeholders. With a centralized system, this illustrative parts catalog software simplifies the parts identification and ordering process for dealerships and avoids parts misorders.
Here is how Intelli Catalog solves the difficulties involved with parts supersession:
Real-Time Supersession Updates
Intelli Catalog keeps a detailed log of part updates, flagging superseded parts with a clear change symbol denoted by ‘H’ (stands for parts history) in the interface. The dashboard mentions information like the start and end dates, which indicate the duration for which that particular part was available and its pricing. It also mentions the most current replacement available, with an adjacent add-to-cart option allowing dealers to place an order.
Supersession modifications immediately reach all the dealers in the OEMs' network using a centralized cloud platform. When a part number changes due to an upgrade, dealers see the new version instantly, along with cross-referencing data to confirm compatibility. Instant access to the most recent part numbers eliminates the need for dealers to wait for an updated catalog, avoiding costly misorders while also saving time.
Business Benefits of Effective Parts Supersession Management for OEMs
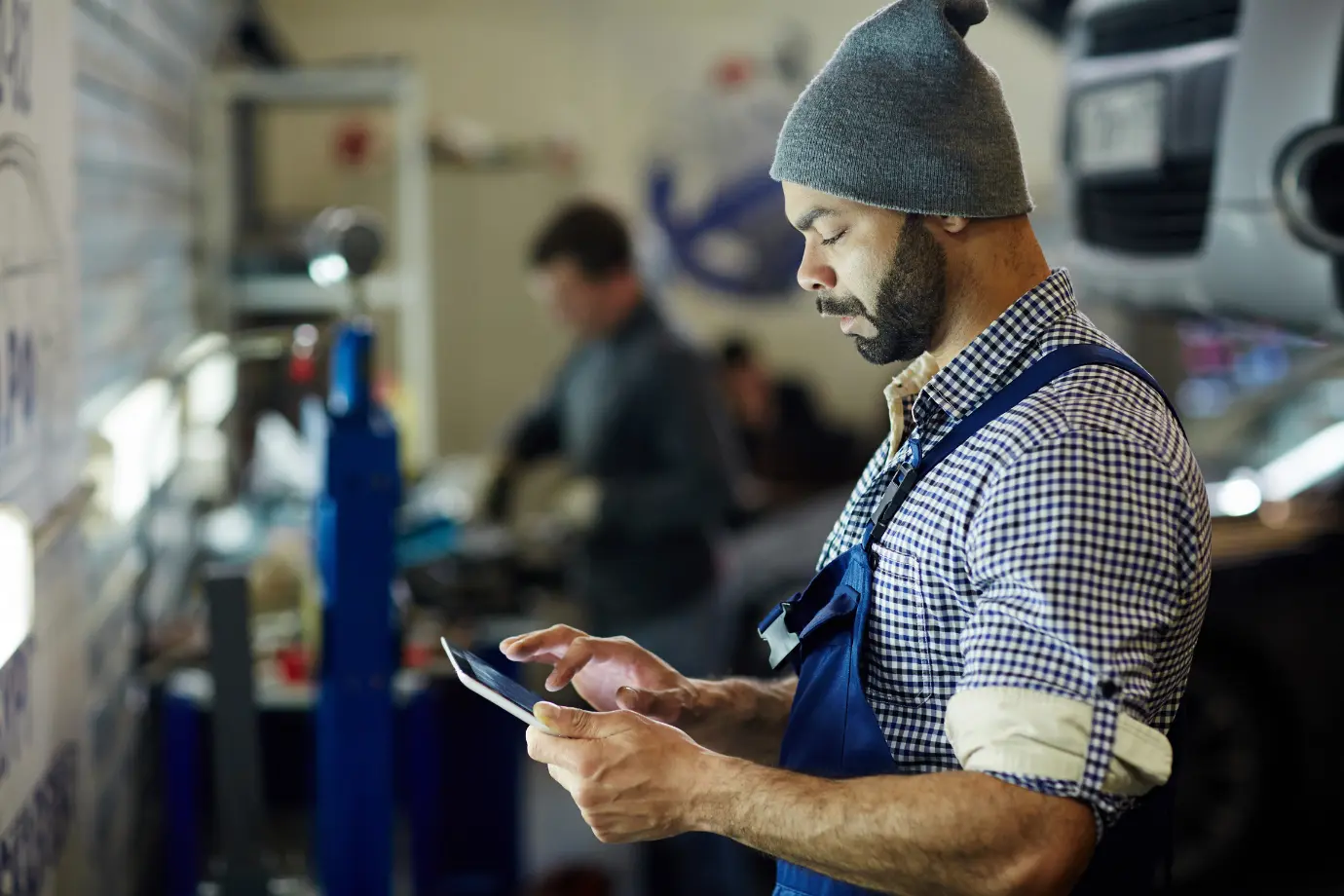
Beyond just preventing errors, the OEMs' goal behind mastering parts supersession is to build a better business. Using solutions like Intelli Catalog helps OEMs modernize their operations and gain benefits that range across the supply chain.
