Warranty management system can be a major source of cost savings for companies, but it can also be a source of better brand integrity, customer experience and loyalty. Consumers need assurance that the product will perform satisfactorily over the complete lifecycle. Manufacturers have option to respond such challenges by offering warranty management system and extended warranty solutions. A warranty is a legal contract which requires the manufacturer to either rectify or compensate for all failures occurring within the warranty period. There are many different aspects to warranty management system and these have been studied by researchers from many different disciplines.
Offering a warranty claims management solution may results in additional costs (referred to as warranty servicing costs or simply warranty costs) to the manufacturer as all failures under warranty need to be either rectified or compensated by the manufacturer. The warranty costs depend on the reliability performance of the product. This in turn depends on several factors some under the control of the manufacturer such as the decisions made during the design and development. This implies, reliability of product and warranty both are very important.
Manufacturers often look for options to offer their clients a longer limited warranty yet transfer the risk to a solid insurance company or services contract provider.The motive behind searching option is that the options can work well with new technology items where the product manufacturers want to focus on the design of their product, highly competitive industries where a longer "backed" warranty management solution offers a competitive differentiation or where a consumer wishes to offer a warranty as long as the consumer is a subscriber or member.
For instance, electrical equipment and appliance manufacturers, using warranty management system to improve customer experience, which can increase the likelihood of being a top performer in customer satisfaction by up to 12%.
Another area that can be examined through warranty claims management is fraudulent claims. Identifying fraudulent claims prior to payment minimizes financial losses and reduces warranty cost – a 3% reduction in fraud on a warranty cost of $100m is $3m. Also, according to recent research on an average 8.1% of warranty claims are rejected by electronics product manufactures for being fraud.
Warranty management solution will surely benefit OEMs and dealers of manufacturing industry. Not only they will make a positive impact on the operations but they will also improve warranty management. About half of them are relatively straightforward to implement.
Also, connecting manufacturers to internet, and including the capability to collect and analyze the data for their equipment.
It’s one thing to have a service person collect data from individual machines when those machines are serviced. Imagine if all machines, faulty or not, are sharing their data with the company via the internet, all the time. It could save a client company a tremendous amount of money if they can detect that some of their parts are going to fail, and take action to prevent that, instead of waiting for them to actually fail.
By integrating "IOT" sensor data provided through Internet connectivity into warranty management system and processes, companies may take advantage of new business and operational opportunities. An example is embedding sensors and internal diagnostics into washers and dryers. Once that sensor data is made available, using internet connectivity, there are lots of ways it can be used:
To Improve Product Quality and Future Designs
The data can provide an understanding of how products are actually being used by customers — more specifically, which features and functions are popular and which are not.
To Reduce Warranty Cost
When one of these machines generates an error code, the machine can pre-diagnose the error. This can save time, money and frustration – it’s the difference between making a very specific repair, replacing the exact right part(s).
