To investigate the cause of the product defects and malfunctions, Original Equipment Manufacturers (OEMs) need to acquire them back. While this possession is essential for product enhancement, especially when covered under warranty, OEMs incur huge costs in managing these warranty parts returns. Parts return management involves multiple stakeholders, which makes it a complex process. In this process, OEMs face challenges like delayed approvals, inefficient logistics, and escalating costs. This strains the manufacturer’s resources and also degrades the OEM’s brand reputation in the market.
To overcome these difficulties and challenges, warranty parts return management software came into existence. Software like Intelli RMS helps manufacturers manage the end-to-end process of parts return. Examining the root cause of malfunctions and defects in these products enables in prevention of such instances in the future and improves product quality and reliability.
Through this article, let’s understand how Intelli RMS facilitates warranty part returns for OEMs to minimize operational inefficiencies.
Introducing Intelli RMS
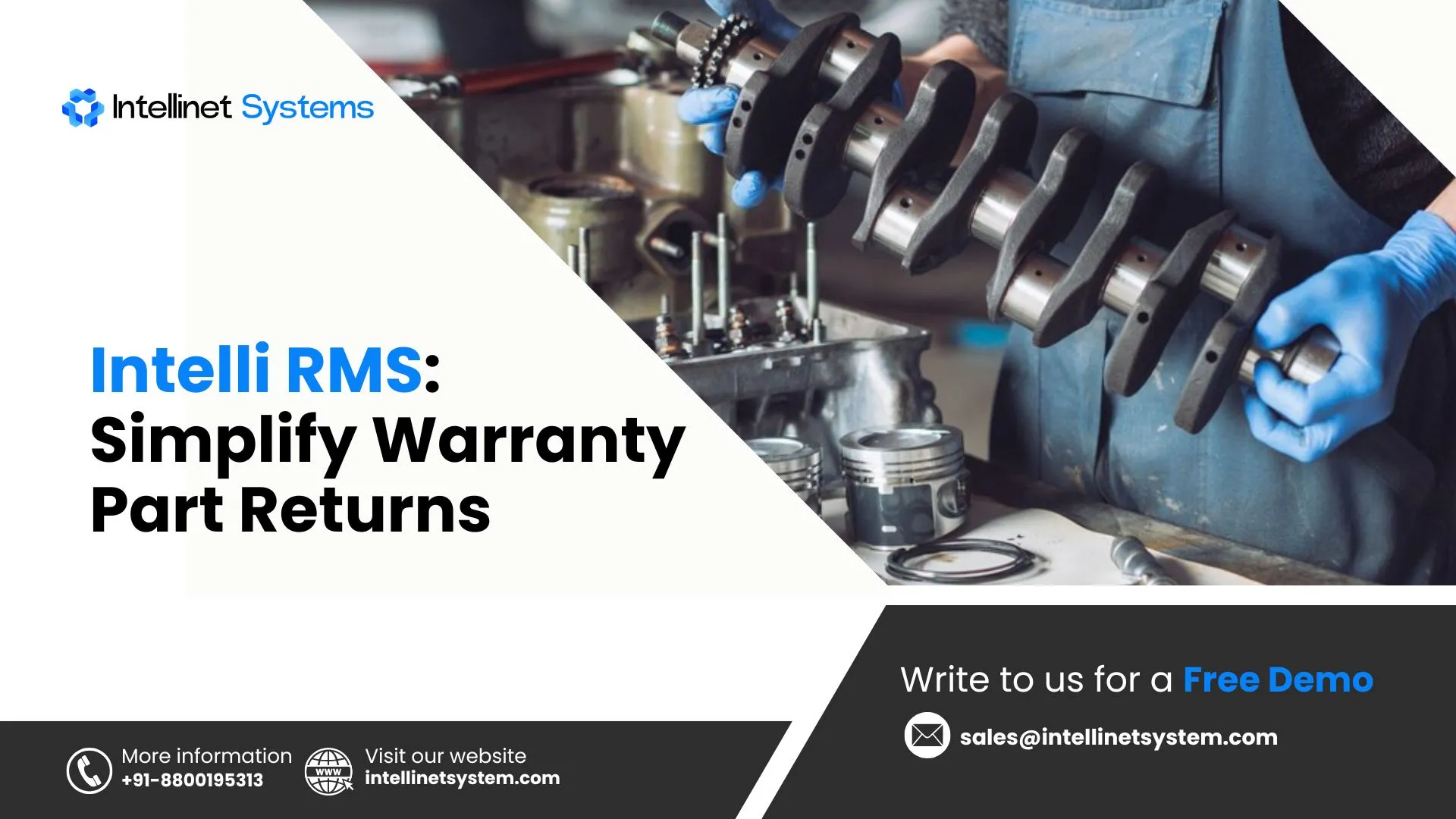
Intelli RMS is a parts return management software that streamlines the return process of spare parts covered within warranty. The software provides an end-to-end solution for the entire process, from generating a return request to logistics and parts delivery.