Some significant benefits OEMs acquire through effective parts supersession management include:
Improved Efficiency
Real-time data and smart searches mean dealers spend less time hunting for parts and more time serving customers. Implementing advanced software like Intelli Catalog helps dealerships minimize order processing time and boost their team’s efficiency.
Costs Savings
Fewer parts misorders translate to fewer returns, restocking costs, and lost inventory. Digital systems also eliminate the need to print and distribute bulky catalogs.
Improved Customer Experience
When dealers get supersession right and provide the right parts on time, customers notice. A happy customer eventually becomes loyal to the brand, and dealerships get returning business.
Competitive Advantage
In cutthroat markets like automotive or aerospace, OEMs who master supersession management stand out. After using Intelli Catalog to streamline their components process, a tractor manufacturer saw a 20% boost in dealer loyalty.
Must Check:
A Complete Guide to Electronic Parts Catalog Software
Takeaways
Poor parts supersession management results in misorders causes delays, and frustrates customers. OEMs can prevent several adverse impacts on their operations by mastering parts supersession and addressing these issues head-on.
The fast-moving inventories of today cannot be handled by traditional techniques of parts supersession management, such as paper catalogs, scrawled notes, and lengthy emails. Intelli Catalog offers a robust solution with real-time updates, clear visuals, and integrations that keep everyone informed. It's about fostering efficiency and trust across the supply chain, not just about preventing errors.
If you’re done with troubles associated with managing spare parts, connect with our experts and get a free demo on how Intelli Catalog can change the game for your business.
Explore More Insights
About the Author
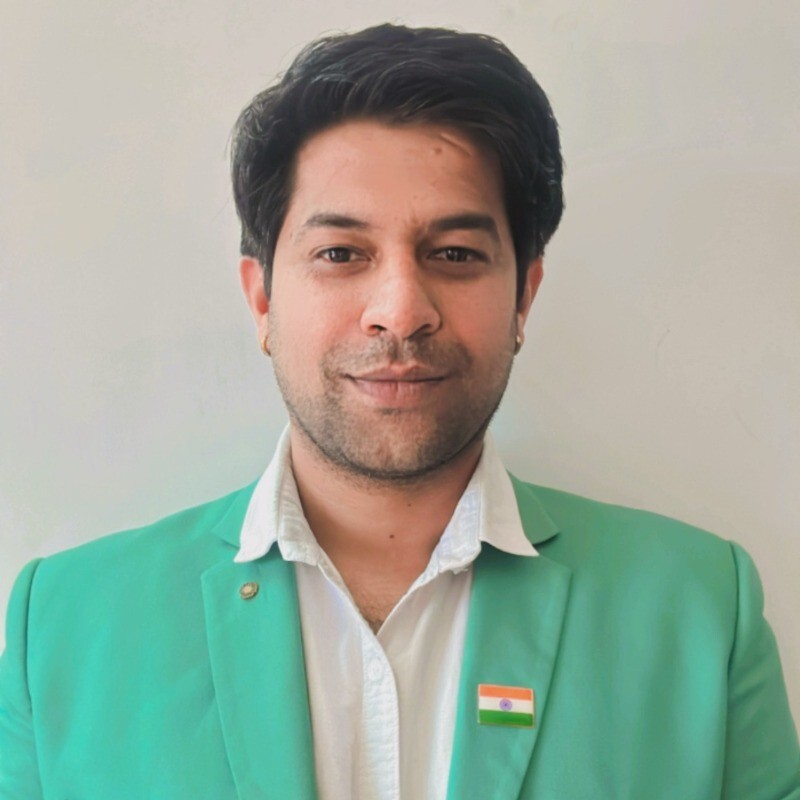
Chandra Shekhar
Chandra Shekhar is the Senior Manager, Strategy & Business Development at Intellinet Systems. With over a decade of experience in the automotive industry, Chandra Shekhar has led digital transformation and aftersales strategy initiatives for OEMs across multiple markets. His background combines deep industry knowledge with a practical understanding of how technology can solve real operational challenges. He focuses on making complex ideas clear and relevant for automotive and aftermarket professionals navigating ongoing change.