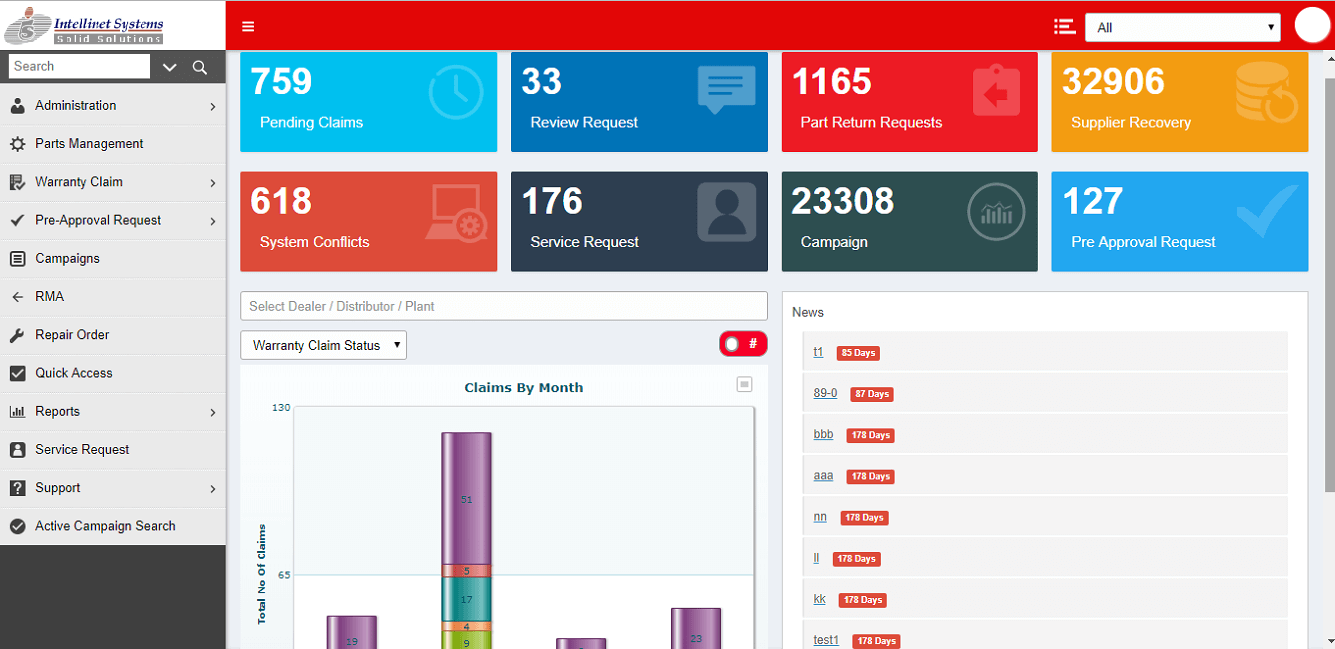
Intellinet has come up with such an idea after market research and analyzing the needs of manufacturers of various fields. By adopting warranty management system processes, they’ll gain the capability to integrate an additional, immensely valuable set of data that will improve their analyses and provide new insights. In turn, this can lead to enhanced support processes, optimized product service, and the provision of new and differentiating experiences for customers, all of which lead to improved revenues.
The main focus is to increase brand value and market capital of an organization through their warranty management system. The software is capable to provide warranty to mostly all types of equipment manufacturers. Have a look at the list given below.
- Automotive Warranty Management Solutions
- Electronics Parts Warranty Management Solutions
- Computer Parts Warranty Management
- Warranty Management For Mobile Spare Parts
- Warranty management software for Farm Equipment
- White Goods Warranty Management System
- Warranty Management Solution For Extrude
- Warranty Management Software For Agriculture Equipment
- Warranty Solutions For Custom Commercial Products
- Warranty Management For Exercise and Sporting Equipment
- And Warranty Solutions For Automotive, Power sports and Marine Products
WMS doesn’t only affect the manufacturing OEMs but also the entire value chain. The importance of suppliers in product design, development and manufacturing is well recognized. Yet, access of suppliers was very low till before this. But after introducing the software like warranty management system the business goals can be effectively accomplished and support the future needs also.
Intellinet Systems offers warranty management system and also develop custom warranty management solutions to extend the limited warranty or create Service Contract (Extended Warranty) programs. It offers you the right parts and service solutions, when and where you need them. The network of highly trained experts keeps your entire fleet up and running to maximize your equipment investment.
For more queries about the software please click here:
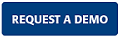
Explore More Insights
About the Author
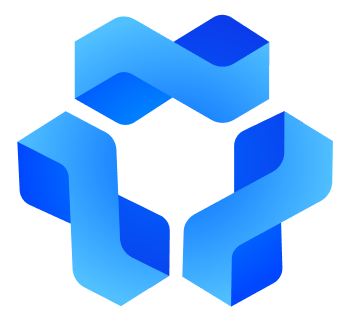