Parts return management is a process where the OEM recalls the malfunctioning or defective parts to understand the root cause of the defect. All the costs involved in this process, which aims to increase operational efficiency, are borne by the manufacturer.
Intelli RMS involves the following 4-step approach when managing returns of spare parts:
1. Return Request Placed by Requester
When the R&D team has to investigate the cause of defects or malfunctions occurring in the product, they may raise a return request for the same. While filing the return request, the requester can choose any dealer to source the product from. This request may include details like the name/number of the defective parts, their quantity, and digital images for validation.
2. Verification and Validation by the Return Center
The return centre authenticates the request to ensure the product details provided are correct and complete. Once the details are authenticated, the return center approves the request, and the part return process is initiated.
3. Automatic Notification to the Dealer and Carrier
For all the approved requests, the dealer and logistics carrier receive an instant notification with a system-generated label to be included with the shipment. The dealer attaches the label to the return shipment, which is then picked up by the carrier partner.
4. Inspection of Returned Parts
Once the shipment reaches the return center, the team verifies the parcel through the barcode. The R&D team acquires the part and performs a technical inspection to analyze the root cause of the defect/part failure. This inspection helps identify why the part malfunctioned and determine possible solutions to avoid such a situation in the future.
The R&D team performs quality checks to identify instances of damage or wear and tear. Based on their analysis and findings, the R&D team may suggest part replacement or changes in the part design.
Features of Intelli RMS
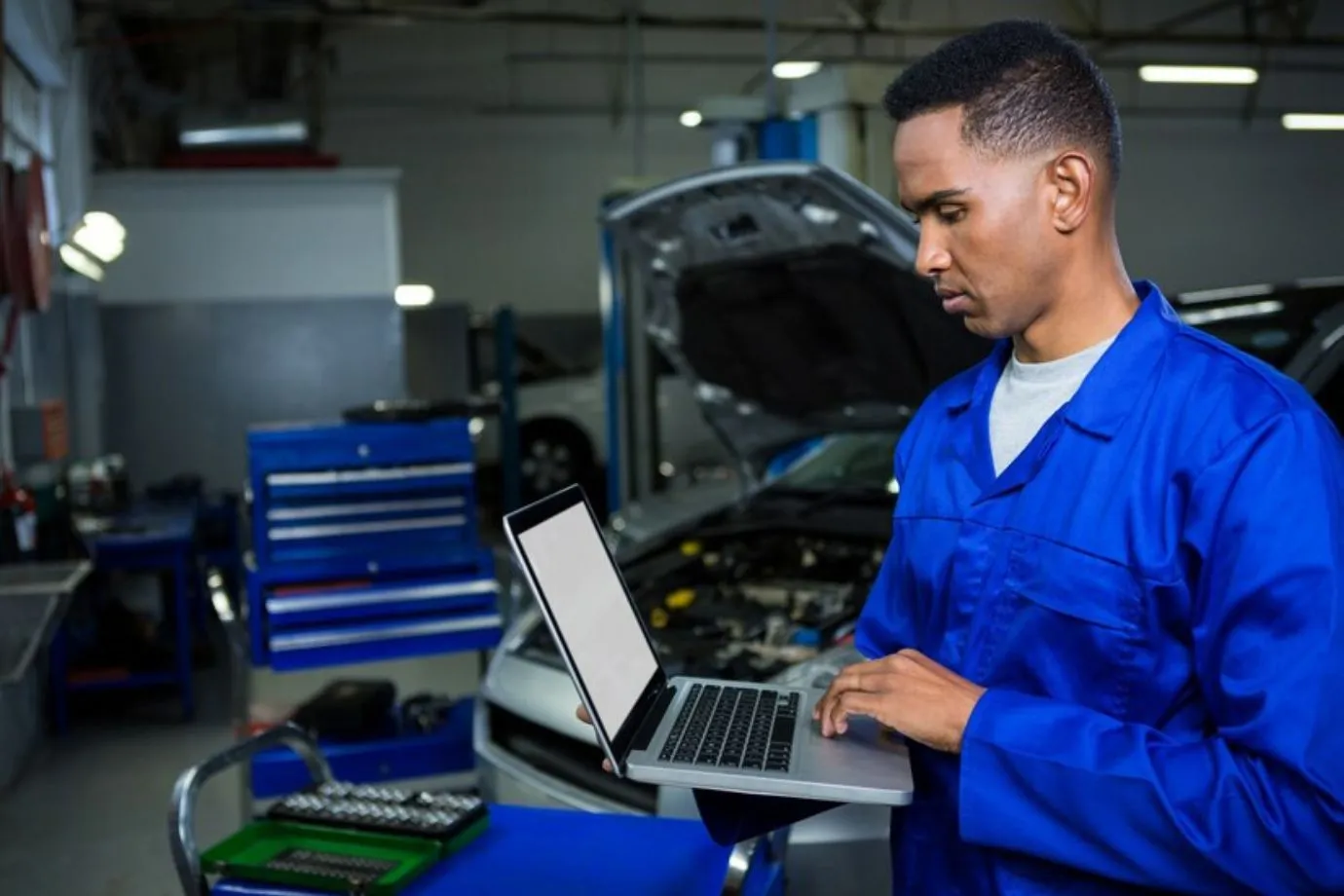
To facilitate the warranty parts return process, Intelli RMS is packed with innovative features, including:
- Integrated Call-Tag Mechanism for Carriers: Generate and attach shipping labels effortlessly, simplifying logistics and reducing manual errors.
- Auto-Tracking of Shipments: Real-time tracking ensures complete visibility of returned parts throughout the supply chain.
- Return Request Generation with Digital Images: Enhance request accuracy by including digital images, enabling faster validation. The software enhances request accuracy by including digital images, helping the returns centre to validate return requests faster.
- Dedicated login for reviewers: Secure login access for each reviewer helps streamline the research process of product defects and malfunctions, and ensures their accountability.
- Multiple shipment services: OEMs can flexibly choose from leading carriers like FedEx, UPS, and TNT to ensure cost-effectiveness.
- Bulk Excel uploads: Requesters can create multiple return requests simply by importing data from Excel sheets. This helps them reduce the risk of errors while also saving their time considerably.
Benefits of Intelli RMS for the OEMs
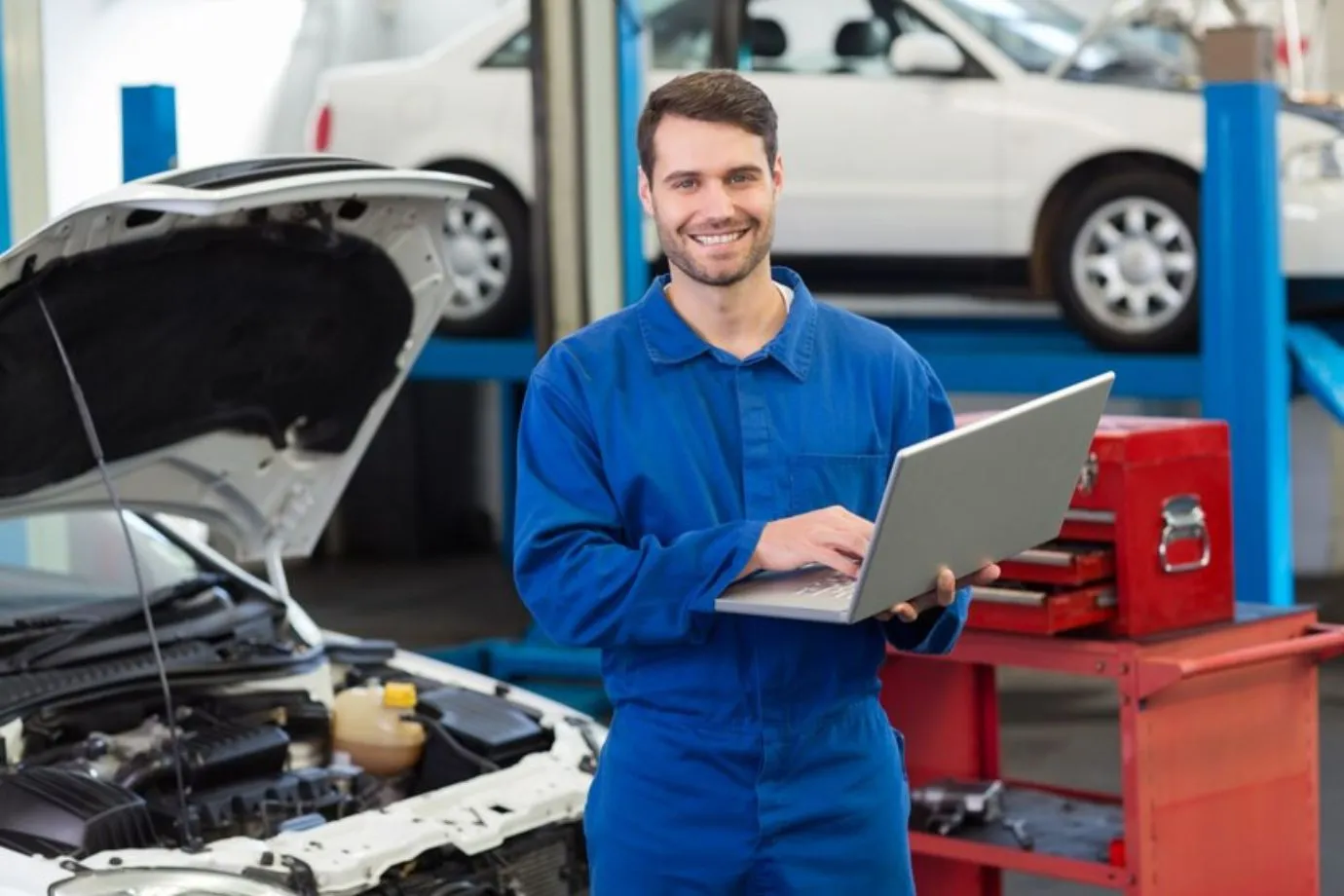
Intelli RMS offers the following benefits to the OEMs:
1. Simplify the Return Process
Automated notification processing between the dealer, logistics carrier, and return centre eliminates the need for manual documentation. This helps in streamlining workflows while reducing turnaround times and operational burden.
2. Allocate Resources Efficiently
