In a time where technological advancements have made businesses choose a digital approach to streamlining the company processes and improve overall efficiency, digital advanced inspection software acts as an enabler to companies across domains to improve their processes, streamline operations, and enhance quality control. That being said, it is crucial to choose the right inspection software that caters to the unique needs of an organization. Let us now discuss the need and also what are the factors to consider when choosing the right vehicle inspection software.
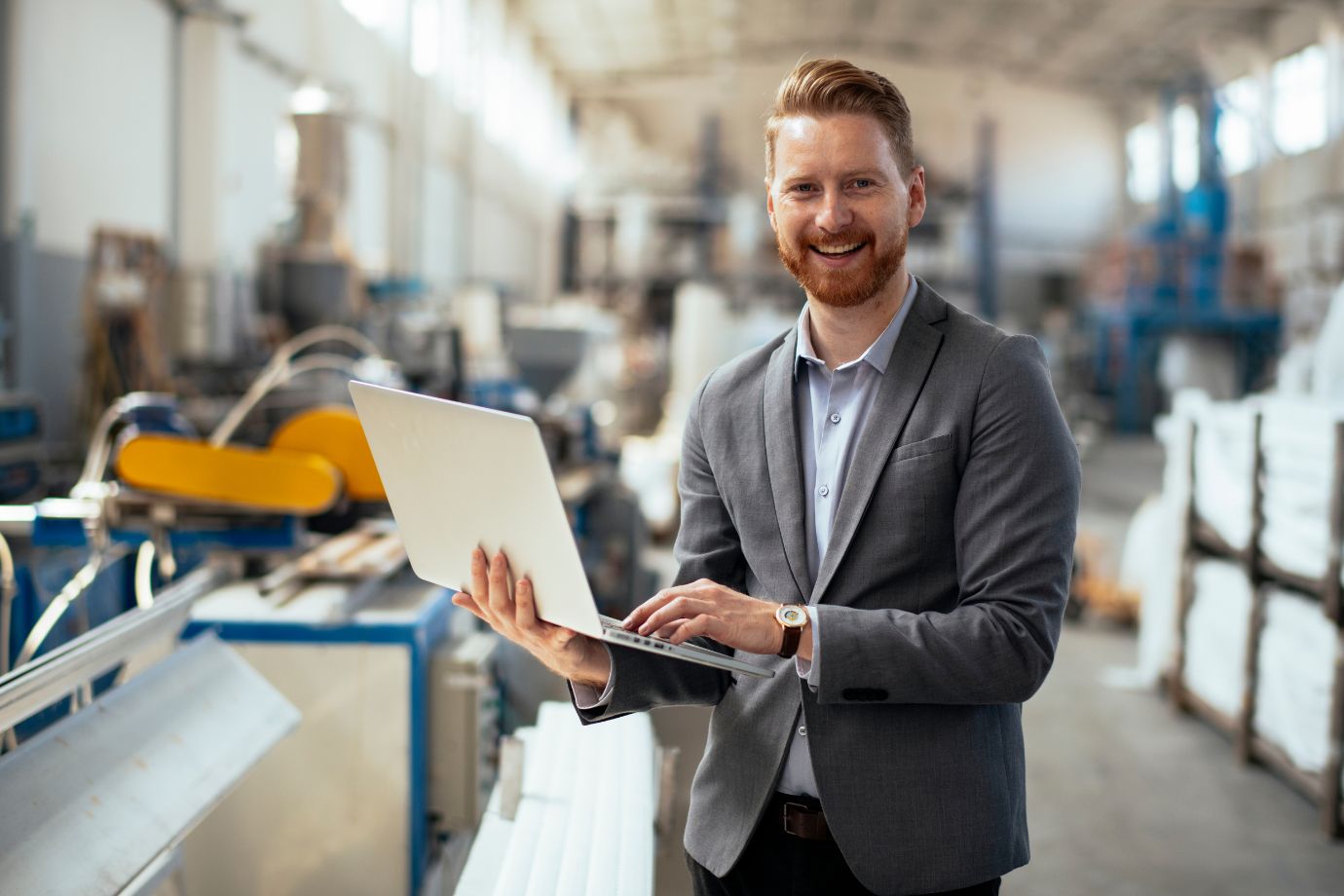
Understanding The Need for Vehicle Inspection Sofware
Before we get into the vastness of vehicle inspection software, introspection is required by businesses to assess their needs. Businesses across domains have unique demands and challenges that necessitate tailored functionalities in digital inspection software.
