It is very important to know that, field issue resolution is considered to be very crucial for the enhanced success of the OEMs (Original Equipment Manufacturers). Effective and timely solutions to field issues ensure immense customer satisfaction, which maintains the proper brand reputation and also fosters the right customer relationships. By rightly and timely addressing the field issues with field technical report, the OEMs can easily demonstrate the commitment to reliability and quality, which includes the right diagnostics, technical assistance, and effective repair and replacement services.
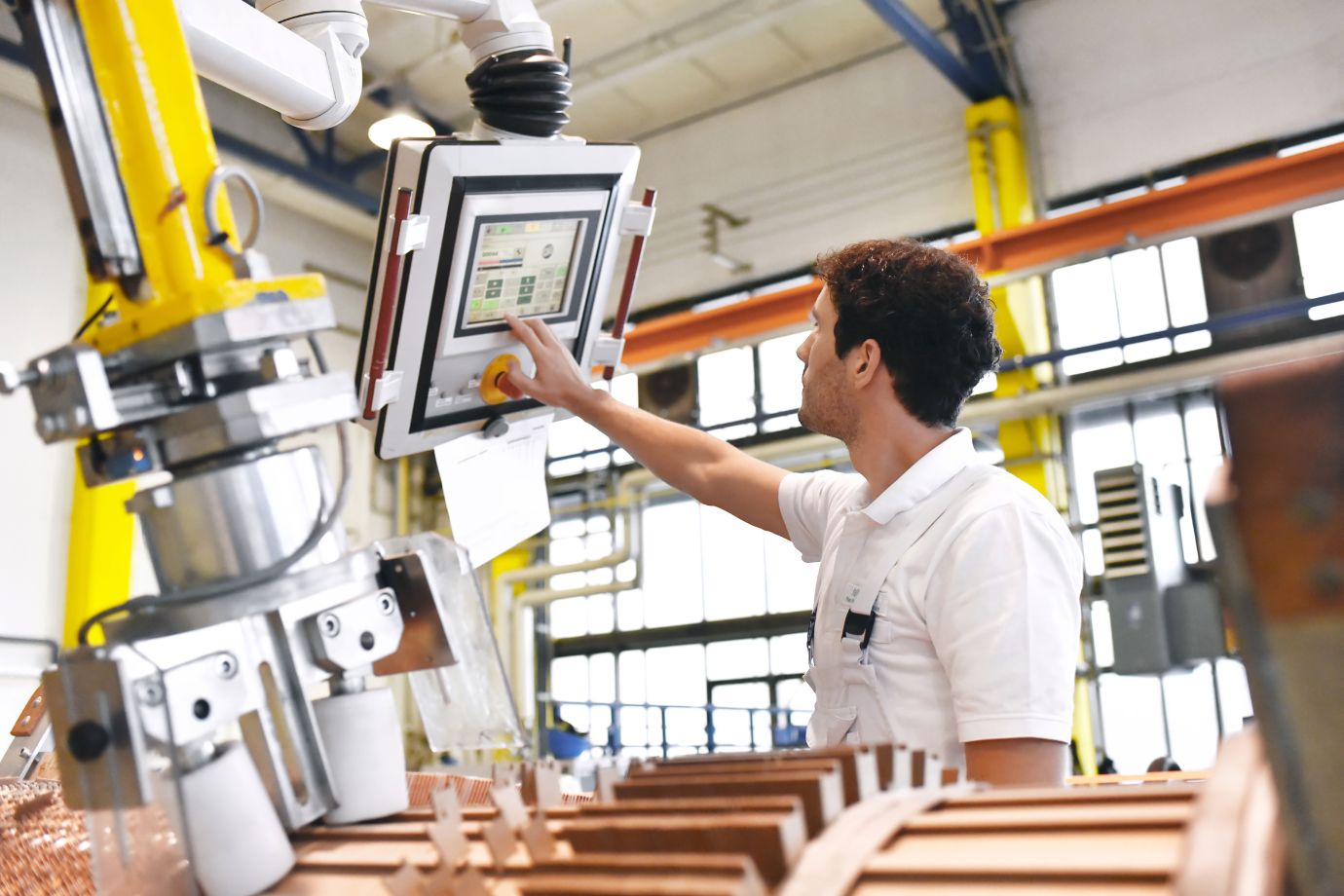
Effective Software That Can Help Manufacturing Companies With Automating Field Issues:
Increased Productivity And Efficiency
The field issues that are handled by manual processes can be both prone to errors and also time-consuming. Automating the field support task does allow for increased efficiency and streamlining of workflows. With the right field supportive software, the manufacturers can easily automate the work orders, monitor progress, and track issues.
