Effective management of your spare parts inventory is essential for your business, no matter which industry you come from. You can rely on the spare parts catalog software to ensure seamless operations and reduce downtime.
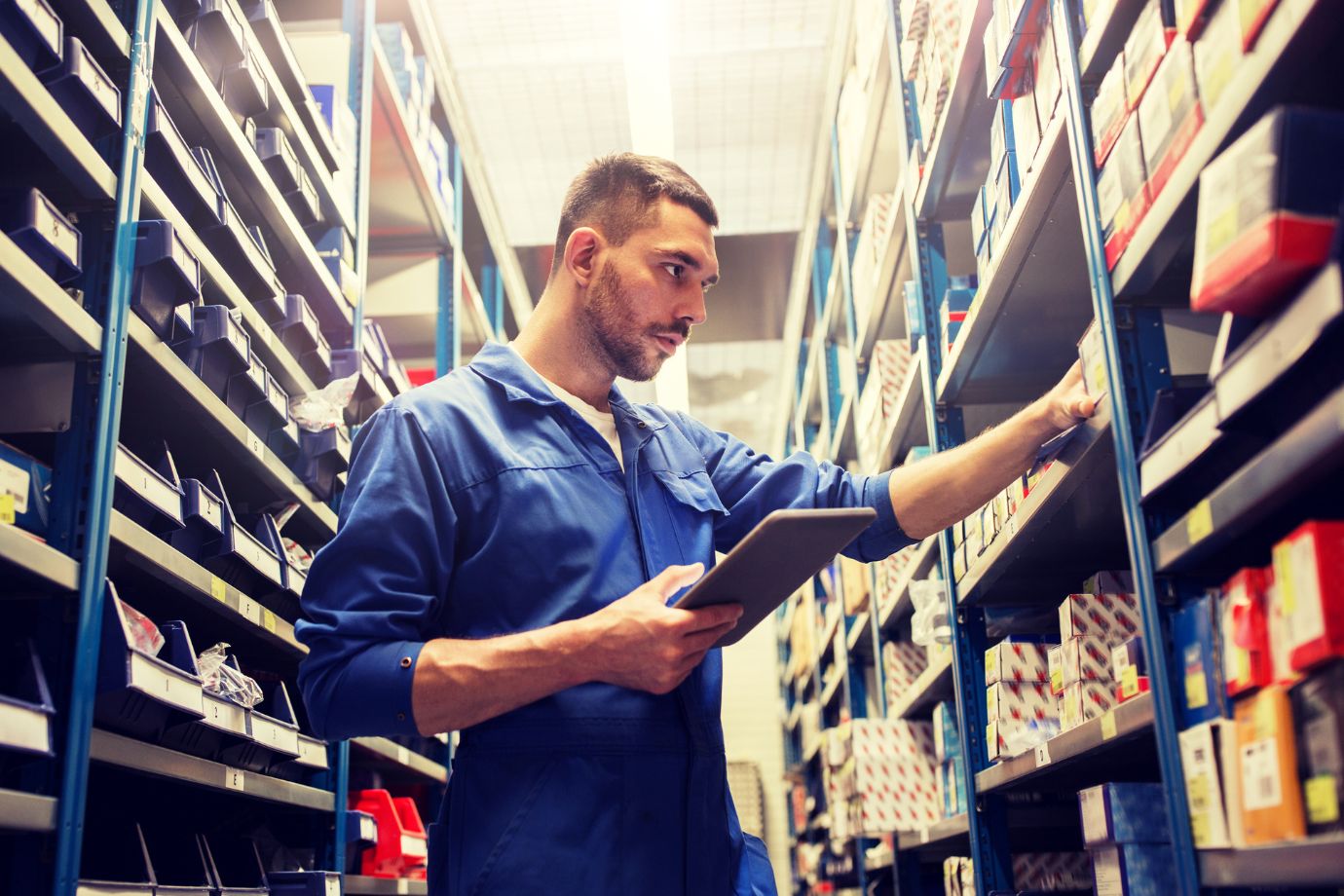
4 Spare Parts Inventory Management Best Practices
Systematically Identify Your Parts
The first step you need to do in managing your spare parts management system is to identify all the parts systematically. You must create a comprehensive inventory list with detailed information, part numbers, descriptions, or specifications. Instead of storing these unused parts in random locations like boxes or cabinets, you must incorporate them into the inventory control system and add them to the parts inventory.
So these items can be effectively managed and made available for use in other equipment. This is the kind of practice that helps ensure the list remains organized for the long run. It can easily minimize the risk of misplacement or losses and maximize the utilization of spare parts through the facility. Integration of the unused parts in the inventory control system can promote inventory management and facilitate easy access, which improves the maintenance and operational efficiency of the plant.
Material Bill and Use
The material bill is considered to be an essential part of the spare part inventory management. This is the method that provides a detailed breakdown of those elements required for the manufacture of the final product. By usage of the model in the spare parts inventory software, it is easy to keep the tab on the aspects that facilitate effective recruitment and minimize inventory excess. An accurate material bill is essential in promoting preventive maintenance for specific equipment.
In a few systems, the preventive maintenance schedules automatically an order that includes designated preventative maintenance dates. Integration of the preventive & model maintenance scheduling the maintenance operations which ensures the repairs & inspection. By using accurate building material models and automating the preventive maintenance work orders, you can effectively manage your maintenance activities, which maximizes operational efficiency & equipment downtime.
Use The Inventory Control System
You should invest in spare part inventory software which offers robust inventory control measures. This software allows keeping a stock level in real-time & provides automatic reorder notifications. It is essential to check for reporting comprehensive capabilities. The inventory control system ensures accurate stock management, which reduces stock-outs and prevents overstocking.
By making use of barcodes and functionality scanning with the systems, companies can easily improve their processes, for achieving great accuracy in inventory. The usage of barcodes allows quick and accurate parts identification, eliminating the different data entry, and can expect preferred tasks for inventory management.
Stock Location For Parts
It is very important to assign a location to the specific stock for every inventory for streamlining the storage process. This also ensures that employees can easily locate and retrieve the parts while minimizing wastage of time and increasing operational effectiveness.
To overcome the challenge, it is essential to implement the recommendations. First, adopt precise identification systems by making use of designated areas in the shared shelf. This allows for quicker identification of required parts.
Bottom Line:
Hence, spare parts inventory management is considered to be crucial for maintaining reduced downtime and seamless operations. The success of each and every spare parts inventory management relies on the right implementation by utilizing software that is customized as per the firm needs.
To learn more about aftermarket software solutions. Visit our website.