OEMs can automate tasks such as carrier selection and package labeling, helping them free their teams for more crucial tasks. This enables the OEM to focus on core operations and efficiently optimize resource allocation.
3. Simplify Logistics and Save Costs
Intelligent logistics carrier selection ensures that the OEM spends the minimum price on logistics costs. Real-time shipment tracking also minimizes waiting times and promotes cost-effectiveness.
4. Use Data-Driven Insights for Product Enhancement
Upon successful analysis, Intelli RMS allows the reviewers to add suggestions based on their findings. This documentation provides insights to the OEMs for product enhancement. After careful analysis, the manufacturer can initiate product improvements such as design modifications and enhance product reliability.
5. Collaborate with Stakeholders Simultaneously
OEMs can connect with their dealers, suppliers, and carriers on a centralized platform. This aids them in improving transparency and communication across the supply chain.
Conclusion
An efficient warranty part returns management is a necessity rather than a luxury for the OEMs in today’s competitive landscape. It helps them manage aftermarket operations and maintain customer trust. This is when Intelli RMS turns out to be more than just a software.
It helps manufacturers simplify parts returns, enhance product quality, and reduce operational costs. Intelli RMS automates tasks like label generation and notifying the logistics carrier. Its real-time shipment tracking helps manufacturers reduce turnaround time.
To know more about how Intelli RMS can streamline warranty parts return management for your business or request a free demo, connect with our experts today.
Explore More Insights
About the Author
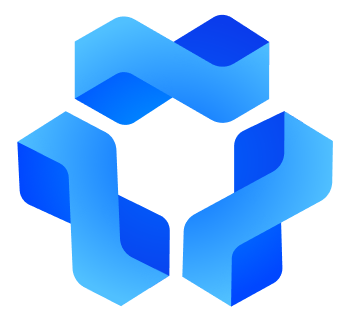