Dealers to Service Managers - Centralized Communication
Having the right software is crucial, as it helps the dealers to have centralized communication with the service managers for reporting field issues. These kinds of service managers try to resolve the different issues, by using their knowledge and expertise, in case of any issues, and can easily connect with the team.
The back-end office teams are received by different issues, hence the help of the software helps in the right processes.
Real-time Analytics and Data
Automation helps manufacturing companies collect and analyze real-time data which is related to field issues. Field support software helps in capturing information on the frequency and types of issues, resolution rates, customer feedback, and response times. This is the kind of data that provides very valuable insights into the recurring issues and also identifies the improvement areas.
With access to the up to date and accurate analytics, it helps manufacturers make informed decisions, by implementing the right solutions and very proactively addressing the escalations. By leveraging the insights, companies can easily optimize their processes and operations, enhance performance, and minimize downtime.
Request Resolution & SLA Insights
Automating the field issues via technical helpdesk support, helps the management provide valuable insights into the compliance of SLAS (Service Level Agreement). Supporting software implementation, it helps stakeholders, providing a quick turnaround time by the OEMs for request resolution. This way the manufacturers get visibility into the response time, adherence to the SLA commitments, and resolution rates.
This is known to be a data-driven approach that helps with the quick management of field issues, helps in identifying the bottlenecks, and also ensures the timely completeness of the services. With the help of SLA insights, the manufacturers can help with optimizing the allocation of resources, maintain customer satisfaction, and improve response time.
Quicker Response By Task Prioritization
With the help of automation, it becomes easier to prioritize tasks, which leads to a quick response and improved resolution of resources. With the automated software, the manufacturers can assign the right priority levels to the field issues, based on urgency and impact in the FTR and TAR submissions. This process allows all the support teams to focus on very critical issues and allocate resources as and when needed.
Prioritizing tasks helps with issues that are of high priority and receive immediate attention, customer disruptions, and minimizing downtime. By prioritizing tasks, manufacturers can effectively optimize workflows.
Improved Customer Retention & Satisfaction
For all manufacturing companies, customer satisfaction should always be the top priority and hence, promptly resolving field issues plays a huge role in this. Companies can easily provide fast responses, efficient resolution with automation, and accurate issue tracking. This overall leads to enhancing customer satisfaction.
Automation at every level also helps with personalized customer interactions, by capturing customer preferences. This allows the experts to provide personalized and tailored solutions.
Bottom Line
Manual field issues handling does result in resource inefficiencies and increased costs, and this is where automation helps manufacturing companies optimize costs and resources. Manufacturing companies with automation can reduce paperwork and minimize errors. Automation also helps with better visibility in the spare parts inventories which prevents stockouts and overstocks.
Hence, real-time analytics and data, help companies to reduce cost, eliminate all unnecessary experts, and optimize resources.
To learn more about aftermarket software solutions. Visit our website.
Explore More Insights
About the Author
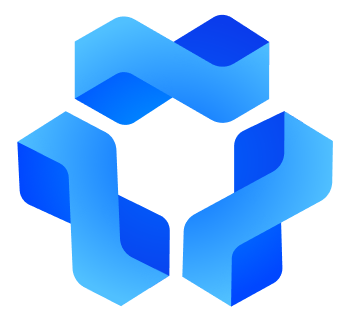