Assessing Industry-Specific Needs: When we talk about industry-specific needs, each industry has a specific set of challenges that require assessment. For example, a manufacturing company might have challenges related to precision in measurement tools and compatibility factors with existing machinery. A healthcare company might have compliance and regulatory challenges. They also might have challenges related to the storage of patients’ health data.
Identifying Pain Points: Identifying and pinpointing the existing inefficiencies in businesses guides companies in understanding the specialized or tailored needs they might require from digital inspection software. It could be challenges like improving the inspection time, improving accuracy, or ensuring compliance, these requirements form the basis of choosing the right inspection software.
Features and Functionalities
Customization and Flexibility: An adaptable vehicle inspection software that enables the alignment of customizations with changing and evolving industry standards and business-specific requirements is crucial. Versatility is ensured when the features needed by a business can be incorporated and tailored to accommodate processes or types of inspection.
Integration Capabilities: The perfect fit of digital inspection software is when it seamlessly integrates with existing systems and processes. If there are compatibility issues, it can cause disruptions in operations and reduce the efficiency of a business.
User-Friendly Interface: To make the most of digital inspection software, it must have a user-friendly interface so it is used with ease by the employees which in turn reduces the time taken to learn and adapt and maximizes the productivity of businesses.
Data Analytics and Reporting: Analytics and reporting are of utmost importance in today’s time as they provide an in-depth understanding based on business-specific data. This data is collected through inspections and enables businesses to make data-driven decisions that are aligned with business goals and ensure business success.
Compliance and Security
Many businesses follow stringent regulations and standards. It is non-negotiable for businesses to deviate from adherence to these regulations. Any digital software that is chosen by an organization must adhere to these industry-specific regulations and standards. These encompass all aspects of regulations and ensure that the inspections and management of data are aligned with legal as well as business standards.
Adherence to Compliance and Regulations: Every industry is required to adhere to certain regulations and it is a non-negotiable aspect for manufacturers. When we talk about the compliance and adherence aspect of businesses, it not only hampers the quality of their product but also the user experience and harms brand loyalty. Every industry has to maintain a strict compliance policy, a pharmaceutical company would require an FDA regulation and also comply with HIPAA guidelines. Similarly, a manufacturing company would require adherence to ISO regulations. These regulations lay out a foundation to standardize and follow quality control measures.
Data Security Measures: Data security is also a non-negotiable aspect for OEMs. As businesses today work with huge amounts of customer data, it is empirical to safeguard and control access to such information. There must be security standards in place and businesses must maintain a robust and secure encryption. Digital inspection software follows adherence to security standards and ensures that access to such data is restricted. By making policies and ensuring cybersecurity, digital inspection software is the solution that companies look for to maintain a safe and secure data protection environment.
Scalability and Support
Scalability: Scaling a business is often a challenge and most businesses understand the importance of keeping in mind the future business plans. To choose the right digital inspection software, OEMs have to look at its features and capabilities and check if they are aligned with their business goals. If we take an example of any OEM, they already would have existing systems in place. Introducing a new software is a challenging task and they should consider the long-term applications for its introduction. They also need to understand if the digital inspection software can handle an increased load of work as the company grows and whether it can be integrated with new systems.
Support and Maintenance: Every OEM understands the importance of support and maintenance as everything depends on it. If companies fail to keep such a system in place, operational and customer service will take a huge hit. This would hurt the brand image reduce sales, decrease customer satisfaction, and result in huge revenue losses. OEMs must have a support and maintenance system where they can schedule the downtime processes and also provide both technical and non-technical assistance. To ensure that operations are smooth, they must have mechanisms in place to deploy updates in a regularised manner to ensure compliance and security as well.
Conclusion
OEMs experience a heap of challenges in their daily operations and must find solutions in real-time so that the operational flow is not hampered. There is meticulous evaluation needed to cater to needs as they are as unique as a business. OEMs would also require functionalities as per their processes, for example, a medical device company's requirements would be very different than an automotive OEM. Many companies might choose digital inspection software which has a heap of features, but they need to understand if those features add any value to their existing processes. The decision to choose the right digital inspection software is crucial and must be decided after internal and expert discussions and consultations.
Explore More Insights
About the Author
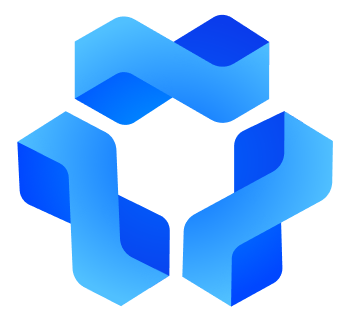